Advancing Production Capabilities through ERP and MES Integration
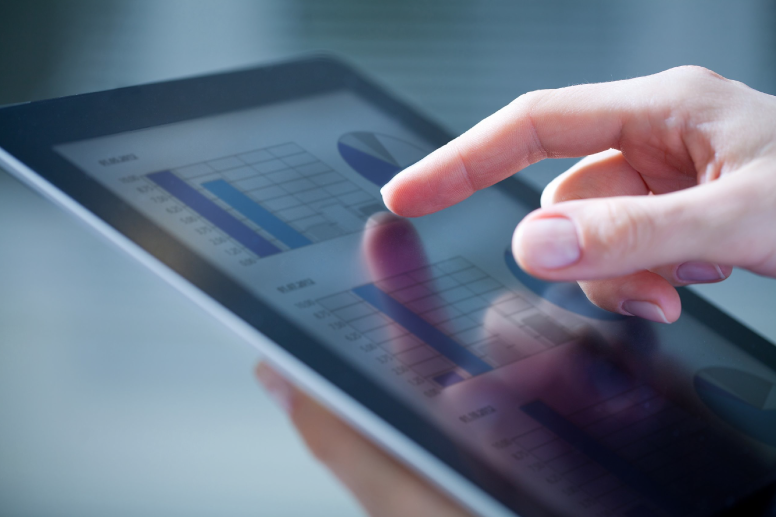
Advancing Production Capabilities through ERP and MES Integration
ERP and MES integration can open new avenues in manufacturing, giving you real-time oversight that enhances strategic decisions. Production floors often rely on a combination of hardware and software to manage everyday tasks, so a unified approach simplifies oversight at all levels. Operators gain an immediate understanding of inventory requirements and scheduling, while managers receive a clear view of resource allocation. This targeted efficiency supports faster releases and drives significant returns for stakeholders.
Global shifts highlight the importance of digital connectivity in production. Pressure to reduce costs, shorten lead times, and remain flexible often relies on integrated solutions that deliver insights around the clock. A well-planned connection between these systems introduces consistent workflows and minimized manual data entry. Many organizations are seeking a fully coordinated system that fosters greater collaboration, higher throughput, and measurable performance gains.
Understanding ERP and MES Integration in Manufacturing
Manufacturers often rely on distinct systems to manage production and administrative tasks. ERP and MES integration is critical for bridging this gap, allowing data to flow seamlessly across the entire operation. Managers who implement these solutions gain real-time access to production metrics, labor efficiency reports, and billing details. This synergy reduces errors from manual data entry and strengthens overall production control.
Integrating both platforms also improves traceability and compliance efforts. Quality checks become more accurate, and historical records remain at the ready for audits or product investigations. A connected ecosystem fosters better collaboration between departments, leading to consistent results and stronger process improvements. Organizations that invest in a robust approach to merging these systems often spot new opportunities for scale and efficiency.
Key Benefits of Integrating ERP and MES
Many leaders strive to unlock the full potential of manufacturing operations. A unified platform serves as a launchpad for streamlined workflows, cost-effective processes, and better control over raw materials. Consistent data sharing between MES and ERP eliminates misinformation and enables stable outputs. This approach can lower administrative burdens and free up resources for strategic objectives.
- Enhanced visibility: Operators and supervisors receive immediate feedback on resource usage, material requirements, and production stages.
- Improved cost efficiency: Real-time tracking of materials and labor hours reduces financial waste, enabling businesses to adjust budgets swiftly.
- Faster speed to market: Centralized oversight helps shorten production cycles, bolstering delivery times for customers.
- Stronger collaboration: Shared data fosters a deeper sense of partnership among cross-functional teams, leading to proactive problem-solving.
- Better data accuracy: Automated synchronization of transactions, production details, and inventory levels curtails duplication and manual errors.
Stronger clarity around planning, scheduling, and output lays a foundation for consistent growth. Modern manufacturing ecosystems reap additional advantages when shared data streams guide pivotal decisions. Visibility across production lines and corporate operations saves time, money, and labor. A closer look at best practices ensures these benefits become a reality on a wider scale.
Best Practices for Successful ERP and MES Integration
Leaders often focus on structured methods when merging ERP and MES. Effective planning sets the stage for a reliable system rollout and reduces friction among teams. Each stage of implementation demands proper communication and meticulous execution to avoid misalignment. Adopting best practices ensures a seamless transition, minimizes disruptions, and creates lasting improvements across manufacturing operations.
Clear Scope Definition
Defining the scope clearly at the beginning prevents scope creep and operational confusion. Teams must explicitly outline what the integration aims to achieve, including detailed objectives related to cost efficiency, throughput, and data visibility. This approach helps align the technical selection of hardware and software components directly to business goals. Establishing clear milestones and checkpoints further assists in tracking progress, addressing any deviations swiftly, and ensuring the project's objectives are consistently met.
Early Stakeholder Engagement
Engaging stakeholders early in the integration process significantly improves alignment and reduces resistance. Stakeholders across departments, including production, IT, finance, and quality control, should participate in initial planning sessions to express requirements and identify potential obstacles. This inclusive strategy ensures multiple perspectives are incorporated, fostering a sense of ownership and commitment among participants. Additionally, regular stakeholder briefings throughout the project enhance transparency, facilitate feedback, and build continuous support that drives successful implementation.
Structured Data and Governance
A structured approach to data governance is essential to successful ERP and MES integration. Standardizing and cleansing data, such as part numbers, bills of material, and routing instructions, reduces inconsistencies and errors during integration. Clearly defined governance policies establish accountability, define data ownership, and set protocols for data handling and security. Implementing robust governance structures also facilitates easier compliance management, provides clarity during audits, and enables smooth scaling when extending the integrated system to new manufacturing sites or processes.
Comprehensive Training and Support
Providing thorough training and continuous support to users and administrators is crucial for successful integration. Comprehensive training programs should cover system functionalities, data entry standards, troubleshooting procedures, and best practices. Equipping employees with user-friendly documentation, online resources, and dedicated support channels ensures they can navigate the new system confidently. Consistent post-implementation support addresses issues promptly, reinforcing user adoption, maximizing system utilization, and providing long-term efficiency.
Regular Performance Reviews and Optimization
Conducting regular performance reviews after implementation helps ensure the ERP and MES integration remains effective and aligned with evolving business needs. Monitoring system performance against predefined metrics, such as data accuracy, throughput speed, and cost savings, enables continuous improvement. Periodic reviews provide insights into areas requiring optimization, ensuring the integrated systems remain agile and responsive to changing manufacturing conditions. A commitment to ongoing optimization supports lasting efficiency gains and maximizes return on investment.
Common Challenges in ERP and MES Integration
Some organizations face a range of obstacles when aligning these systems. Delays or miscommunication can derail efforts and limit return on investment. Multiple variables, including legacy technology and user skepticism, require careful attention. These difficulties often arise when planning is incomplete or insufficient resources are allocated to critical stages.
- Limited IT resources: Lack of skilled personnel or inadequate budgets can stall progress and slow the introduction of new features.
- Incompatible legacy systems: Older platforms may require specialized middleware or extensive updates to function seamlessly with modern systems.
- Resistance from employees: Longtime staff members may be hesitant to adopt new tools, underscoring the importance of training and open dialogue.
Teams that anticipate these challenges often build stronger project plans from the start. Early audits of existing infrastructure, stakeholder alignment sessions, and ongoing communication mitigate many sources of risk. Leaders who address these complexities proactively foster a more stable connection between ERP and MES. Awareness of potential pitfalls lays the groundwork for a smoother transition.
The Role of PLM in ERP and MES Integration
Product Lifecycle Management (PLM) solutions merge design, production, and after-market processes for a comprehensive view of product data. Information captured during design can guide production settings on the shop floor, ensuring consistent quality outputs. This loop of constant feedback helps leaders identify inefficiencies and prioritize improvements across production lines. Seamless interaction among ERP, PLM, and MES platforms unifies critical data streams that once existed in isolation.
Stakeholders benefit from having design data linked to real-time manufacturing metrics to reveal patterns that drive cost savings and faster releases. This synergy cuts down on rework and fosters a deeper sense of accountability across every phase of a product’s journey. Companies that integrate PLM with ERP and MES often tap into previously hidden operational capacities. A dynamic communication loop ensures that each stage remains aligned to market requirements.
Future Trends in ERP and MES Integration
Machine learning and artificial intelligence are gaining traction for predictive maintenance and process optimization. Sensor data from the shop floor can be analyzed in real time to recommend adjustments that avoid downtime or quality issues. This level of insight positions teams to respond promptly and increase production precision. Cloud-based architectures also attract interest because they simplify deployment and allow faster expansion.
Augmented reality tools show promise for advanced operator training, remote collaboration, and ongoing safety improvements. Robotics often work hand in hand with connected systems, creating consistent output and reducing labor-intensive tasks. Upcoming developments suggest deeper integration of supply chain systems to create a more holistic view of procurement and inventory. Organizations that stay agile will likely discover new ways to refine their technology stack and stay ahead of shifting requirements.
Manufacturers worldwide are adopting cloud-based solutions to achieve efficiency, precision, and scalability. At 42Q, we combine decades of manufacturing expertise with cutting-edge technology to deliver connected manufacturing. Our flexible, cloud-native MES platform enhances visibility, streamlines operations, and accelerates digital factory advancement. Discover how our solutions can empower your factory to reach its full potential.
Key Takeaways
- A unified ERP and MES platform allows real-time data exchange that drives process consistency and measurable gains.
- A structured plan for scope, governance, and stakeholder collaboration helps prevent confusion and costly delays.
- Thorough user training and regular system audits address potential setbacks and strengthen adoption.
- PLM solutions connect design and manufacturing data, opening fresh insights for product improvements and faster releases.
- Cloud-based architectures, AI, and robotics continue to shape the future of integrated manufacturing systems.
FAQs
ERP and MES integration links backend business processes with shop floor production data. This connection ensures consistent information flow and allows you to fine-tune resource planning, scheduling, and quality management. Manufacturing outcomes often improve thanks to real-time insights and precise data.
Managers gain immediate updates on labor hours, material usage, and production status. Accurate information leads to faster adjustments, reducing waste and operational expenses. Greater clarity over expenditures also helps in budgeting and resource allocation.
The main difference between these three platforms lies in their core responsibilities and data focus. ERP manages corporate and financial processes, MES focuses on real-time production activities, and PLM centralizes product design and lifecycle information. When used in combination, they offer a more comprehensive framework for efficient output and improved scalability.
Many legacy platforms can merge with modern solutions through middleware or targeted software upgrades. This approach addresses compatibility concerns and aligns older equipment with new data protocols. The result is a seamless flow of information without the need for a total system overhaul.
Clear objectives and early stakeholder involvement often produce better alignment and acceptance. Comprehensive training and open communication lower resistance and reinforce consistent data standards. Ongoing reviews of performance metrics help sustain progress and refine best practices.
Comparing Cloud MES Platforms
vs. On-Premise Systems
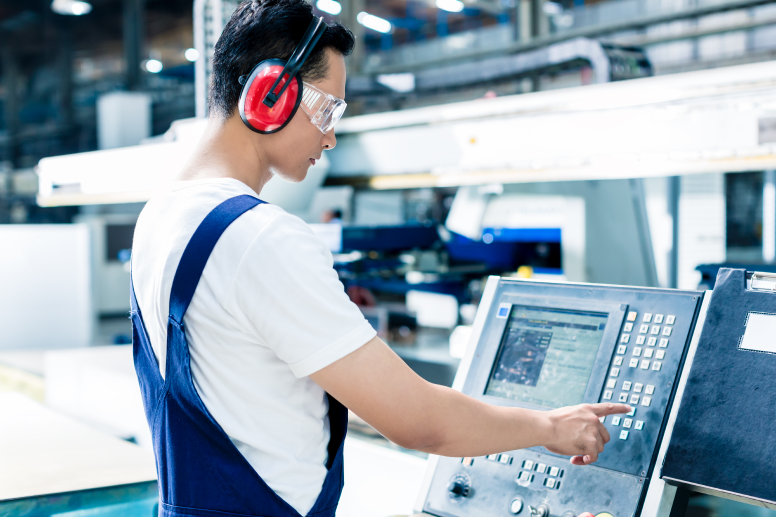
Comparing Cloud-Based MES Platforms vs. On-Premise Systems
Cloud-based MES solutions help manufacturers unlock growth with faster implementation and real-time production oversight. Traditional on-premise systems can still serve specific purposes, but modern facilities often seek flexible, scalable, and cost-effective platforms. Many plants hesitate to migrate because of cybersecurity or data ownership concerns and integration complexity. Despite these considerations, cloud-based deployments frequently deliver significant benefits that align with speed to market and business expansion.
Modern production lines move at a serious pace, and any approach that fosters improved visibility can make a measurable difference. Cloud-based MES platforms deliver immediate data insights that support quick adjustments and streamlined collaboration. This model often lowers the barrier to entry for organizations wanting advanced functionality without heavy capital expenses. Decision-makers who review these solutions will find a strong case for maximizing returns through seamless scalability and prompt ROI.
What Is A Cloud-Based MES?
Cloud-based manufacturing execution system solutions run on remote servers hosted by third-party providers. They give production sites a centralized interface accessible through the internet, which reduces on-site hardware and IT overhead. Many teams refer to this as MES in the cloud because core functionalities, including data storage and analytics, are delivered through a web-based interface. This structure aims to accelerate production oversight, maintain consistent performance, and minimize up-front capital investments.
Cloud MES platforms rely on robust network connectivity, often resulting in quicker updates and minimal system maintenance. Security is typically handled through provider protocols and encryption measures, giving stakeholders peace of mind. These solutions align well with speed-to-market priorities because they can be rolled out swiftly with minimal downtime. They also scale effectively, allowing businesses to handle production growth without significant infrastructure changes.
What Is an On-Premise MES?
On-premise MES software is installed within a manufacturing facility’s local servers, placing responsibility for hardware, security, and maintenance in the hands of internal teams. This method can grant organizations direct control over their data and system settings. Many factories appreciate the sense of ownership gained from hosting these systems on-site, especially in sectors with strict compliance requirements. Some leaders gravitate toward on-premise setups for customization, though these implementations typically involve higher initial costs.
Regular updates often require specialized IT staff or external support, which can stretch implementation timelines. Maintenance windows may disrupt production if hardware or software changes must be made on-site. Scalability is also a concern, as expansions frequently require additional servers and more robust networking capabilities. Despite the control an on-premise MES offers, these constraints can result in slower deployments and reduced flexibility for quick optimization.
How Do Cloud MES Platforms Compare to On-Premise Systems?
The main difference between a cloud MES and an on-premise MES solution lies in where the system is hosted and how it is maintained. Cloud-based models depend on external data centers and remove the need for large on-site hardware investments. On-premise systems, in contrast, reside within the internal network and require dedicated servers plus ongoing maintenance from the organization’s IT department. Both approaches can deliver strong production control, but they differ markedly in cost, flexibility, and ease of deployment.
Factors | Cloud-Based MES | On-Premise MES |
Deployment Time | Shorter, minimal hardware required | Longer, requires dedicated infrastructure |
Scalability | High, pay-as-you-grow model | Limited, hardware upgrades needed |
Maintenance | Handled by vendor, automatic updates | Internal staff or external contractors needed |
Data Access | Remote accessibility from any device | Local network access or VPN |
Cost Structure | Subscription-based, fewer upfront expenses | Higher initial costs, ongoing hardware investments |
Security | Managed by provider, advanced encryption | Internal responsibility, local compliance focus |
Many manufacturers appreciate the convenience of remote system oversight provided by cloud-based MES, especially when tackling new production runs. On-premise setups remain relevant for certain compliance-focused sectors that prefer localized control. A thorough review of operational requirements and budgets often highlights which model offers the best strategic advantage. Organizations that plan for expansion typically lean toward cloud configurations, while those with fixed processes may stay with on-premise deployments.
