Understanding ERP Manufacturing Execution Systems
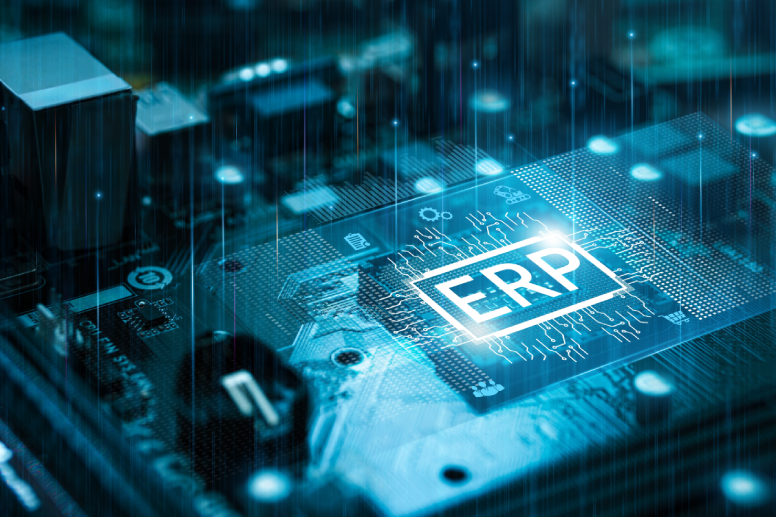
Understanding ERP Manufacturing Execution Systems
Integrating enterprise resource planning (ERP) systems with manufacturing execution systems (MES) is reshaping the way manufacturers operate.
This fusion delivers a powerful combination of real-time production insights and enterprise-level control, empowering manufacturers to address operational challenges, enhance decision-making, and streamline processes. With an increased demand for more intelligent, more connected factories, ERP-MES systems are becoming essential for achieving efficiency, accuracy, and growth in the manufacturing sector.
What is an ERP Manufacturing Execution System?
An ERP Manufacturing Execution System (MES) is a strategic integration that connects enterprise resource planning (ERP) software with MES technology to provide a unified solution for managing and optimizing manufacturing processes. ERP systems focus on overarching business operations such as finance, procurement, and inventory. In contrast, MES systems are designed to handle real-time production floor activities like scheduling, quality control, and performance monitoring.
Fusing these two systems enables manufacturers to streamline operations, minimize inefficiencies, and create a seamless data flow from the shop floor to the boardroom. Bridging the gap between operational and enterprise-level decision-making helps ERP-MES systems empower organizations to make more efficient decisions, improve productivity, and remain innovative.
How ERP and MES Systems Work Together
"ERP systems oversee high-level business processes like financial planning, procurement, and inventory management, while MES focuses on real-time production floor activities like scheduling, quality control, and performance monitoring."
The main difference between an ERP system and an MES lies in its focus and function. ERP systems oversee high-level business processes like financial planning, procurement, and inventory management. On the other hand, MES focuses on manufacturing operations, including production scheduling, quality assurance, and tracking real-time data on the factory floor.
When these systems work together, they create a robust ecosystem that ensures seamless communication between business and production processes. ERP provides the strategic oversight and long-term planning needed for resource allocation, while MES delivers real-time insights and control over manufacturing operations. Together, they close the gap between the administrative office and the factory floor, with data synchronization that improves decision-making, resource utilization, and operational efficiency.
For example, integrating ERP and MES systems allows inventory levels tracked by the ERP system to update dynamically based on production data provided by the MES. This ensures material shortages are avoided, production schedules remain on track, and customer demands are met promptly. This collaboration enhances both productivity and profitability across the organization.
Key Benefits of ERP-MES Integration
"Real-time data visibility enables manufacturers to identify inefficiencies and make informed decisions quickly, ensuring proactive management of production schedules and resource planning."
Integrating an ERP manufacturing execution system is a critical step for manufacturers to be efficient in modern production environments. These systems create a seamless connection between strategic planning and real-time operations, ensuring optimized workflows, enhanced visibility, and precise control over every aspect of the manufacturing process. By bridging this gap, ERP MES systems empower manufacturers to achieve better operational efficiency, improved quality, and scalability for growth. In this piece, we’ll focus on the key benefits and why this integration is essential for businesses in industries ranging from automotive to medical devices.