Benefits of Cloud-Based MES For Manufacturers
Cloud-based MES platforms introduce valuable features that can support faster time to market. Remote accessibility, automatic software updates, and subscription-based pricing lower the barriers that come with digital factory upgrades. Manufacturers gain the capacity to scale production quickly, without making large investments in new hardware. The following points detail some notable advantages that resonate with organizations aiming to maximize returns and reduce unnecessary expenses.
- Reduced Upfront Costs: The subscription-based model avoids hefty investments in servers and hardware.
- Faster Deployment: Remote provisioning accelerates the go-live process and saves valuable engineering time.
- Flexible Scalability: Additional capacity can be added on request, allowing factories to adjust volumes based on need.
- Automatic Updates: The provider manages software enhancements, eliminating manual patches and reducing downtime.
- Enhanced Collaboration: Real-time data access supports cross-site and cross-department coordination for improved efficiency.
- Global Visibility: Multiple locations can link to a single database, offering consolidated reporting and streamlined oversight.
These advantages reflect a strategy geared toward long-term growth. Many manufacturers also value the cost-effective nature of cloud-based MES for pilot programs and expansions. A flexible deployment empowers organizations to pivot quickly when product lines shift or production volumes spike. With these points in mind, businesses often see cloud-based solutions as a modern way to address new operational requirements.
Challenges of On-Premise MES
An on-premise MES strategy involves certain constraints that may affect speed to market. The need for dedicated servers, ongoing maintenance, and specialized staff can cause slower adjustments. Upgrades often mean potential production disruptions or extended lead times for new hardware installations. Some manufacturers consider these hurdles significant, particularly when calculating total cost of ownership.
- High Capital Expenses: Building and maintaining on-site server infrastructure can strain budgets.
- Limited Remote Access: Many on-premise deployments restrict data insights to the local network, making off-site oversight more difficult.
- Longer Implementation Timelines: Hardware setup and testing extend go-live schedules and delay return on investment.
- Complex Upgrades: Software patches require manual intervention, often prompting system downtime and added labor expenses.
- Scalability Challenges: Adding new production lines may require extra servers and configuration, increasing operational complexity.
- Security and Compliance Burdens: Companies must independently manage data protection measures and audits.
These factors do not always disqualify on-premise approaches, but they do present hurdles that call for advanced planning. Organizations that rely on highly customized systems might decide the added control is worth the investment. That path aligns with certain regulated industries where local data storage is preferred. Still, many manufacturers eventually explore cloud-based MES once they weigh the pros and cons.
Key Features of Cloud-Based MES Platforms
Real-Time Data Collection
Many cloud-based manufacturing execution systems provide immediate production feedback, delivering insights on throughput, downtime, and equipment status. This capability helps supervisors spot bottlenecks and correct issues without delay. A transparent view of cycle times and yield rates can reveal opportunities for cost-saving measures. Consistent data flow also supports audits and compliance initiatives, reinforcing accountability throughout the facility.
Advanced Quality Control
Robust quality modules are often built into cloud MES software, providing standardized checks at each production stage. Electronic work instructions can reduce manual errors while ensuring adherence to operational guidelines. Additional data points, such as traceability details and defect reports, simplify root cause analysis. Manufacturers gain the freedom to refine processes without rewriting code or reconfiguring hardware.
Seamless ERP Integration
Cloud-based platforms typically offer APIs and connectors that synchronize data with enterprise resource planning tools. This configuration delivers a unified source of truth, covering materials, orders, and production status under one umbrella. The shared data model diminishes duplication while allowing faster management decisions across multiple departments. Many organizations see major gains in throughput, scheduling efficiency, and cross-functional collaboration.
Implementing A Cloud-Based MES
Planning and Stakeholder Alignment
Successful adoption of a cloud-based MES begins with a clear roadmap that outlines business objectives. Early involvement of department heads helps set realistic timelines and budgets. Many organizations also conduct feasibility assessments to confirm that legacy systems can integrate properly with cloud-based solutions. Careful communication supports wide acceptance across the enterprise, easing the shift from older processes.
Pilot Program Execution
A limited-scope rollout often validates assumptions around data accuracy and performance metrics. Teams can test the user interface, gather operator feedback, and refine workflows before full-scale deployment. This step reduces risks by catching technical issues early in the process. A well-orchestrated pilot clarifies the training requirements needed for broader implementation.
Continuous Improvement
Cloud MES platforms allow for real-time updates, so teams can quickly tweak production settings in response to user feedback. Ongoing measurement of key performance indicators uncovers new cost-saving or quality-enhancing tactics. Frequent reviews ensure the system remains aligned with changing product lines and market conditions. Organizations that commit to iterative improvements often achieve measurable gains in output and ROI.
Applications of Cloud-Based MES In Manufacturing
Many industries use a cloud-based manufacturing execution system to meet distinct production objectives. Medical device firms track serialized components for traceability and compliance. Automotive plants organize complex assemblies across multiple stations, while electronics makers manage shorter product lifecycles. The following list outlines how a cloud MES platform supports different manufacturing processes.
- Medical Device Production: Real-time tracking of lot numbers and automatic recordkeeping to comply with stringent regulations.
- Automotive Assembly: Integrated work instructions that coordinate multiple sub-assemblies and help reduce rework rates.
- Aerospace and Defense: Comprehensive traceability for every component, ensuring consistent quality across extended project timelines.
- Semiconductor Manufacturing: Detailed monitoring of cleanroom parameters and process steps, maximizing yield and reducing contamination risks.
- Consumer Electronics: Centralized monitoring that keeps pace with frequent product updates and short production runs.
Each scenario highlights the flexibility and data-rich capabilities that set cloud-based MES solutions apart. Similar benefits apply across other segments like mining equipment, plastic fabrication, and industrial manufacturing. The ability to centralize information, drive accountability, and respond to production shifts forms the core value of this model. Manufacturers frequently adopt cloud systems to unify scattered processes and expose hidden efficiencies.
Predictions for The Future of MES
Manufacturing technology continues to advance, with many companies prioritizing cloud-based deployments to stay agile. Data analytics, AI, and machine learning integrations will likely become more accessible, expanding the capabilities of a standard MES platform. Real-time insights may guide production volume adjustments and resource allocation faster than traditional methods. Such progress suggests that cloud-based manufacturing execution systems could dominate future deployments.
On-premise solutions might still hold niche roles where security requirements remain especially strict. However, the rising appeal of subscription-based models indicates that many organizations will gravitate toward scalable, vendor-managed systems. Additional connectivity with Industrial Internet of Things (IIoT) devices will create more synergies in the production chain. These trends point toward a more data-driven, linked manufacturing framework grounded in cloud-based infrastructure.
Cloud-based MES solutions and on-premise options each serve critical purposes in modern manufacturing. Organizations often weigh factors such as cost, deployment speed, and regulatory obligations before choosing a system. Cloud deployments typically align with businesses that value short implementation timelines and scalable features. On-premise strategies remain prevalent among those seeking direct control and extensive customization.
A balanced approach involves assessing immediate requirements while forecasting potential expansions. Many manufacturers find that a hybrid model, where certain sensitive processes remain on-premise while other functions shift to the cloud, offers a workable compromise. Yet the momentum for cloud-based manufacturing execution systems shows no sign of slowing, given the growing push for operational efficiency and integrated analytics. Forward-looking leaders often prioritize flexible technology that can adapt to changing market conditions.
Manufacturers worldwide are embracing cloud-based solutions to achieve efficiency, precision, and scalability. At 42Q, decades of manufacturing expertise blend with advanced technology to deliver connected production. Our flexible, cloud-native MES platform enhances visibility, streamlines operations, and accelerates digital enhancements. Discover how these solutions can empower your factory to reach its full potential.
Key Takeaways
- Cloud-based MES platforms support rapid deployments and continuous scalability, cutting down hardware costs.
- On-premise MES solutions offer direct control and customization but tend to involve higher upfront investments.
- Remote accessibility, automatic updates, and subscription pricing reinforce the appeal of a cloud-based manufacturing execution system.
- Planning, pilot testing, and ongoing improvements form the backbone of a successful implementation strategy.
- Growing manufacturing needs often favor the cloud, though on-premise systems still play a role in certain regulated scenarios.
FAQs
Scalability supports sudden shifts in production voluMES and new product lines without overhauling existing IT infrastructure. Manufacturers gain the freedom to add extra capacity on demand, helping them control costs and maintain a steady pace of operations.
Yes, many smaller facilities adopt cloud-based MES due to minimal upfront expenses and reduced hardware requirements. The subscription model can accommodate a range of production outputs, making it a practical fit for growing organizations.
Cloud MES platforms usually employ advanced encryption and robust authentication protocols managed by the vendor. On-premise systems require in-house oversight of cybersecurity measures, which can be more resource-intensive but offers direct control.
Some cloud MES software solutions allow flexible configurations, though extreme customizations may favor on-premise deployments. Reviewing specific needs and working with the vendor to tailor modules helps clarify whether the cloud can support complex requirements.
Many manufacturers choose a pilot phase to validate workflows, gather user feedback, and adjust features. This controlled rollout reduces risks and helps confirm the solution meets operational goals before a broader launch.
Why Agile Manufacturing Starts with a Composable, AI-Ready MES
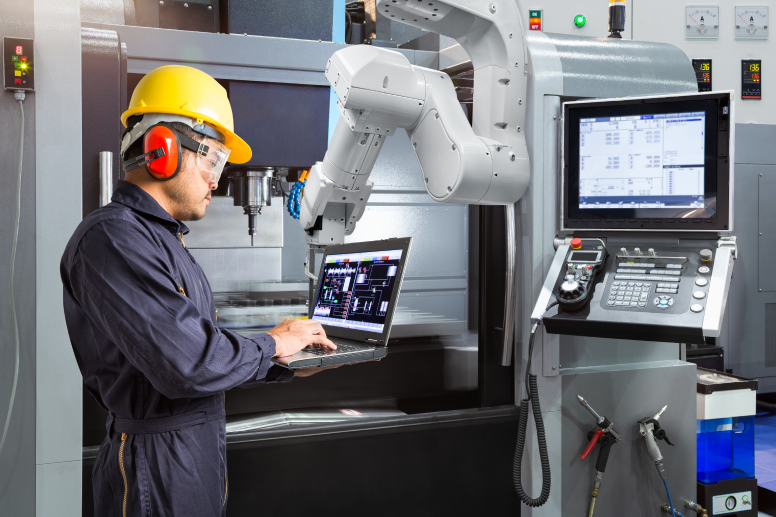
Why Agile Manufacturing Starts with a Composable, AI-Ready MES
Rigid, monolithic manufacturing systems can no longer keep up with modern demands.
To remain competitive, manufacturers must pivot to a composable, cloud-native MES architecture infused with artificial intelligence. This combination enables the agility, efficiency, and scalability that legacy systems lack. Forward-thinking manufacturers realize that a modular, AI-powered MES is not just an IT upgrade – it’s a strategic necessity for driving down costs, accelerating time to market, improving quality, and building a resilient operation.
Composability in manufacturing, which signifies building systems from independent, interchangeable components, is central to this necessity. Instead of a single, rigid system, a composable Manufacturing Execution System (MES) utilizes distinct modules that can be flexibly added, removed, or updated without affecting the entire operation. This approach helps manufacturers adapt to evolving demands, facilitates the integration of new technologies, and optimizes processes with enhanced flexibility and precision.
Traditional MES Hinders Manufacturing Agility
Traditional manufacturing execution systems (MES) were not built for change. Many factories still rely on monolithic, on-premises MES that are deeply customized and rigid. This inflexibility directly undercuts a manufacturer's ability to adapt quickly. Common issues with traditional MES include:
- Rigid architecture slows adaptation: Hard-coded workflows require lengthy reprogramming to handle process changes, delaying time to market.
- Siloed systems and data: Legacy MES often struggles to integrate with modern enterprise systems or IIoT devices, resulting in fragmented data, manual workarounds, and poor real-time visibility.
- Costly customizations and upgrades: Heavy customization makes upgrades cumbersome and expensive, locking plants into outdated software and raising maintenance costs.
- Limited scalability: Monolithic solutions cannot easily scale to new facilities or higher volumes without major effort. This hinders growth and the agility to ramp up output when demand spikes.
- Inflexible processes impact quality: When quality issues or new regulations emerge, traditional MES cannot adjust quickly. This results in inconsistent quality or compliance gaps.
These constraints translate to lost opportunities and higher operating costs. In a fast-moving market, a static MES means slower responses to customer demands, longer production lead times, and an inability to continuously improve operations. Manufacturing leaders recognize that clinging to these legacy systems is untenable if they want to compete on speed, efficiency and innovation.
Composable MES: A Modular Approach to Future-Ready Manufacturing
To achieve agility, manufacturers are shifting from rigid systems to composable MES architectures. A composable MES is built from a set of interoperable, plug-and-play modules rather than one giant application. Each module can operate independently yet integrate through open APIs and a unified data platform. This modular, cloud-native approach offers the flexibility to support a future-ready operation.
Gartner predicts that by 2027, 80% of manufacturing operations management solutions will be cloud-native and edge-driven. Unlike traditional MES, a composable MES can be reconfigured on demand. Need to add a new process or data source? Easier to deploy another module or service without overhauling the entire system. If a capability needs an upgrade, it can be improved in isolation and rolled out, reducing disruption to other functions. The result is a system evolving with the business.
Crucially, a modular MES can accelerate speed to market. Gartner reports that organizations embracing composability delivered new features 80% faster than competitors, enabling them to respond more swiftly to disruptions or customer demands by deploying new capabilities as needed. This modular model is also cost-effective; after the initial investment it reduces the cost of future changes and expansions, lowering total cost of ownership.
It also enhances traceability and quality. All modules share data to a common backbone, contributing to end-to-end visibility of production. This makes it easier to trace materials, processes, and results across different parts of the operation. If a quality issue arises, manufacturers can help pinpoint the root cause faster across connected modules.
Integrating AI with Composable MES Enhances Operational Efficiency
Making MES modular is only part of the transformation. The next level of efficiency comes from integrating artificial intelligence into these composable systems. Nearly 93% of industrial manufacturers already use AI in some form within their operations – from machine vision inspection to predictive analytics – underscoring how critical AI has become for productivity. A cloud-based, composable MES offers an ideal foundation to embed AI at key points in the workflow. By doing so, manufacturers can convert the massive streams of shop-floor data into actionable insights and autonomous decisions.
In a modular architecture, AI-driven tools can plug in more smoothly as another set of services. Below are several ways that integrating AI with a composable MES drives greater operational efficiency:
Predictive Maintenance Minimizes Downtime
Machine learning algorithms in an AI-enhanced MES analyze equipment sensor data and production trends to predict machine failures before they happen. Instead of reacting to breakdowns, maintenance is scheduled proactively when AI signals an issue. This reduces unplanned downtime, extends equipment life, and increases asset utilization while lowering maintenance costs. Ultimately, this leads to more reliable operations and a better bottom line.
Automated Quality Control and Traceability
Integrated into a composable MES, AI-powered vision systems inspect products in real time, catching defects that traditional methods might miss. They can flag anomalies on the line and trigger immediate corrective actions. All events are recorded, giving granular traceability to pinpoint where any fault occurred. This enables faster root-cause analysis and supports continuous improvement. The result is a higher first-pass yield and helps achieve compliance with strict quality standards.
Intelligent Scheduling and Resource Optimization
Advanced algorithms can rapidly recalibrate production schedules in response to real-time conditions – for example, a machine outage or a rush order. Re-planning production might take managers hours; an AI-driven scheduling engine can do it in seconds, optimizing throughput and minimizing idle time. This gives manufacturers greater agility, enabling shorter lead times and faster order fulfillment. Intelligent resource optimization also cuts waste, lowering the cost per unit with automations that can cut costs by 30%.
Adopting Composable MES Positions Manufacturers for Sustained Success
Manufacturers face unrelenting pressure: customers demand faster delivery and high quality, and disruptions can strike at any time. A modular, AI-ready MES can help provide the agility to pivot quickly – whether reconfiguring for a new product or scaling up to meet a surge in demand. It also future-proofs operations. New technologies can be added as modules without overhauling the system, and cloud delivery helps ensure updates roll smoothly. This approach is rapidly becoming the norm, and early adopters gain an edge. Key benefits include lower costs from reduced downtime and scrap, faster time to market, easier scalability, and improved quality through better traceability. Manufacturers that embrace this shift can better weather disruptions and seize new opportunities, while others lag behind. The path forward is clear: build IT around modularity, openness and intelligence. A composable, AI-driven MES is the blueprint for manufacturing excellence, enabling continuous adaptation and innovation.
42Q supports the transition to a modular, plug-and-play, AI-ready MES as the blueprint for modern manufacturing excellence. Leveraging our cloud-native MES platform with interoperable modules empowers manufacturers to modernize at their own pace while integrating advanced AI-driven insights. The result is a scalable, agile operation that drives continuous improvement in quality and efficiency – exactly what companies need.
Key Takeaways
- Modular MES frameworks allow plants to adapt quickly to new requirements.
- Cloud deployment shortens implementation and helps cut operational expenses.
- Unified data models streamline analytics and support AI-backed insights.
- Digital traceability reduces compliance overhead and prevents quality issues.
- Composable architecture fosters cost-effective scaling for sustained production gains.
FAQs
Composable manufacturing involves using modular, interoperable building blocks that work seamlessly within production processes. A composable MES breaks down functionality into flexible components, allowing you to upgrade or switch out features without overhauling the entire system.
A traditional MES often comes with rigid architectures and lengthy implementation cycles. A composable approach offers smaller, adaptable modules that deploy quickly, creating a path to faster returns and easier updates.
Cloud-based architectures simplify AI integration by offering open interfaces and standardized protocols. This structure helps you incorporate predictive analytics, machine learning, or robotics modules without large-scale redevelopment.
Yes, modular elements provide granular traceability and version control that align with regulatory mandates. You can quickly adjust or add new compliance features to meet emerging standards.
A subscription-based model can reduce upfront hardware costs and spread expenses predictably over time. The option to add or remove modules ensures you only pay for what your operation needs.
6 Benefits of Composability in Manufacturing
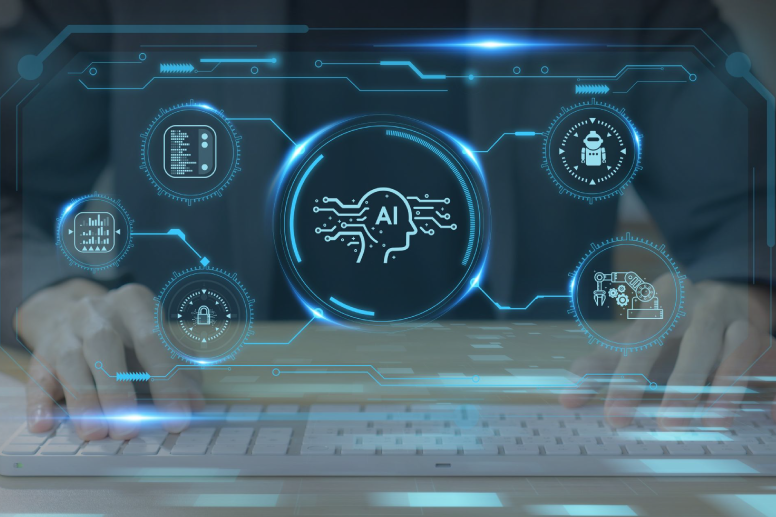
6 Benefits of Composability in Manufacturing
Composability in manufacturing refers to the ability to combine modular components in a flexible and efficient way to meet specific production needs. It allows manufacturers to break down complex systems into simpler, easily manageable pieces that can be reconfigured, upgraded, or scaled as needed. This approach leads to increased efficiency, faster adaptation to changes, and a significant reduction in costs. Embracing composability is essential in today’s highly competitive manufacturing environment, where businesses must respond quickly to changing market demands and technological advancements. By integrating composability into manufacturing processes, companies can unlock new opportunities for growth, innovation, and optimization.
What is Composability in Manufacturing?
Composability in manufacturing involves assembling different modular components within production processes to create flexible, adaptable, and efficient systems. Each component can function independently or interconnect with others, making it possible to add, remove, or reconfigure specific modules with minimal disruption. This approach promotes better responsiveness when demands shift, technologies evolve, or production requirements grow more complex. Manufacturers benefit from streamlined workflows, easier scalability, and the opportunity to adopt cutting-edge solutions without overhauling their entire operation.
Composability is rooted in the concept of designing processes to be change-ready. Modular design allows manufacturers to update individual elements without impacting the overall production pipeline, saving both time and resources. Businesses can replace legacy components or introduce novel solutions whenever the need arises, which accelerates innovation and fosters continuous improvement. This is especially important in a sector where new methods, materials, and regulations often emerge, requiring agile responses and robust operational structures that protect profitability and product quality.
MES and Composability
Manufacturing Execution Systems (MES) play a crucial role in enabling composability in modern manufacturing environments. These systems act as the backbone of a connected, flexible, and scalable factory. By incorporating modular components into MES platforms, manufacturers can achieve greater flexibility in adapting to specific production needs. MES solutions that support composability allow for seamless integration with various tools, equipment, and processes across the factory floor. This means that manufacturers can implement changes quickly, ensure optimal resource utilization, and drive innovation in production workflows, all while reducing operational complexities. With the right MES in place, the benefits of composability are more achievable and impactful than ever before.
6 Benefits of Composability in Manufacturing
The advantages of composability in manufacturing are numerous. Below are six key benefits that illustrate how adopting composable systems can enhance operational efficiency and drive success.
1. Enhanced Agility
Manufacturers today face constant pressure to adapt to shifting market conditions, supply chain disruptions, and customer demands. One of the most significant benefits of composability is its ability to enhance agility in production processes. With modular systems, manufacturers can quickly adjust production lines, replace outdated components, or integrate new technologies without disrupting the entire workflow. This flexibility ensures faster response times, improved throughput, and better alignment with market trends. The ability to pivot quickly offers manufacturers a competitive advantage, allowing them to stay ahead in the industry.
2. Improved Scalability
As businesses grow, their operational requirements change. Composability allows manufacturers to scale production capabilities up or down as needed without significant investments in new infrastructure. Modular systems enable businesses to add or remove components to match the level of demand, ensuring resources are allocated effectively. Whether expanding operations to new facilities or adapting to seasonal fluctuations in demand, composability provides the flexibility to adjust production capacity quickly and cost-effectively. This scalability is essential for long-term growth and ensures that businesses can meet market demands without incurring excessive costs or inefficiencies.
3. Cost Efficiency
Cost control is a critical concern for any manufacturing operation. Composability helps reduce costs by allowing manufacturers to optimize their resource usage and avoid unnecessary expenses. Modular components can be replaced or upgraded individually, eliminating the need for large-scale overhauls or expensive custom-built solutions. This approach also reduces downtime, as manufacturers can swap out faulty components or implement improvements without shutting down entire systems. Additionally, composable systems promote better inventory management, as manufacturers can adjust their production to match actual demand, avoiding the costs associated with overproduction or stockpiling. These cost-saving benefits significantly improve the bottom line.
4. Better Resource Utilization
Effective resource utilization is essential for maximizing the efficiency of manufacturing processes. Composability enables manufacturers to make the most of their existing resources by tailoring production processes to specific needs. With modular systems, businesses can allocate resources more effectively, ensuring that machinery, labor, and materials are used in the most efficient way possible. This reduces waste and ensures that production lines are running at optimal capacity. Furthermore, better resource utilization can lead to fewer delays, higher product quality, and reduced energy consumption, all of which contribute to improved overall performance.
5. Increased Innovation
In today’s competitive market, innovation is key to staying relevant and achieving long-term success. Composability fosters innovation by allowing manufacturers to experiment with new technologies and processes without risking major disruptions to existing systems. Because modular components can be swapped in and out easily, manufacturers can pilot new ideas, test improvements, and implement innovative solutions with minimal risk. This adaptability encourages creativity within the production environment, leading to faster implementation of new features, enhanced product designs, and the ability to respond to consumer needs more effectively. Innovation is made more accessible when businesses can integrate new technologies into their workflows seamlessly.
6. Seamless Integration
A primary benefit of composability is its ability to facilitate seamless integration between different tools, systems, and technologies within the manufacturing environment. By adopting modular systems, manufacturers can integrate new software applications, sensors, or machinery without disrupting existing operations. This integration reduces the complexity of managing diverse technologies and ensures that all components work together efficiently. With the right composability framework in place, manufacturers can integrate their operations with other systems, such as Enterprise Resource Planning (ERP) or supply chain management tools, resulting in smoother workflows and improved data sharing across departments. Seamless integration ultimately leads to enhanced collaboration and faster decision-making.
Examples of Composability in Manufacturing
Examples of composability highlight how modular systems can make manufacturing processes more adaptable, scalable, and cost-effective. These examples often showcase how everyday production tasks benefit from plug-and-play components that ensure minimal downtime. Organizations use composable frameworks to simplify tasks like assembly line reconfigurations, product customization, and equipment updates, without the need for full-scale replacements. This flexibility is essential for aligning production capabilities with new opportunities, emerging technologies, and business objectives.
- Modular production lines: Modular systems allow manufacturers to set up production lines that can be adjusted to different product types, volumes, or configurations without requiring major reengineering.
- Flexible automation: Robotic systems and automated equipment that can be easily reprogrammed or replaced based on changing production needs.
- Cloud-based MES solutions: Modular MES platforms that can integrate with a variety of production tools and systems, enhancing visibility and flexibility.
- Customizable assembly workflows: Workflow automation that can be reconfigured to suit varying production requirements, improving both efficiency and throughput.
- Digital twins: Virtual replicas of physical assets that allow manufacturers to simulate and optimize production processes, helping identify potential improvements.
These examples demonstrate that composability is more than just a buzzword; it is a strategic method for improving efficiency and responsiveness. Each composable element supports easier maintenance, faster upgrades, and better alignment between diverse production requirements. This approach empowers decision-makers to refine their operations based on accurate data insights, while limiting waste and downtime. By applying these examples, organizations can refine their existing processes, stay ahead of market shifts, and maintain stable growth in any manufacturing setting.
Common Challenges Implementing Composability in Manufacturing
Adopting composability in manufacturing offers many rewards, but there are hurdles to address before those rewards become reality. Leaders may encounter issues integrating modular components with legacy systems or finding skilled personnel who can support advanced automation. Organizational resistance can also slow the transition if teams are hesitant to shift away from traditional production approaches. Understanding these potential obstacles can help businesses develop practical strategies to successfully integrate composable designs.
- Integration complexity: Connecting disparate systems and technologies can be difficult, particularly if legacy systems are involved.
- Training requirements: Employees may need specialized training to adapt to new modular systems, which could lead to short-term disruptions.
- Cost of initial setup: While composable systems offer long-term savings, the upfront investment in modular components and software can be significant.
- Resistance to change: Employees or stakeholders who are accustomed to traditional manufacturing processes may resist transitioning to more flexible, modular systems.
- Data management: Managing and integrating the vast amounts of data generated by composable systems can be overwhelming without the right infrastructure in place.
Awareness of these challenges is the first step toward creating a roadmap for smoother composability adoption. Clear communication, robust training programs, and targeted technology investments can mitigate most of the difficulties that appear when introducing modular methods. Collaboration across departments ensures that each group understands the value of composability, easing common points of resistance. As organizations address these implementation barriers, they become better positioned to maximize long-term gains in efficiency, innovation, and agility.
Future Trends in Composability
Looking ahead, composability is expected to continue shaping the future of manufacturing. The ongoing advancements in IoT, AI, and cloud computing will only further enhance the flexibility and scalability of composable systems. With the integration of smart devices and sensors, manufacturers will have greater visibility and control over their production processes, enabling more precise adjustments and improvements. Additionally, the rise of Industry 4.0 and smart manufacturing technologies will create new opportunities for composability to thrive, making manufacturing systems more intelligent, automated, and connected than ever before.
Manufacturers worldwide are embracing cloud-based solutions to achieve efficiency, precision, and scalability. At 42Q, we combine decades of manufacturing expertise with cutting-edge technology to deliver smart connected manufacturing. Our flexible, cloud-native MES platform enhances visibility, streamlines operations, and accelerates digital transformation. Discover how our solutions can empower your factory to achieve its full potential.
Key Takeaways
- Composability allows manufacturers to adapt quickly to market changes and technological advancements, enhancing agility.
- Modular systems provide scalability, allowing manufacturers to adjust production capacity without major infrastructure changes.
- Composability leads to cost savings by reducing downtime and allowing for more efficient resource utilization.
- Modular systems enable better resource management, reducing waste and optimizing production workflows.
- Implementing composability promotes innovation by making it easier to integrate new technologies and experiment with improvements.
FAQs
Composability in manufacturing refers to the ability to integrate modular components into production systems, allowing for flexibility, scalability, and customization of workflows. This approach helps manufacturers adapt to changing demands and implement new technologies quickly.
Composability helps manufacturers reduce costs by enabling the use of modular components that can be upgraded or replaced without the need for major system overhauls. This results in savings from reduced downtime, optimized resource allocation, and the avoidance of large-scale investments.
MES plays a vital role in composability by providing a cloud-based platform that enables seamless integration of various systems, equipment, and workflows. MES helps manufacturers manage production in real time, ensuring greater efficiency and flexibility.
Composability fosters innovation by providing manufacturers with the ability to experiment with new technologies, products, and processes without disrupting existing systems. This makes it easier to implement new ideas and quickly adapt to market changes.
The challenges of implementing composability include integration complexities, initial setup costs, employee training, and potential resistance to change. However, the long-term benefits outweigh these challenges for manufacturers willing to adapt.
5 Applications of MES in Industrial Automation
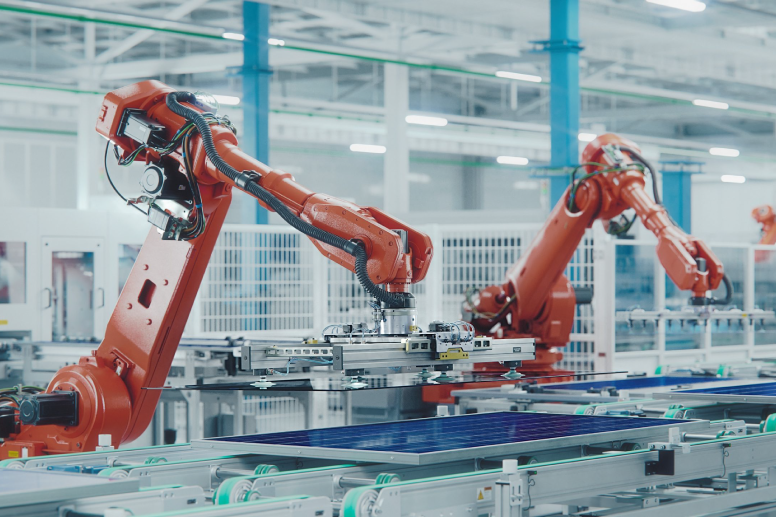
5 Applications of MES in Industrial Automation
Manufacturing Execution Systems (MES) have become a significant technology for bridging operational data with production goals. Many factories rely on real-time information to address production bottlenecks before they result in costly setbacks. Data synchronization across machinery, workers, and supply chains has proven vital for improving output consistency. Industry leaders consider MES an essential part of modern manufacturing strategies due to the immediate and measurable advantages it offers.
What is MES in Industrial Automation?
Manufacturing Execution Systems (MES) are specialized software platforms that track and manage production activities across industrial facilities. They gather real-time data from machines, workstations, and personnel to offer accurate process insights. This approach ensures that tasks run smoothly and that performance meets defined targets. An estimated 74% of manufacturers plan to implement MES or upgrade their existing solutions soon, reflecting the growing importance of this technology.
These systems play a pivotal role in industrial automation by coordinating data flows between the shop floor and higher-level business systems. This coordination supports improved scheduling, resource allocation, and process control. Manufacturers benefit from streamlined operations and real-time data insights, both of which contribute to higher output quality. MES in industrial automation applications provide a cohesive structure that ties together many facets of production, from raw materials to final products.