- Real-Time Data Visibility: ERP and MES systems work together to centralize data, giving manufacturers instant insights into production schedules, inventory, and operational metrics. This real-time access helps more informed decision-making and reduces inefficiencies on the factory floor.
- Enhanced Production Efficiency: Eliminating communication gaps between departments ensures production schedules align with material availability and workforce capacity. This streamlining of operations minimizes downtime and accelerates time-to-market.
- Improved Quality Control: With MES data seamlessly integrated into ERP systems, manufacturers can monitor production processes and quickly address potential quality issues. This ensures consistent adherence to industry standards while reducing defects.
- Scalability for Growth: ERP-MES integration allows businesses to maintain operational consistency across multiple locations. Whether scaling up production or adapting to demands, manufacturers can rely on these systems for stability and flexibility.
- Cost Savings Through Process Optimization: Streamlined workflows and improved operational efficiency reduce waste and carrying costs. Manufacturers can reinvest these savings into innovation and expansion efforts.
- Regulatory Compliance Support: By automating data collection and ensuring traceability , ERP-MES systems simplify adherence to industry regulations. Documentation for audits and certifications becomes easily accessible.
- Enhanced Customer Satisfaction: Integrated systems help ensure on-time deliveries, accurate production timelines, and consistent quality—all of which contribute to meeting or exceeding customer expectations.
Adopting an ERP manufacturing execution system offers manufacturers the opportunity to unify and optimize their operations, ensuring long-term success. With key benefits like real-time visibility, improved efficiency, and streamlined compliance processes, ERP MES systems are indispensable tools for any organization focused on innovation and growth. Investing in this integration now ensures not only immediate performance improvements but also the ability to adapt and succeed in future manufacturing challenges.
8 Steps for Implementing an ERP-MES System
A successful ERP-MES system implementation requires a structured and methodical approach to minimize risks and maximize benefits. With proper planning, manufacturers can align the system’s capabilities with their specific operational goals, ensuring a smoother transition and improved overall performance. Every phase, from evaluating business needs to post-deployment monitoring, plays a vital role in ensuring that the system delivers measurable improvements in productivity, compliance, and decision-making efficiency.
1. Assess Business Needs and Goals
Begin the process by conducting a comprehensive evaluation of your manufacturing operations. Identify pain points, inefficiencies, and areas where the integration can create value. Consider factors like production delays, resource allocation challenges, or data silos that slow decision-making. Define measurable goals such as reducing production downtime, improving product quality, or enhancing supply chain visibility. Setting clear objectives ensures the implementation delivers targeted outcomes.
2. Select the Right ERP-MES Solution
The success of the integration heavily depends on selecting software that aligns with your specific manufacturing processes. Evaluate solutions based on their compatibility with existing systems, scalability for future growth, and ability to support real-time data exchange. Focus on features like ease of use, vendor support, and compliance with industry-specific standards. Conduct demos and involve relevant stakeholders to ensure the solution meets technical and operational requirements.
3. Develop a Detailed Implementation Plan
A well-defined plan is crucial for a smooth rollout. Outline key milestones, resource requirements, and timelines to avoid unexpected delays or cost overruns. Assign roles and responsibilities to cross-functional teams, including IT, operations, and management, to ensure department alignment. Phased rollouts often prove effective, allowing you to test the system on a smaller scale before full deployment.
4. Ensure Infrastructure Readiness
Evaluate and prepare your existing infrastructure to support the ERP-MES integration. This includes assessing hardware, software, network capabilities, and security protocols. Upgrading outdated equipment or systems may be necessary to ensure seamless data exchange and operational efficiency. Collaborate with IT teams to address technical gaps and establish the system’s foundation for success.
5. Data Migration and Validation
Accurate and complete data migration is essential for the new system to function effectively. Cleanse and standardize existing data to eliminate inconsistencies or inaccuracies. Securely transfer critical information such as inventory records, production schedules, and supplier details into the new system. After migration, validate data accuracy and integrity through rigorous testing to prevent errors that could disrupt operations.