Importance of MES in Industrial Automation
Companies depend on real-time production insights to reduce waste and optimize efficiency. MES in industrial automation offers a direct line of sight into active workflows, allowing teams to anticipate bottlenecks before they escalate. This method keeps downtime to a minimum and enhances the overall reliability of manufacturing assets. It also helps unify data from multiple plants, leading to consistent process standards.
Another important function of MES is the ability to align production with business targets. It assists in calculating resource requirements, monitoring quality metrics, and tracking performance all in one place. This streamlined approach leads to time savings, cost reduction, and fewer errors. MES in industrial automation applications often lead to better returns on investment because they allow factories to maximize output within existing infrastructure.
5 Applications of MES in Industrial Automation
1. MES Application in Production Planning
Production schedules rely on accurate data to avoid misalignment and resource shortages. MES application in production planning helps gather relevant metrics from the shop floor to create realistic timetables. Planners gain visibility into lead times, batch sizes, and machine usage, which assists in prioritizing tasks effectively. This approach sets the stage for consistent throughput and minimizes schedule disruptions.
Better scheduling leads to faster time-to-market and higher customer satisfaction. The data analysis features of MES platforms also show exactly where to reduce inefficiencies or plan for expansions. This makes production more scalable as market demands fluctuate. Factories often see tangible returns with shorter cycles and fewer unexpected delays.
2. MES in Quality Control
Quality assurance teams benefit from an integrated system that flags deviations in real time. MES in quality control provides continuous monitoring of parameters like temperature, pressure, or component specifications. Alerts highlight variations outside the acceptable range, allowing prompt corrective actions. Workers no longer wait until the end of a batch to identify and fix issues.
Immediate error detection prevents additional defects and avoids rework costs. This improvement contributes to stronger regulatory compliance and boosts overall brand reputation. Better traceability also makes it easier to manage recalls when necessary, as each unit can be tracked through every production step. The measurable payoff is fewer quality failures and enhanced consumer trust.
3. MES for Inventory Management
Material shortages and surplus stock create unnecessary expenses. MES for inventory management offers accurate tracking of raw materials and finished goods. The software reconciles available stock with upcoming production requirements, reducing over-purchasing or last-minute scrambling. This clarity lowers warehousing costs and ensures materials are used effectively.
Digital records replace manual data entry and boost transparency across multiple sites. Operators can monitor consumption rates and plan restocking at optimal times. This method eliminates guesswork and leads to more predictable cost forecasts. The main benefit is a stable production flow that meets timelines without tying up capital in idle inventory.
4. MES in Maintenance Management
Production lines depend on consistent equipment performance, and downtime often leads to missed goals. MES in maintenance management provides a structured way to monitor machine health and schedule preventive tasks. Operators receive notifications when certain performance thresholds are exceeded or when usage hits defined limits. This precaution helps avoid major breakdowns by catching issues early.
Proactive maintenance extends the life of vital assets and promotes minimal interruptions to production. Managers can measure the effectiveness of maintenance activities with built-in analytics and adjust schedules as necessary. This means improved asset utilization and reduced overhead related to emergency repairs. Facilities often report better overall productivity and fewer unplanned shutdowns.
5. MES in Regulatory Compliance
Many sectors face specific standards for documentation, product traceability, and process safety. MES in regulatory compliance streamlines the capture and organization of necessary records. Production details are recorded automatically, reducing human error and ensuring consistent adherence to legal requirements. Audits become simpler because data remains centralized and easily accessible.
Automated logging of parameters lessens administrative burdens and cuts the time spent on manual inspections. Managers use the platform to verify that each lot meets industry guidelines and remains within approved ranges. This level of oversight is vital for consumer safety and brand credibility. The measurable outcome is reduced compliance-related costs and fewer legal complications.
Future Trends in Industrial Automation MES
The next wave of MES features is already shaping how factories measure performance and adapt to shifting demands. An industry analysis projects that the MES market could surpass $18 billion globally by 2030, highlighting the sustained momentum of these solutions. Emerging technology and advanced production strategies promise new efficiencies for many businesses. It is worthwhile to consider how upcoming developments may reshape your manufacturing roadmap.
- Greater integration with cloud services is expected to offer a faster time-to-value for new implementations. This approach reduces on-premise infrastructure and broadens accessibility.
- Augmented analytics in MES solutions will guide manufacturers to detect patterns and outliers quickly. This insight makes it easier to tweak operations on the fly.
- Collaborative robotics paired with MES have the potential to streamline workflows even further. Machine-generated data will feed into centralized dashboards for real-time visibility.
- Scalable IoT adoption could enhance data collection from sensors and devices across every step of production. The outcome is a stronger ability to forecast maintenance needs and manage workloads more precisely.
- Predictive modeling within MES may transform how factories refine production methods. Statistical projections of future performance will inform more targeted improvements.
Keeping pace with these trends can open new revenue streams and boost productivity. Adaptable MES platforms also help address uncertainties and market fluctuations more effectively. Each manufacturer must assess which features will yield the greatest impact based on business size and product complexity. The final goal is a stable, data-centric production model that supports continuous improvement.
Manufacturers worldwide are embracing cloud-based solutions to achieve efficiency, precision, and scalability. At 42Q, we combine decades of manufacturing expertise with cutting-edge technology to deliver connected manufacturing. Our flexible, cloud-native MES platform enhances visibility, streamlines operations, and accelerates digital transformation. Discover how our solutions can empower your factory to achieve its full potential.
Key Takeaways
- MES offers a unified way to manage production tasks, track resources, and monitor quality in real time.
- Integrated quality control within MES allows immediate detection of deviations, saving time and preventing rework.
- Inventory management becomes more cost-effective thanks to accurate material tracking and automated stock reconciliation.
- Maintenance notifications reduce downtime and prolong equipment lifespan by highlighting issues before failures occur.
- Regulatory compliance becomes simpler through automated record-keeping and standardized reporting workflows.
FAQs
A modern MES in industrial automation often includes real-time data capture, resource scheduling, and advanced analytics. It connects shop floor activities with management goals to maintain consistent production quality. Some solutions also integrate regulatory checks and automated reporting to keep businesses fully prepared for audits.
MES focuses on real-time production management, while other tools might handle specific tasks like equipment control. It provides a centralized view of processes, making it easier to spot bottlenecks or inefficiencies. Many manufacturers use MES alongside other systems to ensure continuous improvement across the entire facility.
MES tools offer preventive maintenance alerts based on equipment usage or performance metrics. This proactive strategy addresses potential malfunctions before they escalate. Reduced downtime leads to stable output and lower repair costs.
MES platforms automate record-keeping for processes, materials, and product history. Compliance checks become part of daily production routines, minimizing manual oversight. Many businesses see faster audits and fewer legal complications through these digital records.
MES can typically synchronize with enterprise resource planning systems through standardized APIs. This integration ensures that production data and business metrics reflect the same accurate information. Organizations often adopt such a setup to create a unified source of truth for operational decisions.
What is a Computerized Maintenance Management System (CMMS) in MES?
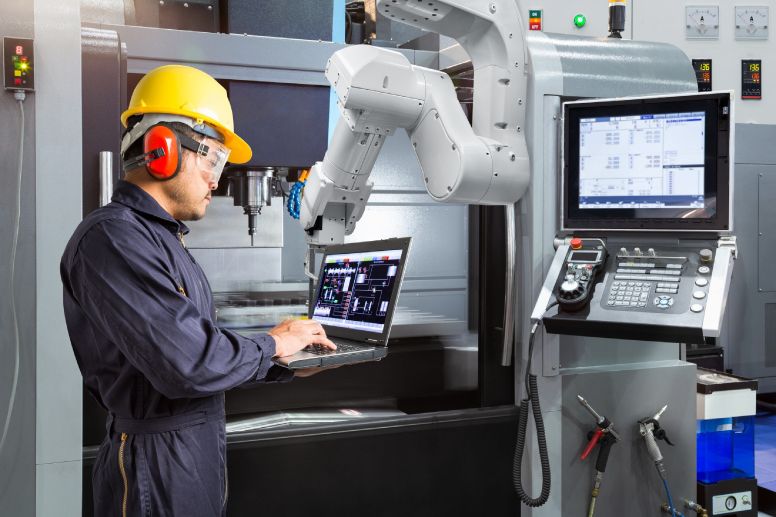
What is a Computerized Maintenance Management System (CMMS) in MES?
Equipment reliability is one of the most important factors in maintaining an efficient manufacturing operation.
A computerized maintenance management system (CMMS) ensures that maintenance activities are planned, tracked, and executed in a way that minimizes disruptions and maximizes uptime. Manufacturing facilities depend on these systems to automate work orders, manage asset lifecycles, and integrate maintenance workflows with production schedules.
The ability to monitor equipment health in real time and schedule proactive maintenance helps manufacturers prevent costly breakdowns and extend machine lifespan. A CMMS in manufacturing reduces maintenance costs, improves compliance, and enhances workforce efficiency. When integrated with a manufacturing execution system (MES), it creates a seamless connection between production and maintenance teams, ensuring that equipment remains operational without impacting output.
Key Features of CMMS Software in MES
A computerized maintenance management system (CMMS) plays a vital role in manufacturing execution systems (MES) by ensuring seamless maintenance operations, reducing equipment failures, and supporting continuous production. The right CMMS software provides essential tools to automate maintenance workflows, track asset performance, and optimize resource management. These features improve plant efficiency, extend machine lifespan, and help manufacturers meet compliance requirements.
- Automated Work Order Management: Generates, assigns, and tracks maintenance tasks, ensuring technicians receive real-time alerts for inspections and repairs. Automated workflows reduce manual scheduling errors, improve technician efficiency, and promptly address high-priority repairs.
- Preventive and Predictive Maintenance: Uses historical performance data, sensor readings, and condition-based monitoring to schedule maintenance activities before failures occur. This proactive approach minimizes costly unplanned downtime and prevents extensive damage to equipment.
- Asset Tracking and Equipment Management: Maintains a centralized database for machinery, tools, and infrastructure, allowing manufacturers to track usage, maintenance history, and depreciation. Keeping accurate records improves asset utilization and helps maintenance teams make informed repair or replacement decisions.
- Spare Parts and Inventory Control: Monitors stock levels, tracks usage patterns, and automates reordering processes to prevent supply shortages. Having the right spare parts available reduces repair wait times, ensuring minimal disruption to production.
- Failure Analysis and Root Cause Reporting: Identifies recurring issues by analyzing failure patterns and maintenance records. Data-driven insights help maintenance teams implement long-term solutions that reduce repeated breakdowns and lower repair costs.
- Compliance and Audit Support: Tracks maintenance records, inspection reports, and calibration logs to meet industry-specific regulatory requirements. Built-in compliance tools streamline audit preparation, ensuring manufacturers have accurate documentation readily available.
- Mobile Access for Maintenance Teams: Provides technicians with mobile-friendly platforms to receive work orders, log maintenance activities, and update asset information in real-time. Mobile CMMS solutions improve response times and reduce communication delays.
- IoT and Sensor-Based Monitoring: Integrates with connected devices and industrial sensors to monitor equipment performance in real-time. Automated alerts notify maintenance teams of irregularities, predictive maintenance that prevents equipment failures.
- Customizable Dashboards and Reporting: Offers data visualization tools that help plant managers analyze key performance indicators (KPIs), track maintenance efficiency, and improve resource allocation. Custom reports provide insights into work order completion rates, asset reliability, and maintenance costs.
- Integration with MES and ERP Systems: Ensures seamless data exchange between maintenance, production, and business operations. Connecting CMMS software with MES and ERP platforms allows manufacturers to synchronize maintenance activities with production schedules, improving overall workflow efficiency.
A CMMS in manufacturing provides essential tools to streamline maintenance operations, prevent equipment failures, and improve cost control. These features help manufacturers optimize asset performance, minimize production disruptions, and maintain compliance with regulatory standards.
The Role of CMMS in Manufacturing
A CMMS in manufacturing serves as the foundation for effective equipment maintenance, helping facilities minimize disruptions and optimize productivity. Production lines rely on machinery operating at peak efficiency, and any unexpected breakdown can result in costly delays. A computerized maintenance management system ensures that all maintenance activities are scheduled, tracked, and executed in a way that maximizes uptime while keeping repair costs under control.
Manufacturers use a CMMS to implement proactive maintenance strategies that reduce the likelihood of unplanned downtime. Equipment sensors and historical performance data allow teams to anticipate failures and take corrective action before they impact production. Maintenance workflows are automated to assign tasks based on priority, resource availability, and machine usage patterns. This level of coordination helps manufacturing plants operate with fewer disruptions and lower operational risks.
Compliance with industry regulations is another critical function of a CMMS in MES. Manufacturing industries such as medical devices, automotive, and aerospace require meticulous tracking of maintenance records, calibration schedules, and component replacements. A CMMS software simplifies compliance efforts by documenting all maintenance activities and ensuring audit trails remain accurate and current.
Benefits of Manufacturing CMMS
A computerized maintenance management system (CMMS) improves manufacturing efficiency by automating maintenance workflows, tracking asset performance, and reducing equipment downtime. In an industry where operational delays lead to significant costs, a well-implemented CMMS in manufacturing ensures that maintenance teams work proactively rather than reacting to unexpected failures. The following benefits help manufacturers reduce expenses, optimize resource allocation, and improve production efficiency.
- Reduced Equipment Downtime: Scheduled maintenance tasks and predictive analytics allow maintenance teams to detect potential failures before they impact production. This proactive approach ensures equipment remains operational, minimizing disruptions to manufacturing schedules and preventing revenue loss.
- Lower Maintenance and Repair Costs: Optimized maintenance schedules prevent excessive wear and tear, reducing the need for costly emergency repairs. A CMMS in MES also helps allocate maintenance resources efficiently, preventing unnecessary labor and equipment expenditures.
- Extended Asset Lifespan: Routine inspections, timely repairs, and condition-based maintenance strategies help extend the life of machinery and production equipment. A maintenance approach reduces premature replacements, protecting capital investments.
- Improved Regulatory Compliance: Manufacturing industries, including medical devices and aerospace, require strict adherence to regulatory maintenance and safety standards. CMMS software automates documentation, ensuring that maintenance records, calibration logs, and audit trails remain accurate and readily accessible.
- Increased Workforce Efficiency: Automated work orders eliminate manual scheduling errors, ensuring technicians receive precise instructions based on equipment priorities. Mobile access to maintenance records allows teams to complete tasks more efficiently and respond to urgent repairs without delays.
- Optimized Spare Parts and Inventory Management: Automated stock level tracking ensures critical spare parts remain available. A manufacturing CMMS prevents overstocking while reducing risks associated with parts shortages, ensuring that repairs are completed on time.
- Better Equipment Performance Monitoring: IoT sensors and MES data provide real-time insights into machine conditions. Maintenance teams can rely on data-driven triggers for servicing, reducing reliance on static maintenance schedules that may not align with equipment needs.
- Enhanced Data Analytics and Reporting: Custom reports and dashboards help manufacturers track maintenance costs, technician productivity, and asset reliability. Data-driven insights support better long-term maintenance planning and strategic rationale.
- More substantial Safety and Risk Management: Regular maintenance inspections reduce the likelihood of equipment malfunctions that could pose safety hazards to employees. A CMMS software ensures that machinery remains in optimal working condition, lowering the risk of workplace incidents.
- Seamless Integration with Production Workflows: A CMMS in MES connects maintenance activities with production schedules, ensuring that planned maintenance does not interfere with critical manufacturing processes. Coordinated workflows improve efficiency without sacrificing output.
A CMMS in manufacturing ensures that production facilities remain efficient, safe, and cost-effective. Manufacturers improve asset reliability by centralizing maintenance operations and automating workflows, reducing unexpected expenses and compliance risks.
Integrating CMMS with MES
A computerized maintenance management system (CMMS) becomes more effective when integrated with a manufacturing execution system (MES). This connection allows manufacturers to align maintenance activities with production schedules, reducing unplanned downtime and improving overall operational efficiency. An integrated system ensures real-time asset performance monitoring, providing maintenance teams with data-driven insights to schedule preventive maintenance without disrupting manufacturing processes.
Seamless integration between CMMS software and an MES improves communication between maintenance and production teams. Equipment health data flows directly into the CMMS, allowing maintenance teams to prioritize repairs based on asset conditions rather than relying solely on time-based schedules. This coordination reduces production stoppages and prevents unnecessary maintenance activities, optimizing machine uptime and resource allocation.
Real-Time Equipment Monitoring
Machine performance data captured by IoT sensors, programmable logic controllers (PLCs), and MES platforms feed directly into the CMMS, allowing maintenance teams to assess asset health in real-time. If a piece of equipment starts showing irregular patterns, automated alerts trigger maintenance requests before failures occur. This prevents unexpected breakdowns while reducing unnecessary preventive maintenance, ensuring resources are used efficiently.
Automated Work Order Scheduling
An integrated system generates work orders based on machine conditions, production requirements, and technician availability. Maintenance tasks are scheduled in coordination with manufacturing workflows, ensuring that planned servicing does not disrupt critical operations. This approach eliminates the inefficiencies of manual scheduling and ensures that equipment receives service at the optimal time.
Enhanced Data Accuracy and Reporting
Manual data entry often leads to inconsistencies and errors that compromise maintenance efficiency. A CMMS in MES eliminates these challenges by automatically recording maintenance logs, repair history, and asset performance data. Accurate reporting gives maintenance managers insights into failure trends, labor efficiency, and cost-saving opportunities, improving long-term maintenance planning.
Optimized Spare Parts and Inventory Control
Connecting CMMS software with an MES directly links maintenance needs and spare parts inventory. Automatic inventory tracking ensures that necessary components are available before a maintenance task begins, reducing delays caused by missing parts. This also prevents overstocking, reducing inventory holding costs while providing critical supplies are always on hand.
Better Compliance and Audit Readiness
Manufacturers in regulated industries must maintain accurate maintenance records for compliance audits. An integrated CMMS in manufacturing streamlines this process by documenting all inspections, repairs, and calibrations in a centralized system. This improves audit readiness and helps manufacturing facilities meet regulatory standards without the burden of manual documentation.
A CMMS integrated with MES provides manufacturers with a connected maintenance strategy that enhances efficiency, reduces downtime, and extends asset lifespan. The ability to track machine health, automate scheduling, and optimize inventory ensures that maintenance operations align with production goals, improving overall plant performance.
Choosing the Right CMMS Software for MES
Selecting a computerized maintenance management system that integrates effectively with an MES requires careful evaluation of key factors that impact operational efficiency, scalability, and cost-effectiveness. Manufacturing operations rely on a CMMS that automates maintenance workflows and aligns with existing production processes.
Compatibility with MES software is essential for seamless data exchange between maintenance and production teams. A system that integrates with IoT devices, machine sensors, and enterprise resource planning (ERP) platforms ensures real-time equipment monitoring and accurate maintenance tracking. Cloud-based deployment options offer flexibility by reducing on-site infrastructure costs while providing secure remote access to maintenance records.
User-friendly interfaces and mobile accessibility improve adoption rates among maintenance teams. A well-designed CMMS allows technicians to access work orders, submit reports, and update asset records from any location. Customization options further enhance usability, allowing manufacturers to tailor features such as automated scheduling, compliance tracking, and spare parts management to fit their specific needs.
Scalability is another important factor when selecting a CMMS in manufacturing. A system that supports multiple facilities, production lines, and asset categories ensures long-term usability as business operations expand. Generating detailed reports and analytics also enhances maintenance planning, helping manufacturers optimize performance and reduce operational risks.
EAM vs CMMS: Key Differences
The main difference between an enterprise asset management (EAM) system and a computerized maintenance management system (CMMS) lies in their scope and functionality. A CMMS focuses on maintenance-related tasks, while an EAM provides a broader approach to asset management, covering the entire lifecycle of equipment from procurement to disposal.
Feature | CMMS | EAM |
Primary Focus | Maintenance scheduling and tracking | Full asset lifecycle management |
Scope | Equipment maintenance and repairs | Procurement, maintenance, and asset utilization |
Integration | Works with MES and maintenance teams | Connects with ERP, MES, and financial systems |
Asset Lifecycle | Limited to the operational phase | Covers acquisition, operation, and decommissioning |
Inventory Management | Tracks spare parts for maintenance | Manages asset-related inventory and procurement |
Compliance Support | Ensures regulatory maintenance tracking | Covers audits, compliance reporting, and documentation |
A CMMS in manufacturing is primarily designed to manage maintenance operations, focusing on scheduling, work orders, and spare parts tracking. It helps manufacturers prevent downtime and maintain regulatory compliance through detailed maintenance logs and automated workflows.
An EAM system takes a more comprehensive approach, tracking assets throughout their lifecycle, from initial acquisition to retirement. This system integrates with financial and procurement modules, making it a better choice for manufacturers that require enterprise-wide asset management.
Future Trends in CMMS for Manufacturing
Advancements in computerized maintenance management system (CMMS) software continue to improve manufacturers' management of maintenance operations, reduce downtime, and optimize asset performance. As manufacturing facilities adopt more innovative technologies, CMMS in MES solutions incorporate automation, real-time analytics, and predictive capabilities to improve efficiency. The following trends are shaping the future of CMMS software in manufacturing.
- AI-Powered Predictive Maintenance: Artificial intelligence (AI) analyzes machine performance data to identify patterns that indicate potential failures. Instead of relying on fixed maintenance schedules, AI-driven insights help maintenance teams anticipate issues before they lead to breakdowns, improving equipment reliability and reducing repair costs.
- IoT-Connected Maintenance Systems: Industrial IoT (IIoT) devices collect real-time sensor data from machines, continuously monitoring temperature, vibration, and energy consumption. A CMMS in manufacturing processes this data and generates automated alerts when equipment conditions deviate from normal operating ranges, allowing maintenance teams to act before failures occur.
- Cloud-Based CMMS Deployment: Cloud-based CMMS software allows manufacturers to manage maintenance operations without requiring extensive on-site infrastructure. Cloud solutions offer better accessibility for maintenance teams, secure data storage, automatic updates, and the ability to scale across multiple facilities without expensive hardware investments.
- Augmented Reality (AR) for Maintenance Support: AR technology assists technicians by overlaying real-time visual instructions onto equipment during inspections and repairs. This helps reduce downtime, minimize human errors, and improve training for new maintenance personnel, ensuring tasks are performed correctly without delays.
- Mobile CMMS Applications for On-the-Go Maintenance: Maintenance teams benefit from mobile-friendly CMMS software that provides instant access to work orders, asset records, and real-time machine data. Mobile solutions improve response times by allowing technicians to diagnose and resolve issues without being tied to a desktop interface.
- Automated Workflows and AI Chatbots: AI-powered virtual assistants help maintenance teams schedule and manage tasks by automating routine processes such as work order creation and equipment status updates. These tools reduce administrative burdens, allowing technicians to focus on critical maintenance tasks instead of manual data entry.
- Integration with ERP, MES, and Supply Chain Systems: Future CMMS solutions are improving integration with manufacturing execution systems (MES), enterprise resource planning (ERP), and supply chain platforms. This parallel approach ensures maintenance planning aligns with production goals, inventory management, and procurement schedules, reducing downtime caused by equipment failures or spare part shortages.
- Sustainability-Focused Maintenance Strategies: Manufacturers prioritize energy-efficient and sustainable maintenance practices to reduce waste and lower operational costs. A CMMS and a capable MES can support these initiatives by tracking energy usage, optimizing maintenance schedules, and ensuring compliance with fit regulations.
- Automated Compliance and Safety Audits: Compliance tracking tools within CMMS software simplify audits by maintaining digital records of inspections, certifications, and regulatory maintenance requirements. Automation reduces non-compliance risk while ensuring that all equipment remains appropriately working.
Advancements in CMMS technology are reshaping maintenance strategies by improving efficiency, increasing automation, and reducing costs. Combining AI, IoT, and real-time data analytics ensures manufacturers can optimize maintenance operations while keeping production lines running smoothly.
Manufacturers worldwide are adopting digital solutions to improve efficiency, precision, and scalability. At 42Q, we combine decades of manufacturing expertise with cutting-edge technology to deliver smart connected manufacturing. Our flexible, cloud-native MES platform enhances visibility, streamlines operations, and accelerates digital transformation. Discover how our solutions can empower your factory to achieve its full potential.
Key Takeaways
- A computerized maintenance management system (CMMS) automates maintenance tracking, work order scheduling, and asset management, reducing downtime in manufacturing.
- Integrating CMMS software with an MES ensures seamless coordination between maintenance and production, improving efficiency and reducing operational risks.
- Predictive maintenance powered by IoT and AI helps manufacturers schedule repairs based on real-time equipment data, preventing costly failures.
- Compliance tracking within a CMMS in manufacturing simplifies audits by maintaining digital records of maintenance activities, inspections, and regulatory requirements.
- Cloud-based CMMS solutions provide manufacturers with remote access, automated updates, and scalable deployment, making maintenance operations more efficient and cost-effective.
FAQs
A computerized maintenance management system (CMMS) is a software tool that automates maintenance tracking, schedules repairs, and manages asset lifecycles. It helps manufacturers reduce downtime, improve efficiency, and optimize maintenance resources.
A CMMS in MES connects maintenance activities with production schedules, ensuring real-time equipment monitoring and automated work order management. This integration helps maintenance teams prevent disruptions while optimizing machine uptime.
Industries such as automotive, aerospace, medical devices, and consumer electronics rely on CMMS software to maintain regulatory compliance, improve asset reliability, and reduce maintenance costs. Any industry that depends on continuous production benefits from a CMMS.
Predictive maintenance in a CMMS in manufacturing uses IoT sensors and historical performance data to identify early signs of wear or failure. Maintenance tasks are scheduled based on actual asset conditions, reducing unnecessary servicing and preventing unexpected breakdowns.
A manufacturing CMMS lowers maintenance costs by preventing equipment failures, reducing emergency repairs, and optimizing spare parts inventory. Automated maintenance scheduling ensures resources are used efficiently, helping manufacturers control expenses while improving productivity.
How 42Q is Shaping the Next Era of Manufacturing
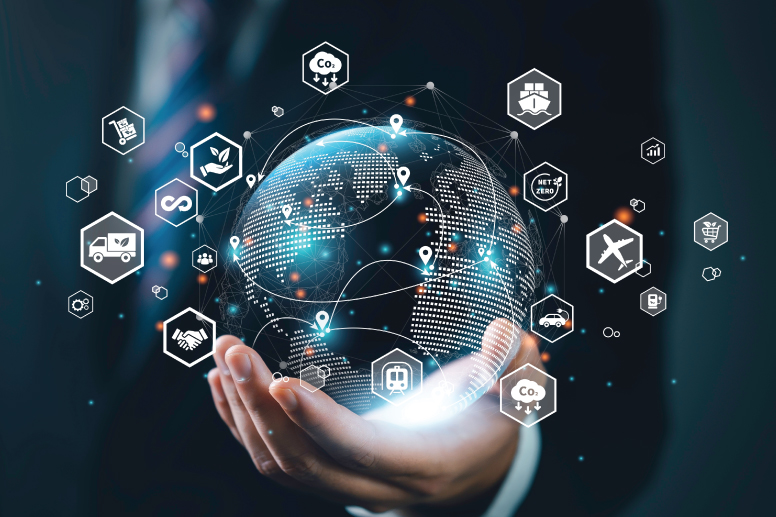
Building a Smarter, Greener Future
How 42Q is Shaping the Next Era of Manufacturing
As we approach Hannover Messe, the manufacturing world is buzzing with anticipation. It’s a time to reflect on where the industry is headed and how we can tackle the challenges of tomorrow. At 42Q, we’ve spent the past year working closely with manufacturers to address two of the most pressing issues facing the industry today: sustainability and the intelligent use of technology.
This isn’t about chasing trends, it’s about solving real problems. Manufacturers are under pressure to do more with less: less waste, less downtime, and less complexity. At the same time, they need to stay competitive in a rapidly changing landscape. That’s where we come in. Over the past 12 months, we’ve made significant strides in helping manufacturers achieve operational excellence while building a foundation for a more sustainable future.
Sustainability: It’s a Goal, and a Journey that requires Focus
Let’s be honest… sustainability isn’t just a nice-to-have anymore. It’s a business driver. But for many manufacturers, the path to sustainability isn’t always clear. How do you reduce waste without sacrificing efficiency? How do you optimize resource use without overhauling your entire operation? These are the questions we’ve been working to answer.
Data as the Foundation for Sustainable Manufacturing
At 42Q, we believe that sustainability starts with visibility. You can’t improve what you can’t measure. That’s why we’ve focused on giving manufacturers the tools to see their operations clearly—from energy use to material waste to equipment performance.
Our Connected Manufacturing platform, built on AWS, pulls data from across the production floor and beyond, giving manufacturers a unified view of their operations. This isn’t just about collecting data; it’s about turning that data into actionable insights. For example, by analyzing cycle times and defect rates, manufacturers can pinpoint inefficiencies and reduce waste. By monitoring energy consumption, they can identify opportunities to cut costs and lower their environmental impact.
Modular Solutions for Sustainable Growth
Another way we’re helping manufacturers build sustainability into their operations is through our composable MES architecture. Traditional manufacturing systems often come with a lot of unnecessary baggage—features you don’t need, complexity you don’t want, and costs you can’t justify. Our modular approach lets manufacturers build a system that’s tailored to their specific needs, without the bloat.
This isn’t just good for the bottom line; it’s good for the planet. By only using what you need, you reduce waste—both in terms of resources and energy. And because the system is designed to grow with you, it ensures that sustainability is built into your operations from the ground up.
AI in Manufacturing: Not Just the Hype, But Real Value
There’s a lot of talk about AI in manufacturing, and frankly, a lot of it is overhyped. But when applied thoughtfully, AI can deliver real value. Over the past year, we’ve been working to integrate AI into our platform in ways that actually make a difference for manufacturers.
Arthur: Making AI Work for You
One of our proudest accomplishments this year has been the rollout of Arthur, our AI-powered assistant. Arthur is a practical tool designed to make life easier for manufacturers. Think of it as a knowledgeable colleague who’s always there to help. Need to troubleshoot a machine? Arthur can guide you through it. Looking for real-time production data? Arthur can pull it up in seconds.
What makes Arthur truly valuable is its ability to streamline workflows and reduce downtime. By providing instant access to critical information, Arthur helps manufacturers make faster, smarter decisions. And because it’s powered by Amazon Bedrock, it’s constantly learning and improving, ensuring that it stays relevant as your needs evolve.
AI Beyond the Hype: Predictive Maintenance and Quality Control
Beyond Arthur, we’re also exploring how AI can be used to tackle some of the biggest pain points in manufacturing. For example, predictive maintenance is a game changer for reducing downtime and extending the life of equipment. By analyzing data from sensors and historical performance, AI can predict when a machine is likely to fail—before it happens. This not only saves time and money but also reduces the waste associated with unexpected breakdowns.
Similarly, AI can play a key role in quality control. By analyzing production data in real time, AI can detect defects early in the process, reducing waste and ensuring that only high-quality products make it to market. These aren’t futuristic ideas—they’re practical applications of AI that are delivering real results today.
What We’ve Achieved: A Year of Progress
Looking back over the past 12 months, we’re proud of what we’ve accomplished. Here are a few highlights:
- Connected Manufacturing: We’ve helped manufacturers gain a unified view of their operations, enabling them to make smarter, more sustainable decisions.
- Arthur: Our AI-powered assistant has become an indispensable tool for manufacturers, streamlining workflows and reducing downtime.
- Composable MES: Our modular approach has given manufacturers the flexibility they need to build systems that grow with them, without unnecessary waste or complexity.
- Strategic Partnerships: We’ve strengthened our collaborations with industry leaders, ensuring that our customers have access to the best tools and expertise available.