6. Train Employees on the New System
Comprehensive training equips employees with the skills to use the ERP-MES system effectively. Conduct workshops hands-on training sessions, and provide user-friendly guides tailored to different organizational roles. Address any concerns or resistance to change by highlighting the system’s benefits and demonstrating how it simplifies workflows. Continuous support during and after deployment ensures employees feel confident using the new tools.
7. Monitor and Optimize the System Post-Deployment
After rolling out the ERP-MES system, closely monitor its performance against predefined goals. Gather feedback from users to identify any operational bottlenecks, inefficiencies, or areas for improvement. Use real-time analytics and system-generated insights to fine-tune processes and ensure maximum value. Periodic reviews and updates align the system with business needs and technological advancements.
8. Establish Ongoing Support and Maintenance
Maintaining the system is vital for long-term success. Develop a support structure that includes vendor assistance, internal IT teams, and a robust help desk. Regular software updates, security checks, and system health monitoring protect against vulnerabilities and maintain optimal performance. Proactive maintenance ensures the ERP-MES system remains reliable and scalable as your organization grows.
Implementing an ERP-MES system is not just about adopting new technology—it’s about fostering an operational shift that delivers sustained improvements. Each step in the process is critical to creating a seamless integration that supports both immediate objectives and long-term growth. With the right planning and execution, manufacturers can unlock the full potential of ERP-MES systems, improving efficiency, reducing costs, and staying innovative in their industries. Ensuring ongoing support and periodic evaluations will further strengthen the system’s ability to adapt and evolve with organizational needs.
Overcoming Challenges in ERP-MES Deployment
Implementing an ERP-MES system transforms manufacturing operations, but can introduce unique challenges during deployment. Addressing these challenges requires strategic planning, strong stakeholder collaboration, and proactive solutions. Anticipating potential obstacles and preparing actionable strategies ensures smoother integration, reduces downtime, and maximizes the value of an ERP-MES system investment.
- Complexity of Integration: Connecting ERP and MES systems involves merging diverse data sources, software, and processes. Selecting a solution with high compatibility and engaging experienced technical support can reduce integration hurdles.
- Resistance to Change: Employees may resist new technologies due to fear of disruption or lack of familiarity. Clear communication, ongoing support, and robust training help teams embrace and utilize the system effectively.
- High Initial Costs: The upfront investment in an ERP-MES system can appear significant. Conducting a detailed cost-benefit analysis highlights long-term savings and operational improvements, justifying the initial expenditure.
- Data Security Risks: Merging data from production and business systems increases exposure to cyber threats. Choosing a system with strong security features, such as encryption and role-based access control, protects sensitive data.
- Customization Requirements: Manufacturing processes often require tailored solutions. Customizing ERP-MES systems to meet unique operational needs can be time-intensive. Selecting a flexible system that supports modular upgrades ensures scalability and adaptability.
- Downtime During Implementation: System deployment may temporarily disrupt manufacturing operations. Planning phased rollouts or testing the system in smaller environments minimizes downtime and avoids large-scale interruptions.
- Data Migration Challenges: Transferring historical data into the new system without errors can be complex. Ensuring thorough data validation during migration prevents inaccuracies and ensures system reliability.
Overcoming deployment challenges is critical to ensuring the success of ERP-MES system implementation. Careful preparation, clear communication, and collaborative efforts help manufacturers minimize disruptions and address key obstacles. Each challenge presents an opportunity to refine processes, enhance decision-making, and build a more resilient production environment. Proactively addressing these issues unlocks seamless integration and delivers the long-term benefits of improved productivity, operational efficiency, and scalability.
Maximizing ROI with ERP-MES Systems
Achieving a strong return on investment (ROI) with an ERP-MES system requires aligning the technology with business goals and focusing on measurable outcomes. Manufacturers can unlock significant value by leveraging the system’s capabilities to enhance efficiency, reduce costs, and improve customer satisfaction.
Streamlining operations is one of the most effective ways to maximize ROI. Integrating ERP and MES ensures data flows seamlessly across departments, reducing manual effort and operational bottlenecks. This leads to faster decision-making, higher productivity, and fewer production delays. Focusing on quality improvements also drives ROI. Real-time monitoring and reporting help manufacturers detect and resolve quality issues early in production. This minimizes waste, reduces rework, and ensures compliance with stringent industry standards.