Looking Ahead: What’s Next for 42Q?
As we head into Hannover Messe, we’re more committed than ever to helping manufacturers navigate the challenges of tomorrow. Sustainability and AI will continue to be key focus areas, but we’re also looking at new ways to drive efficiency, reduce complexity, and empower manufacturers to do their best work.
We’re excited to share our latest innovations at the show, and we look forward to connecting with manufacturers who are ready to take their operations to the next level. Because at the end of the day, our goal is to help manufacturers build a smarter, greener, and more efficient future.
The Future of Automotive Manufacturing and MES
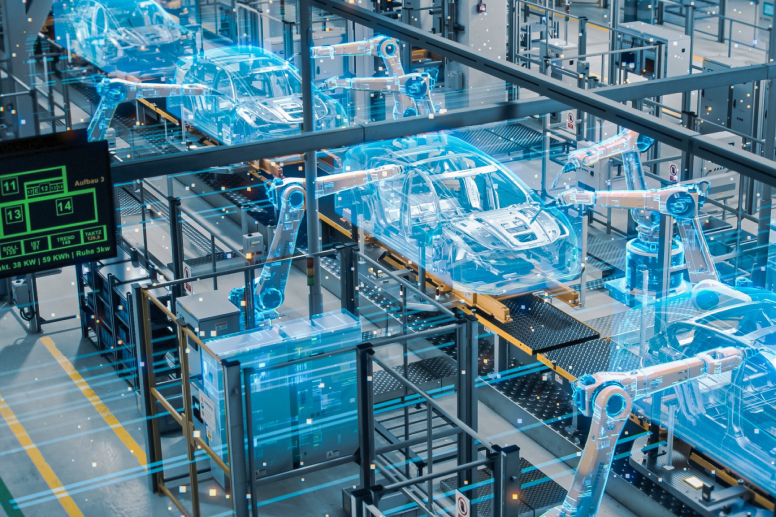
The Future of Automotive Manufacturing and MES
Manufacturing Execution Systems (MES) are forming automotive production, improving efficiency, quality, and traceability across the factory floor.
As manufacturing complexity increases, companies must manage production schedules, reduce waste, and meet regulatory requirements while maintaining cost control. MES bridges the gap between enterprise resource planning (ERP) systems and factory operations, providing real-time data, automation, and process optimization. Automotive manufacturers adopting MES gain improved visibility, streamlined workflows, and enhanced production capabilities, ensuring they meet the growing industry with greater precision and reliability.
What is Automotive Manufacturing in MES?
Automotive manufacturing involves complex processes that form raw materials into fully functional vehicles. This industry relies on precision engineering, supply chain coordination, and quality control to ensure production efficiency and product reliability. Manufacturers seek solutions to enhance operations while reducing costs and production timelines as technology advances.
A Manufacturing Execution System (MES) plays an essential role in modern automotive production by bridging the gap between enterprise resource planning (ERP) systems and factory floor operations. MES provides real-time monitoring, data collection, and process automation, helping manufacturers optimize production workflows, improve traceability, and ensure compliance with industry regulations. With increasing efficiency and scalability, MES solutions are now essential for manufacturers looking to streamline operations and meet customer expectations.
Benefits of MES in Automotive Manufacturing
Automobile manufacturers must maintain high production standards while adapting to shifting market conditions. MES improves factory operations by providing digital tools that track performance, optimize workflows, and enhance overall productivity. These benefits help manufacturers lower costs, reduce errors, and maintain consistency throughout production.
- Production efficiency: MES automates data collection, reducing manual errors and ensuring accurate process tracking. This improves workflow efficiency and minimizes production downtime.
- Quality control: Real-time monitoring allows manufacturers to detect and address defects before they escalate, improving product quality and reducing waste.
- Traceability and compliance: MES provides full product traceability, recording each manufacturing process step. This helps meet regulatory requirements and improves audit readiness.
- Workforce optimization: Operators receive digital work instructions, reducing training time and enhancing worker efficiency on the factory floor.
- Supply chain visibility: MES integrates with ERP and other business systems, providing better visibility into material availability and production schedules. This improves planning and reduces delays.
- Cost reduction: Process automation and predictive maintenance reduce material waste, energy consumption, and unplanned downtime, lowering production costs.
- Scalability: MES supports multi-plant operations, allowing manufacturers to standardize processes across multiple facilities while maintaining centralized control.
Manufacturers implementing MES gain better control over production while improving agility in responding to operational challenges. These advantages make MES an essential tool for automotive companies looking to improve efficiency and maintain high-quality manufacturing standards.
Examples of MES in Automotive Manufacturing
Manufacturers rely on MES to improve efficiency, maintain product quality, and meet production goals. The system integrates with factory operations to support automation, provide real-time insights, and improve traceability. These capabilities address specific challenges in automotive manufacturing, ensuring consistent results across production lines.
1. Digital Work Instructions for Assembly Processes
Automotive production involves assembling thousands of components with precision. MES provides digital work instructions, guiding operators through each step with real-time updates. This reduces errors, minimizes rework, and ensures each vehicle meets quality standards. Operators can also receive automated alerts for process deviations, preventing defects before they affect production.
2. Production Monitoring and Performance Analytics
Factory performance depends on accurate data collection and analysis. MES tracks production rates, machine uptime, and operator efficiency, providing manufacturers with real-time insights into performance metrics. These analytics help identify bottlenecks and inefficiencies, allowing process adjustments that improve production speed and output quality.
3. Traceability for Compliance and Quality Assurance
Automotive manufacturing requires complete traceability of parts and materials to meet industry regulations. MES records each step of production, capturing data on material origins, assembly processes, and quality checks. If a defect occurs, manufacturers can trace the issue back to its source and take corrective action, reducing the risk of recalls and compliance violations.
4. Automated Inventory and Supply Chain Integration
Supply chain coordination is essential to prevent material shortages and production delays. MES integrates with inventory management systems, tracking material usage in real time and automating restocking processes. This prevents overstocking or understocking issues, ensuring materials arrive at the right time to maintain production schedules.
5. Predictive Maintenance to Reduce Downtime
Equipment failures cause unplanned downtime, delaying production and increasing costs. MES uses predictive maintenance tools to monitor machine performance and detect potential failures before they happen. Automated alerts notify maintenance teams when repairs or servicing are needed, preventing breakdowns and extending equipment lifespan.
Automotive manufacturers rely on MES to enhance production processes, improve quality control, and optimize resource allocation. These applications make MES a critical tool for increasing efficiency while reducing costs and minimizing operational risks.
Challenges in Automotive Manufacturing
Automotive manufacturers face complex operational challenges that affect production efficiency, cost control, and regulatory compliance. Meeting industry requirements while maintaining high output levels requires advanced solutions to manage factory operations effectively. MES helps address these obstacles by providing visibility, automation, and process control.
- Supply chain disruptions: Material shortages, supplier delays, and logistical constraints slow production. Manufacturers must adjust schedules and inventory levels to avoid production halts.
- Quality assurance and defect management: Identifying defects early in the process reduces rework and scrap costs. Without a formed tracking system, maintaining consistent product quality becomes difficult.
- Equipment downtime and maintenance inefficiencies: Unexpected equipment failures lead to production stoppages, increasing costs and delaying deliveries. Predictive maintenance and performance monitoring help minimize unplanned downtime.
- Regulatory compliance and traceability: Automotive manufacturers must meet strict safety regulations. Tracking materials, production steps, and testing data ensure compliance while reducing the risk of recalls.
- Production scalability: Expanding production capacity requires standardizing processes across multiple facilities. Without centralized control, scaling operations lead to inconsistencies and inefficiencies.
- Workforce training and process standardization: Operator errors and inefficient workflows reduce production speed. Digital work instructions and automated process controls improve training effectiveness and operational consistency.
- Energy consumption and sustainability requirements: Reducing waste and improving energy efficiency helps manufacturers lower costs and meet goals. Process optimization and resource monitoring provide better control over energy usage.
Manufacturers that address these challenges improve production efficiency, product quality, and overall operational stability. MES provides solutions that help factories optimize resources, reduce costs, and maintain compliance with industry regulations.
How to Improve Efficiency in Automotive Manufacturing with MES
Manufacturers rely on MES to improve production efficiency, reduce operational risks, and optimize factory performance. The system provides data-driven insights, automation tools, and real-time monitoring to streamline processes. These capabilities help factories maintain quality while minimizing costs and production delays.
Automating Data Collection and Process Tracking
Manual data entry slows production and increases the risk of errors. MES automates data collection, capturing real-time production metrics from machines, sensors, and operators. This ensures accurate tracking of key performance indicators (KPIs) such as cycle times, defect rates, and machine utilization. Automated data reporting allows manufacturers to identify inefficiencies and adjust processes to improve productivity.
Optimizing Production Scheduling and Resource Allocation
Balancing production schedules with material availability and workforce capacity prevents delays and inefficiencies. MES synchronizes scheduling with inventory and labor management systems, ensuring that materials arrive on time and operators follow optimized workflows. This reduces bottlenecks, minimizes idle time, and maximizes overall production output.
Enhancing Quality Control with Real-Time Monitoring
Defects impact production costs and customer satisfaction. MES integrates with quality control systems to monitor product specifications, detect anomalies, and flag defects as they occur. Automated alerts notify operators when deviations happen, allowing immediate corrective actions. This reduces waste, improves product consistency, and lowers rework costs.
Implementing Predictive Maintenance to Minimize Downtime
Equipment failures lead to unplanned downtime and increased repair costs. Some MES solutions offer capabilities that address equipment downtime. These systems are capable of collecting data on machine performance and, depending on their features, may be able to predict maintenance requirements using historical data and real-time sensor inputs. This allows for proactive maintenance, with alerts being sent when servicing is needed, which can reduce unexpected failures. The goal of such features is to improve equipment reliability and prolong machine lifespans, minimizing production disruptions.
Standardizing Work Instructions for Consistent Operations
Operators need clear instructions to follow best practices and maintain process consistency. MES provides digital work instructions, ensuring each step of production is performed correctly. These instructions update in real-time based on machine status, production requirements, or regulatory changes. Standardizing workflows improves worker efficiency and reduces errors across multiple shifts and facilities.
Improving Traceability for Compliance and Supply Chain Visibility
Tracking materials, parts, and production processes ensures compliance with industry regulations. MES records each manufacturing stage, linking product batches to raw material sources and assembly data. This improves supply chain visibility and allows manufacturers to trace defects to their origin, reducing liability and improving quality control.
Reducing Waste and Improving Sustainability Efforts
Material waste and energy consumption increase production costs. Some Manufacturing Execution Systems (MES) can offer features that help manufacturers track things like energy use, material waste, and how efficiently materials are being used. This data can then be used to find ways to make processes better, reduce resource consumption, and be more environmentally friendly. If done well, this can help lower costs and meet environmental rules
Manufacturers using MES gain better control over production, improving efficiency while maintaining quality and compliance standards. The system provides the tools to optimize factory operations and reduce costs in an industry.
Evolution of Automotive Manufacturing and MES
Automotive manufacturing has advanced through technological innovations that improve efficiency, safety, and product quality. MES has adapted to support these advancements, providing digital tools that connect production processes and optimize factory operations. The industry's progression reflects a shift toward automation, data-driven strategy, and integrated manufacturing systems.
- Early mass production: The introduction of assembly lines standardized vehicle manufacturing, reducing production time and increasing output. Manual processes dominated, relying on human oversight and repetitive tasks.
- Introduction of automation: Robotics and computer-controlled machinery improved precision and consistency, reducing human error and increasing production speed. Automation helped streamline repetitive tasks while improving safety and efficiency.
- Integration of digital monitoring systems: Manufacturers adopted early versions of MES to track production metrics, monitor machine performance, and manage work orders digitally. These systems provided essential real-time insights but lacked full integration capabilities.
- Expansion of data-driven manufacturing: Advanced MES platforms integrated with ERP and supply chain systems allow manufacturers to analyze performance data and optimize workflows across multiple facilities. Predictive analytics and process automation further improved production efficiency.
- Adoption of smart factories: Modern MES solutions incorporate artificial intelligence, machine learning, and cloud computing to connect production lines with enterprise systems. Smart factories use real-time data to improve traceability, automate and improve production control.
- Sustainability and energy-efficient manufacturing: MES often includes tools for tracking resource consumption, optimizing energy use, and reducing material waste. These capabilities help manufacturers meet standards while lowering operational costs.
Automotive manufacturing continues to grow with advancements in automation, digital connectivity, and sustainability initiatives. MES is vital in supporting these developments, ensuring manufacturers achieve higher efficiency, lower costs, and improved production outcomes.
Key Trends in Automotive Manufacturing and MES
Manufacturers continue integrating innovative technologies into production, improving efficiency and reducing costs through automation and data-driven insights. MES is essential in optimizing factory operations by incorporating artificial intelligence, Internet of Things (IoT) connectivity, and predictive analytics. Cloud-based MES solutions allow greater scalability and system accessibility, reducing the need for expensive on-premise infrastructure. Sustainability initiatives drive the adoption of energy-efficient manufacturing practices, with an MES capable of monitoring real-time resource consumption to minimize waste. Cybersecurity measures remain a priority as factories connect more systems and data sources, ensuring that production information remains secure. MES-ERP integration strengthens business continuity, aligning production workflows with broader enterprise objectives for better inventory control, planning, and efficiency. Automotive manufacturers rely on these advancements to improve quality, reduce downtime, and maintain compliance with industry regulations.
Manufacturers worldwide are adopting cloud-based solutions to improve efficiency, precision, and scalability. At 42Q, we combine decades of manufacturing expertise with cutting-edge technology to deliver innovative, connected manufacturing. Our flexible, cloud-native MES platform enhances visibility, streamlines operations, and accelerates digital transformation. Discover how our solutions can empower your factory to achieve its full potential.
Key Takeaways
- MES improves efficiency in automotive manufacturing by automating workflows, reducing downtime, and providing real-time visibility into production processes.
- Traceability features help manufacturers maintain compliance by tracking materials, components, and assembly processes throughout the production cycle.
- Predictive maintenance reduces machine failures and unplanned downtime by monitoring equipment health and scheduling repairs before breakdowns occur.
- Cloud-based MES solutions enhance scalability and flexibility by integrating factory operations across multiple facilities and improving data accessibility.
- MES-ERP integration strengthens manufacturing operations by aligning production schedules, resource planning, and inventory control with business objectives.
FAQs
MES improves efficiency by automating data collection, optimizing production scheduling, and reducing downtime through predictive maintenance. The system provides real-time monitoring, allowing manufacturers to adjust workflows, minimize bottlenecks, and maintain consistent output. With MES, production processes become more reliable, scalable, and cost-effective.
A comprehensive MES includes production tracking, quality management, resource planning, and traceability features. These components ensure real-time visibility into factory operations, helping manufacturers maintain compliance, reduce waste, and optimize machine utilization. Integrated digital work instructions also enhance operator efficiency and process consistency.
Traceability ensures compliance with safety regulations, reduces liability, and improves quality control by tracking each step in the manufacturing process. MES provides a digital record of materials, assembly processes, and testing data, allowing manufacturers to quickly identify and correct defects. This level of oversight helps prevent costly recalls and production delays.
MES uses machine data and sensor inputs to detect potential equipment failures before they happen. Predictive maintenance strategies reduce unplanned downtime, extend machine lifespan, and lower repair costs. By analyzing performance trends, MES ensures maintenance teams receive timely alerts for servicing, improving overall equipment efficiency.
MES focuses on real-time production management, process automation, and shop-floor monitoring, while ERP handles higher-level business operations like finance, procurement, and supply chain management. MES works with ERP to provide manufacturers with complete operational visibility, ensuring factory processes align with business goals.