Effective use of predictive analytics within the system supports equipment maintenance and lowers unplanned downtime. Monitoring real-time data from MES systems enables manufacturers to anticipate equipment failures and address issues before they disrupt operations. This increases uptime and extends the life of manufacturing assets. Maximizing ROI also involves training employees to use the ERP-MES system efficiently. Empowering your team with the knowledge and skills to leverage the system enhances productivity and drives better results across all operations.
These efforts ensure that ERP-MES integration delivers measurable business value, helping manufacturers optimize resources and meet customer demands. Focusing on these areas establishes a pathway to long-term operational excellence and financial success.
Future Trends in ERP and MES Technology
ERP and MES technologies continue to adapt to meet the demands of modern manufacturing. By integrating advanced innovations, these systems are driving operational efficiency, improving decision-making, and helping manufacturers to adapt to emerging challenges. Staying ahead of technological advancements is not just about remaining competitive—it’s about improving operations to achieve higher productivity, sustainability, and flexibility.
Below are some of the most influential advancements shaping the future of ERP and MES systems.
- Artificial Intelligence Integration: AI-powered capabilities are being embedded into ERP and MES systems to analyze vast datasets, forecast production schedules, and detect maintenance needs before they become critical. This integration enhances operational efficiency while reducing downtime and increasing predictive decision-making.
- Cloud-Based Solutions: Cloud technology is becoming the backbone of ERP and MES systems. It offers scalability, cost-effectiveness, and secure remote access to manage operations globally. Cloud platforms also allow for real-time visibility across facilities, supporting agile and connected manufacturing.
- Industrial Internet of Things (IIoT): IIoT-enabled ERP-MES systems leverage sensors and connected devices to gather real-time production data. This connectivity allows manufacturers to optimize operations, predict maintenance requirements, and enhance resource management through precise monitoring and control.
- Digital Twin Technology: Digital twins create virtual replicas of physical manufacturing systems, offering manufacturers the ability to simulate, monitor, and optimize operations. By integrating with ERP and MES systems, digital twins provide actionable insights into system performance.
- Advanced Analytics and Dashboards: Advanced analytics and dynamic dashboards are empowering manufacturers with actionable insights into production performance. Customizable dashboards help users to monitor KPIs, identify inefficiencies, and make data-driven decisions in real time, improving overall operational effectiveness.
The evolution of ERP and MES technology is reshaping how manufacturers approach efficiency, scalability, and sustainability. Adopting advancements such as AI, IIoT, and cloud-based solutions ensures businesses are equipped to address future challenges while staying ahead in their industries. By leveraging these powerful tools, organizations can enhance their processes, improve visibility, and drive long-term results.
Manufacturers worldwide are adopting integrated solutions to improve efficiency, visibility, and operational control. At 42Q, we bring decades of manufacturing expertise and advanced technology to deliver cloud-native ERP-MES solutions. Our innovative platform simplifies operations, optimizes resource allocation, and accelerates digital transformation. Learn how we can help your factory unlock its true potential.
Key Takeaways
- ERP-MES integration unifies enterprise-level planning with real-time production management, enabling data-driven decision-making.
- Manufacturers benefit from enhanced visibility, improved efficiency, and streamlined workflows.
- Scalable ERP-MES solutions support small and large manufacturers, adapting to diverse industries and operational needs.
- Sustainability is a growing focus, with ERP-MES systems helping businesses reduce waste and track environmental metrics.
- Advanced technologies like AI, IIoT, and edge computing are shaping the future of ERP-MES systems, offering increased efficiency and innovation.
FAQ's
An ERP-MES system bridges the gap between enterprise-level planning and real-time production management. Its purpose is to synchronize processes, improve data visibility, and enhance decision-making to boost overall operational efficiency in manufacturing.
ERP-MES integration provides centralized data, real-time monitoring, and streamlined workflows. These benefits lead to reduced downtime, improved production accuracy, and optimized resource utilization, which support better business outcomes.
ERP-MES systems are scalable, making them accessible to manufacturers of all sizes. Small manufacturers can benefit by reducing inefficiencies, automating manual processes, and improving production planning with the system's powerful features.
ERP-MES systems are versatile and serve industries including automotive, medical devices, aerospace, and clean energy. These systems support with productivity, compliance, and enable advanced operational control in various manufacturing environments.