15 MES Applications by Industry
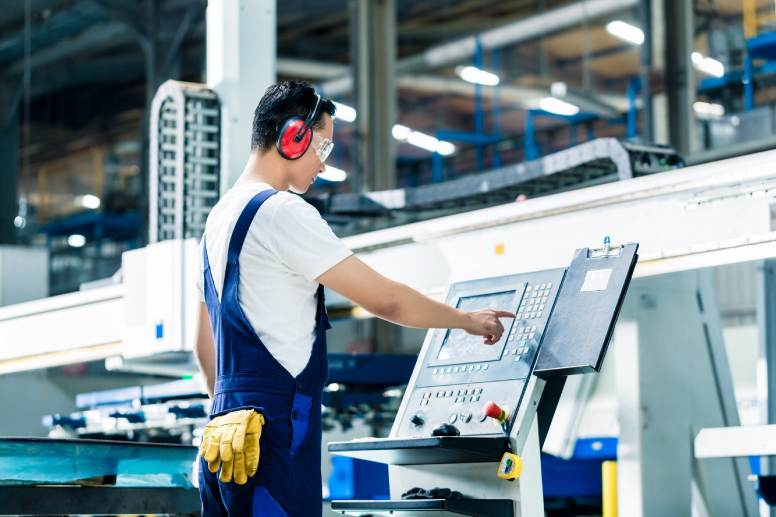
15 MES Applications by Industry
Manufacturers constantly seek ways to improve efficiency, reduce costs, and maintain high-quality production standards.
Manufacturing Execution Systems (MES) provide a critical solution by integrating real-time monitoring, automation, and data analytics into production workflows. These applications help manufacturers across various industries track production, optimize resource utilization, and ensure compliance with industry regulations. With the ability to reduce waste, improve traceability, and enhance operational control, MES applications play a key role in modernizing manufacturing and driving long-term growth.
Importance of MES in Manufacturing
Manufacturing Execution Systems (MES) play an essential role in modern production by connecting, monitoring, and controlling complex manufacturing processes. These systems bridge the gap between enterprise resource planning (ERP) and production equipment, ensuring accurate data flow and operational efficiency. As industries strive for greater agility, MES applications provide real-time insights that help you minimize downtime, improve quality, and maximize production output.
Integrating MES applications supports key operational areas, including production scheduling, traceability, quality management, and resource allocation. MES applications make data-driven by providing a centralized view of manufacturing activities, reducing errors, and optimizing workflows. This level of control is significant for industries that rely on precision and compliance, such as automotive, medical devices, and aerospace.
Beyond immediate operational improvements, MES applications also contribute to long-term scalability and cost reduction. With greater visibility into production processes, manufacturers can identify inefficiencies, enhance workforce productivity, and respond more effectively to fluctuations. These advantages make MES applications a critical investment for companies looking to optimize their operations and remain adaptable in data-driven manufacturing.
15 MES Applications by Industry
Manufacturing Execution Systems (MES) provide essential tools for industries that require precision, compliance, and efficiency in production. These applications help manufacturers monitor production in real-time, automate quality control, and improve operational workflows. Below are 15 MES applications categorized by industry, each addressing unique challenges while optimizing manufacturing processes.
Automotive Industry
Automotive manufacturers rely on MES applications to manage complex assembly lines, track components, and improve production efficiency. These systems help optimize workflows, minimize defects, and improve compliance with regulatory standards.
1. Real-Time Production Monitoring
Production inefficiencies result in lost time and increased operational costs. MES applications track production in real-time, collecting data from machinery and operators to identify bottlenecks, optimize throughput, and reduce delays. Manufacturers gain complete visibility into work orders, cycle times, and output, allowing quick adjustments that improve production efficiency.
Effective production monitoring also helps reduce scrap and rework. Immediate alerts notify operators of quality deviations, preventing defective parts from advancing further in the assembly process. This improves overall product consistency and reduces material waste.
2. Quality Assurance and Defect Tracking
Automotive manufacturers must maintain strict quality control throughout production. MES applications integrate with inspection systems to detect defects at early stages, preventing faulty parts from reaching final assembly. Real-time defect tracking making manufacturers to analyze failure trends, improving quality processes over time.
Detailed defect reports allow teams to implement corrective actions quickly, reducing scrap rates and minimizing the risk of expensive recalls. Capturing quality data at every step helps ensure compliance with automotive safety regulations while maintaining high production standards.
3. Traceability and Component Serialization
Manufacturers must track each component through the production cycle to ensure compliance with regulatory standards. MES applications provide full traceability by assigning serial numbers to components and recording their history, from supplier sourcing to final vehicle assembly.
Serialized traceability simplifies recall management by identifying specific batches of defective parts rather than requiring full-scale product recalls. This improves accountability while reducing liability risks for manufacturers and suppliers.
4. Just-in-Time (JIT) Inventory Management
Managing inventory efficiently prevents production delays and minimizes unnecessary costs. MES applications coordinate material deliveries with production schedules, ensuring that parts arrive when needed. This reduces excess stock, prevents shortages, and optimizes warehouse space.
Automated inventory tracking helps reduce lead times and improves supply chain reliability. Keeping inventory levels aligned with production grow minimizes waste while supporting lean manufacturing principles.
5. Workforce and Task Allocation
Optimizing labor allocation improves productivity and reduces idle time. MES applications assign tasks based on worker availability, skill levels, and production priorities, ensuring that each station operates efficiently.
Smart scheduling improves resource utilization by aligning work assignments with operational needs. Skill-based allocation reduces human errors, while digital work instructions provide operators with step-by-step guidance to improve efficiency.
Medical & Pharmaceutical Industry
Strict regulatory requirements make MES applications essential in medical and pharmaceutical manufacturing. These systems ensure compliance, track product quality, and improve documentation accuracy.
6. Electronic Batch Record (EBR) Management
Paper-based record-keeping increases the risk of human errors and non-compliance. MES applications digitize batch records, ensuring accurate and complete documentation for every production run.
Electronic batch records improve traceability and simplify audit preparation. Manufacturers can store, retrieve, and update production data in a centralized system, reducing paperwork and ensuring compliance with industry standards such as FDA 21 CFR Part 11.
7. Real-Time Process Monitoring
Precise control over production conditions ensures product safety and consistency. MES applications monitor temperature, pressure, and humidity in real-time, preventing deviations that could compromise product integrity.
Automated alerts notify operators of variations in process conditions, reducing the risk of contamination or defective batches. This level of monitoring supports Good Manufacturing Practices (GMP) and improves regulatory compliance.
8. Regulatory Compliance Support
Regulatory agencies require detailed production records and audit trails. MES applications automate compliance reporting, reducing the manual effort needed to prepare for audits.
Automated compliance tracking helps ensure that all manufacturing processes adhere to industry regulations. Digital logs provide transparency and prevent errors in documentation, reducing the risk of regulatory violations.
9. Equipment Calibration and Maintenance Tracking
Maintaining properly calibrated equipment is essential for consistent product quality. MES applications track calibration schedules and log maintenance activities to prevent equipment failures.
Automated maintenance reminders reduce unplanned downtime and extend asset lifespan. Preventive maintenance ensures machines operate at peak performance, supporting reliable and repeatable production processes.
10. Batch and Product Traceability
Tracking raw materials and final products improves product safety and recall management. MES applications provide complete traceability from ingredient sourcing to final packaging.
Automated traceability reduces risks associated with contamination or defects. When recalls are necessary, manufacturers can quickly identify affected batches, reducing financial losses and protecting consumer safety.
Food and Beverage Industry
Food manufacturers use MES applications to improve safety, maintain quality standards, and optimize production workflows. These systems provide real-time process monitoring and automate compliance tracking.
11. Recipe and Ingredient Management
Precision in ingredient measurements ensures product consistency. MES applications store digital recipes and track ingredient usage to prevent formulation errors.
Standardized recipe management reduces variability between batches. Automated recipe enforcement helps manufacturers maintain uniform product quality across different production facilities.
12. Food Safety and Compliance Tracking
Food manufacturers must meet strict safety regulations. MES applications monitor processing conditions, track ingredient sources, and automate compliance reporting.
Automated food safety tracking prevents contamination risks and simplifies regulatory audits. Digital logs provide proof of compliance with safety standards, reducing legal and financial risks for manufacturers.
13. Production Scheduling and Workflow Optimization
Optimizing production workflows improves efficiency and reduces operational costs. MES applications balance workloads, align production with market, and prevent bottlenecks.
Real-time scheduling adjustments help manufacturers meet order deadlines without unnecessary delays. Better workflow management improves labor efficiency and reduces raw material waste.
14. Waste Reduction and Yield Optimization
Minimizing waste lowers costs and improves profitability. MES applications analyze production data to identify inefficiencies, allowing manufacturers to optimize ingredient usage and reduce overproduction.
Data-driven insights help manufacturers refine processes to maximize yields. Reduced food waste improves sustainability efforts while increasing operational efficiency.
15. Packaging and Labeling Verification
Accurate labeling is essential for regulatory compliance and consumer safety. MES applications automate packaging processes, verifying ingredient lists, expiration dates, and nutritional information.
Automated label verification prevents mislabeling errors, reducing product recalls. Consistent labeling ensures that consumers receive accurate information while meeting compliance requirements.
Benefits of Implementing MES Applications
Manufacturing Execution Systems (MES) improve production efficiency, reduce operational costs, and enhance product quality by providing real-time visibility and process automation. These applications support manufacturers in industries where precision, compliance, and scalability are critical. Implementing MES applications leads to measurable improvements across production lines, supply chain operations, and workforce management.
- Improved Production Efficiency: Automating workflows reduces manual data entry, minimizes human errors, and accelerates production cycles. MES applications provide real-time monitoring of manufacturing activities, allowing manufacturers to identify bottlenecks and optimize machine utilization. A data-driven approach to production management helps reduce downtime, improve throughput, and streamline daily operations.
- Enhanced Product Quality and Traceability: Tracking materials, monitoring process parameters, and logging quality inspections at every production stage ensures consistent product quality. MES applications detect deviations in real-time, allowing operators to make immediate corrections. Full traceability simplifies compliance with industry regulations and improves response times for recalls or quality-related investigations.
- Cost Reduction Through Waste Minimization: Manufacturing waste leads to unnecessary costs and inefficiencies. MES applications analyze production data to identify where waste occurs, helping manufacturers adjust processes to improve material usage. Automating defect detection and optimizing workflows reduces scrap rates while ensuring that raw materials are used efficiently.
- Regulatory Compliance and Audit Readiness: Industries with strict compliance requirements benefit from automated documentation and compliance tracking. MES applications generate and store digital production records, ensuring that all manufacturing data is readily available for audits. Standardized reporting reduces the risk of regulatory violations and simplifies certification processes.
- Better Workforce Utilization: Assigning tasks based on skill levels, availability, and production priorities optimizes labor resources. MES applications automate workforce scheduling, reducing idle time and improving overall productivity. Digital work instructions help operators complete tasks more efficiently, reducing training time and minimizing errors.
- Seamless Integration With Supply Chain Operations: Synchronizing production schedules with material deliveries prevents disruptions caused by shortages or excess inventory. MES applications provide real-time updates on stock levels, helping manufacturers manage materials efficiently. Improved coordination between suppliers, manufacturers, and distributors ensures that production stays aligned with orders.
- Predictive Maintenance for Equipment Reliability: Equipment downtime disrupts production and increases costs. MES applications track machine performance data, detecting signs of wear or potential failures before breakdowns occur. Predictive maintenance reduces unplanned downtime, extends asset lifespan, and helps manufacturers maintain consistent production output.
- Scalability for Expanding Operations: Standardized processes and centralized data management allow manufacturers to scale operations without unnecessary complexity. Cloud-based MES applications provide multi-site visibility, allowing manufacturers to monitor and manage production across multiple facilities. Consistent workflows improve efficiency while supporting long-term growth.
Implementing MES applications allows manufacturers to improve efficiency, reduce operational risks, and maintain high-quality production standards. These systems provide a foundation for data-driven helping companies optimize resources while meeting industry compliance requirements. MES adoption supports manufacturers in achieving greater operational control, cost savings, and long-term scalability.
Future Trends in MES Applications
Manufacturing Execution Systems (MES) continue to move with advancements in automation, data analytics, and cloud computing. As manufacturers seek greater efficiency, flexibility, and visibility across operations, MES applications are integrating new technologies to meet industry grows.
Artificial intelligence (AI) and machine learning improve predictive analytics in MES applications, allowing manufacturers to optimize production scheduling, identify potential failures before they occur, and enhance quality control through automated defect detection. AI-driven insights help manufacturers make data-backed decisions that improve efficiency and reduce costs.
Cloud-based MES solutions provide multi-plant connectivity, allowing manufacturers to manage global operations through a centralized platform. Cloud deployment reduces infrastructure costs while ensuring real-time access to production data from any location. This shift supports manufacturers looking for scalable, remote-accessible solutions that improve collaboration between production sites.
Integration with the Industrial Internet of Things (IIoT) is improving data collection and equipment monitoring. Smart sensors connected to MES applications provide real-time machine performance data, helping manufacturers track overall equipment effectiveness (OEE), automate maintenance scheduling, and reduce unplanned downtime.
Augmented reality (AR) and digital twin technology enhance training and troubleshooting capabilities. AR-enabled MES applications allow technicians to visualize production processes, receive step-by-step guidance, and interact with digital representations of equipment for more efficient maintenance and problem-solving.
Cybersecurity is becoming a priority as MES applications handle increasing production data. Enhanced security features, including multi-factor authentication, encryption, and secure cloud storage, ensure manufacturers protect sensitive information while complying with industry regulations.
MES applications will continue integrating with emerging technologies to improve manufacturing efficiency, quality control, and supply chain coordination. As automation and data-driven processes advance, manufacturers will rely on MES solutions to maintain operational agility and optimize production.
Manufacturers worldwide embrace cloud-based solutions to achieve efficiency, precision, and scalability. At 42Q, we combine decades of manufacturing expertise with cutting-edge technology to deliver smart, connected manufacturing. Our flexible, cloud-native MES platform enhances visibility, streamlines operations, and accelerates digital transformation. Discover how our solutions can empower your factory to achieve its full potential.
Key Takeaways
- MES applications improve production efficiency by automating workflows, reducing errors, and optimizing machine utilization to minimize downtime and maximize output.
- Real-time monitoring and quality tracking enhance product consistency by detecting defects early and ensuring compliance with industry standards.
- Automated inventory and supply chain management prevent material shortages and overstocking, improving operational agility and cost efficiency.
- Regulatory compliance and audit readiness are simplified through digital records, automated reporting, and process standardization.
- Predictive maintenance features reduce equipment downtime by monitoring performance data and scheduling proactive maintenance before failures occur.
FAQs
An MES application is a software solution that monitors, tracks, and controls production processes in real time. It provides manufacturers with visibility into operations, automates data collection, and optimizes production workflows to improve efficiency and quality.
MES applications reduce manual data entry, minimize errors, and streamline workflows by automating production monitoring and scheduling. Real-time insights help manufacturers identify bottlenecks, allocate resources effectively, and minimize downtime to improve overall efficiency.
Industries such as automotive, aerospace, medical devices, food and beverage, and electronics manufacturing benefit significantly from MES applications. These sectors require precision, regulatory compliance, and real-time traceability, all of which MES applications provide.
MES applications automate documentation, track production data, and generate audit-ready reports. By maintaining digital records and enforcing process controls, MES solutions help manufacturers meet regulatory requirements in industries with strict compliance standards.
MES focuses on shop floor execution, providing real-time visibility into production processes, equipment performance, and quality control. ERP systems manage broader business functions such as finance, procurement, and supply chain management. Integrating MES with ERP ensures seamless coordination between production and enterprise operations.
What Are OEE Systems in Manufacturing?
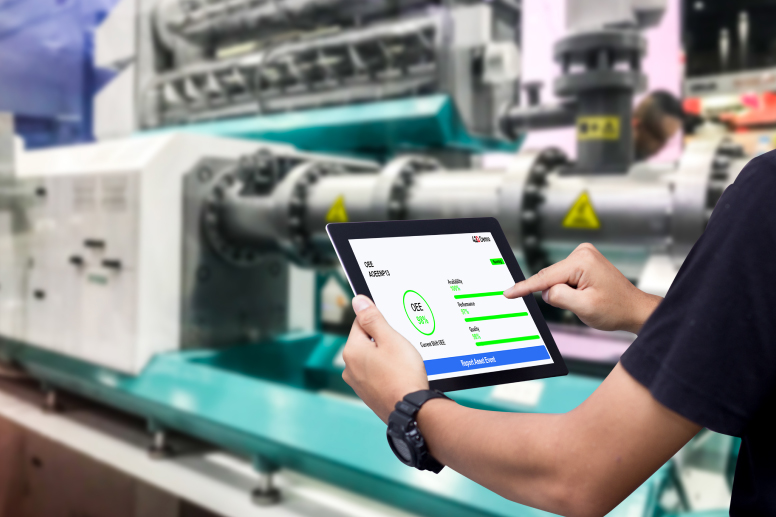
What Are OEE Systems in Manufacturing?
Manufacturers rely on Overall Equipment Effectiveness (OEE) to assess and improve production efficiency.
Measuring availability, performance, and quality helps identify bottlenecks, reduce unplanned downtime, and enhance productivity. Manufacturers struggle to maintain consistent output and operational reliability without accurate OEE tracking.
OEE systems in manufacturing provide actionable insights that allow businesses to improve machine utilization, streamline workflows, and optimize resource allocation. Understanding how to measure and apply OEE metrics reduces waste, improves product quality, and ensures production runs efficiently.
What Does OEE Stand For in Manufacturing?
Overall Equipment Effectiveness (OEE) is a standardized metric that quantifies manufacturing productivity by measuring how efficiently equipment operates. It evaluates three critical factors—availability, performance, and quality—to determine the percentage of planned production time that is genuinely productive. A perfect OEE score of 100% indicates flawless manufacturing: no unplanned downtime, no slow cycles, and zero defects.
Manufacturers rely on OEE to pinpoint inefficiencies, track continuous improvement initiatives, and optimize production output. By providing real-time visibility into equipment effectiveness, OEE systems in manufacturing help identify bottlenecks, reduce waste, and increase throughput. Understanding this metric is essential for improving operational efficiency and maintaining a driving edge in modern production situations.
Importance of OEE Systems in Manufacturing
OEE systems in manufacturing provide a structured approach to identifying and eliminating inefficiencies in production. Every unplanned stoppage, slow cycle, or defective product directly affects output and profitability. Without accurate data on these losses, manufacturers struggle to implement meaningful improvements. OEE systems quantify equipment effectiveness, offering clear insights into performance trends and production constraints.
Operational visibility is essential for improving production efficiency and reducing waste. OEE data helps manufacturers identify recurring downtime causes, assess equipment performance, and implement targeted maintenance strategies. Instead of reacting to breakdowns, businesses can shift to proactive measures that extend machine lifespan, optimize workforce utilization, and maximize throughput.
Key Components of OEE in Manufacturing
OEE systems in manufacturing evaluate equipment efficiency using three fundamental metrics: availability, performance, and quality. Each component identifies specific production losses and provides insight into areas requiring improvement. Understanding these factors helps manufacturers reduce downtime, optimize production speed, and improve product quality.
Availability: Minimizing Downtime and Maximizing Production Time
Availability measures the percentage of planned production time that equipment remains operational. Downtime caused by unplanned maintenance, changeovers, or raw material shortages reduces production efficiency. OEE systems track planned and unplanned stoppages, providing data that helps manufacturers address recurring issues.
Several factors contribute to availability losses, including unexpected equipment failures, lengthy setup times, and delayed material deliveries. Preventive maintenance programs, standardized changeover procedures, and better inventory management reduce disruptions. Increasing machine uptime ensures that production schedules remain consistent, improving manufacturing efficiency.
Performance: Ensuring Optimal Production Speeds
Performance evaluates how efficiently equipment operates compared to its designed capacity. Machines running at slower-than-expected speeds or experiencing frequent micro-stoppages contribute to performance losses. These inefficiencies reduce output without directly halting production, making them difficult to detect without real-time monitoring.
OEE tracking helps manufacturers identify process inefficiencies such as slow cycle times, suboptimal machine settings, and worn-out tooling. Addressing these issues improves production rates while maintaining consistent quality. Proper operator training, proactive machine adjustments, and automated process monitoring support higher performance levels.
Quality: Reducing Defects and Improving Product Consistency
Quality measures the percentage of manufactured products that meet specifications without requiring rework or scrap. Defective products lead to waste, increased costs, and additional labor for corrections. OEE systems track defect rates, providing insights into production inconsistencies and recurring quality issues.
Several factors, including improper machine calibration, inconsistent raw materials, and operator errors, contribute to quality losses. Real-time quality monitoring, automated defect detection, and process standardization help manufacturers maintain high product standards. Identifying and addressing the root causes of defects reduces material waste, improves customer satisfaction, and enhances overall production reliability.
How These Components Work Together
Availability, performance, and quality are connected, with losses in one area often affecting the others. A machine experiencing frequent downtime (availability loss) may also struggle to maintain optimal cycle times (performance loss). Likewise, running equipment at maximum speed without proper quality controls may lead to increased defects (quality loss).
OEE systems in manufacturing provide a structured approach to measuring and improving these key components. Tracking and analyzing OEE data helps manufacturers implement targeted improvements that enhance equipment reliability, increase throughput, and maintain high-quality production standards.
Benefits of Implementing OEE Systems in Manufacturing
OEE systems in manufacturing provide valuable insights that help manufacturers improve efficiency, reduce production losses, and maintain consistent product quality. Measuring availability, performance, and quality allows businesses to identify inefficiencies and take targeted actions that enhance productivity. Tracking OEE metrics provides a structured approach to minimizing downtime, improving machine reliability, and increasing output without requiring additional resources.
- Reduced Downtime and Unplanned Stoppages: Equipment failures and unexpected maintenance issues disrupt production schedules and reduce output. OEE tracking provides real-time data on recurring downtime causes, allowing manufacturers to implement proactive maintenance strategies. Predictive maintenance based on historical trends helps reduce breakdowns, ensuring machines operate reliably and production schedules remain uninterrupted.
- Increased Production Efficiency: Machines that operate below optimal speeds or experience frequent micro-stoppages lead to performance losses. OEE monitoring identifies slow-running equipment, enabling manufacturers to make necessary adjustments. Process optimization, better operator training, and automated tracking tools help improve production rates, ensuring machines perform at their designed capacity.
- Improved Product Quality and Defect Reduction: Defective products lead to material waste, rework, and increased operational costs. OEE systems track defect rates and identify patterns that indicate process inconsistencies or equipment malfunctions. Early detection of quality issues allows manufacturers to implement corrective actions before large-scale defects occur, maintaining high product standards while reducing scrap and rework expenses.
- Lower Operational Costs and Better Resource Utilization: Production inefficiency wastes valuable resources, from raw materials to labor hours. OEE data helps manufacturers optimize resource allocation by ensuring equipment operates efficiently, and workforce utilization remains balanced. Reducing material waste, minimizing energy consumption, and optimizing production workflows contribute to significant cost savings over time.
- Data-Driven Regulating for Continuous Improvement: Accurate and detailed production data allows manufacturers to identify trends and measure the effectiveness of process improvements. OEE reports provide insights into production bottlenecks, enabling businesses to implement data-backed changes that drive continuous operational improvements. Historical data tracking helps assess long-term trends and ensures sustained productivity gains.
- Sustainability and Waste Reduction: Manufacturing operations generate excess waste when inefficient processes or production defects occur. OEE tracking helps minimize unnecessary waste by improving equipment reliability, reducing defective output, and streamlining production workflows. Efficient manufacturing practices contribute to lower energy consumption and a reduced footprint, aligning with sustainability goals while maintaining cost-effective operations.
OEE systems in manufacturing provide structured insights that support efficiency improvements at every production stage. Tracking availability, performance, and quality metrics ensure manufacturers can pinpoint inefficiencies, reduce costs, and maintain a high standard of production output. Implementing OEE-driven improvements leads to measurable gains in productivity, operational stability, and long-term manufacturing success.
Real-World Applications of OEE in Manufacturing
OEE systems in manufacturing are widely used across industries to improve production efficiency, reduce downtime, and maintain high-quality standards. Manufacturers rely on OEE tracking to optimize processes, minimize losses, and ensure consistent output. Each industry applies OEE data to address specific challenges, from reducing machine failures in high-volume production to maintaining strict compliance in regulated sectors.
Automotive Production: Optimizing Assembly Line Efficiency
Automotive manufacturers depend on OEE tracking to maintain continuous production flow in high-speed assembly lines. Unplanned downtime in welding, stamping, and painting stations can cause costly delays and disrupt supply chain coordination. Monitoring availability helps manufacturers detect frequent stoppages, while performance tracking ensures robotic systems and conveyor lines run at optimal speeds. Quality metrics help identify production defects early, preventing faulty components from reaching final assembly. By applying OEE data, automotive manufacturers improve throughput while reducing waste and rework.
Medical Device Manufacturing: Ensuring Compliance and Quality
Medical device manufacturers operate under strict regulatory standards requiring precision, traceability, and consistency. OEE systems help track machine performance in critical operations such as injection molding, sterilization, and assembly. Availability data allows manufacturers to reduce downtime caused by maintenance or validation requirements, while performance monitoring ensures equipment operates within specified tolerances. Quality tracking helps detect defects in sensitive components, minimizing the risk of compliance issues and ensuring that all products meet the required specifications before distribution.
Semiconductor Fabrication: Enhancing Yield and Process Stability
Semiconductor manufacturing relies on OEE tracking to improve yield rates in highly complex and precise fabrication processes. Equipment availability is critical in wafer processing, where unexpected downtime leads to production losses and increased costs. Performance tracking ensures that lithography, etching, and deposition machines operate at optimal cycle times, reducing inefficiencies impacting product quality. Quality monitoring helps manufacturers detect process deviations that could lead to defective chips, allowing for real-time adjustments that protect overall yield.
Aerospace Component Manufacturing: Maintaining Production Reliability
Aerospace manufacturers use OEE systems to monitor production consistency in machining, composite fabrication, and surface finishing processes. Availability tracking helps reduce unplanned downtime in CNC machining and assembly operations, preventing disruptions in supply chain commitments. Performance monitoring ensures that materials such as aluminum and titanium are processed at the correct speeds to avoid defects of stress. Quality tracking supports precision manufacturing requirements, ensuring that critical aerospace components meet industry regulations and safety standards.
Industrial Equipment Manufacturing: Optimizing Multi-Line Production
Manufacturers producing heavy machinery, engines, and industrial components rely on OEE data to improve efficiency across multiple production lines. Availability tracking helps reduce production delays caused by long setup times and changeovers, while performance monitoring ensures machines operate at maximum capacity. Quality data allows manufacturers to detect recurring defects in castings, welded structures, and hydraulic components, leading to fewer warranty claims and improved product reliability.
OEE tracking provides manufacturers data-driven insights that improve efficiency, enhance quality, and support long-term operational stability. Industries implementing structured OEE measurement strategies gain higher production output, reduced waste, and more predictable manufacturing processes.
How to Effectively Measure OEE in Manufacturing
Measuring OEE in manufacturing requires a structured approach that captures accurate availability, performance, and quality data. A well-defined measurement system ensures manufacturers can identify inefficiencies, track production trends, and implement targeted improvements. Accurate OEE tracking provides a clear understanding of equipment effectiveness, helping businesses reduce downtime, improve production speed, and maintain product consistency.
- Define Equipment Availability: Availability measures the actual operating time of equipment compared to the planned production time. Calculating this metric requires subtracting all unplanned downtime, such as machine breakdowns, material shortages, and lengthy changeovers, from the total scheduled time. A lower-than-expected availability score signals recurring stoppages that must be addressed through preventive maintenance, better scheduling, or process adjustments.
- Monitor Performance Efficiency: Performance evaluates how well equipment operates at its designed speed. Machines that run slower than expected, experience frequent micro-stoppages or require frequent operator intervention reduce overall efficiency. Tracking cycle times helps manufacturers pinpoint performance issues caused by incorrect machine settings, worn-out tooling, or inconsistent material feed rates. Addressing these inefficiencies ensures machines produce at optimal speeds without compromising quality.
- Track First-Pass Quality Rates: Quality measures the percentage of products that meet specifications without requiring rework or scrap. To calculate this metric, manufacturers must track defect rates and analyze patterns in production errors. Common causes of quality losses include misaligned machine calibration, raw material inconsistencies, and operator errors. Identifying recurring quality issues requires manufacturers to implement corrective actions such as improved quality control procedures, automated defect detection, and stricter process standards.
- Use Automated Data Collection Systems: Manually tracking OEE metrics increases the risk of data errors and inconsistencies. Automated monitoring solutions, such as machine sensors, manufacturing execution systems (MES), and IoT tracking devices, provide real-time data on equipment performance. These systems capture production information more accurately, allowing manufacturers to respond to inefficiencies immediately rather than relying on retrospective analysis.
- Analyze OEE Trends and Historical Data: Measuring OEE once provides a snapshot of performance, but long-term tracking offers more profound insights into production patterns. Historical OEE data helps manufacturers assess the effectiveness of process improvements, compare performance across different shifts, and identify recurring inefficiencies. Regularly analyzing trends ensures that manufacturing operations continuously improve and that productivity gains are maintained over time.
- Set Benchmarks and Target Goals for Improvement: OEE measurement becomes more effective when manufacturers establish clear benchmarks based on industry standards or internal historical performance. Setting achievable OEE goals allows businesses to track progress and measure the success of process optimizations. Comparing OEE scores across different machines, production lines, or factory locations provides valuable insights into areas that require further refinement.
Implementing a structured OEE measurement process ensures manufacturers collect reliable data, identify inefficiencies, and improve production outcomes. Accurate tracking of availability, performance, and quality metrics supports continuous improvement efforts, helping manufacturers achieve higher efficiency and more consistent operational results.
Manufacturers worldwide are adopting data-driven solutions to improve efficiency, quality, and operational visibility. At 42Q, we combine decades of manufacturing expertise with cutting-edge technology to deliver innovative, connected manufacturing. Our flexible, cloud-native MES platform enhances visibility, streamlines operations, and accelerates digital factory change. Discover how our solutions can empower your factory to achieve its full potential.
Key Takeaways
- To assess manufacturing efficiency, OEE measures three key components—availability, performance, and quality.
- Reducing unplanned downtime through predictive maintenance and optimized changeovers improves equipment availability.
- Optimizing machine performance by addressing micro-stoppages and slow cycle times increases production output.
- Minimizing defects and rework ensures higher product quality while reducing material waste and operational costs.
- Implementing OEE tracking systems gives manufacturers data-driven insights to support continuous process improvements.
FAQs
OEE has been widely used in manufacturing since the 1980s when companies began adopting lean production methodologies. As digital tools and automation improved, OEE became a standard metric for evaluating production efficiency. Today, manufacturers rely on OEE tracking systems to optimize workflows and reduce operational losses.
OEE stands for Overall Equipment Effectiveness and is a key metric to assess manufacturing efficiency. It measures availability, performance, and quality to determine how effectively equipment is utilized. Tracking OEE helps manufacturers identify inefficiencies, reduce downtime, and improve product output.
OEE systems track machine availability and analyze unplanned downtime causes such as equipment failures, long setup times, and material shortages. Manufacturers can reduce stoppages and maintain a stable production flow using predictive maintenance and real-time monitoring. Preventing frequent breakdowns leads to increased uptime and higher productivity.
OEE is a comprehensive metric that combines three key factors—availability, performance, and quality—into a single effectiveness score. Unlike standalone metrics such as machine utilization or defect rate, OEE provides a holistic view of production efficiency. Using OEE alongside other key performance indicators (KPIs) gives manufacturers deeper insights into overall productivity.
Manufacturers can improve OEE scores by addressing availability losses, optimizing machine performance, and reducing quality defects. Strategies such as preventive maintenance, automated process monitoring, and workforce training help enhance efficiency. Using real-time OEE tracking systems allows businesses to make data-driven decisions that lead to continuous improvements.