Advancing Production Capabilities through ERP and MES Integration
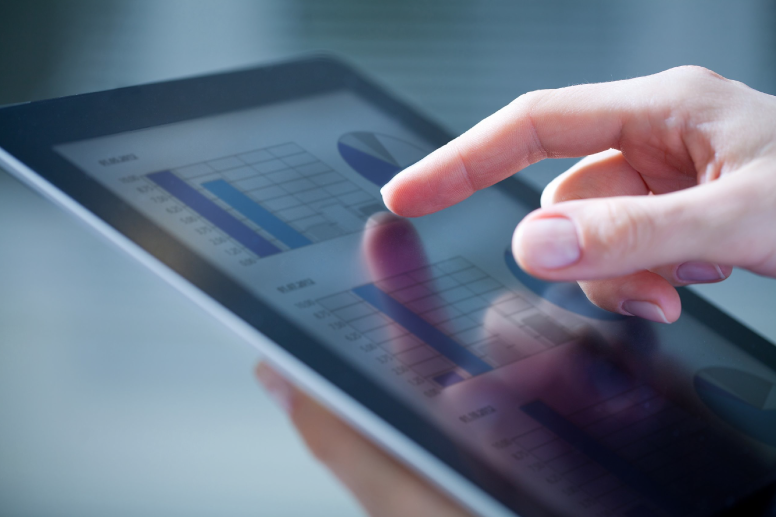
Advancing Production Capabilities through ERP and MES Integration
ERP and MES integration can open new avenues in manufacturing, giving you real-time oversight that enhances strategic decisions. Production floors often rely on a combination of hardware and software to manage everyday tasks, so a unified approach simplifies oversight at all levels. Operators gain an immediate understanding of inventory requirements and scheduling, while managers receive a clear view of resource allocation. This targeted efficiency supports faster releases and drives significant returns for stakeholders.
Global shifts highlight the importance of digital connectivity in production. Pressure to reduce costs, shorten lead times, and remain flexible often relies on integrated solutions that deliver insights around the clock. A well-planned connection between these systems introduces consistent workflows and minimized manual data entry. Many organizations are seeking a fully coordinated system that fosters greater collaboration, higher throughput, and measurable performance gains.
Understanding ERP and MES Integration in Manufacturing
Manufacturers often rely on distinct systems to manage production and administrative tasks. ERP and MES integration is critical for bridging this gap, allowing data to flow seamlessly across the entire operation. Managers who implement these solutions gain real-time access to production metrics, labor efficiency reports, and billing details. This synergy reduces errors from manual data entry and strengthens overall production control.
Integrating both platforms also improves traceability and compliance efforts. Quality checks become more accurate, and historical records remain at the ready for audits or product investigations. A connected ecosystem fosters better collaboration between departments, leading to consistent results and stronger process improvements. Organizations that invest in a robust approach to merging these systems often spot new opportunities for scale and efficiency.
Key Benefits of Integrating ERP and MES
Many leaders strive to unlock the full potential of manufacturing operations. A unified platform serves as a launchpad for streamlined workflows, cost-effective processes, and better control over raw materials. Consistent data sharing between MES and ERP eliminates misinformation and enables stable outputs. This approach can lower administrative burdens and free up resources for strategic objectives.
- Enhanced visibility: Operators and supervisors receive immediate feedback on resource usage, material requirements, and production stages.
- Improved cost efficiency: Real-time tracking of materials and labor hours reduces financial waste, enabling businesses to adjust budgets swiftly.
- Faster speed to market: Centralized oversight helps shorten production cycles, bolstering delivery times for customers.
- Stronger collaboration: Shared data fosters a deeper sense of partnership among cross-functional teams, leading to proactive problem-solving.
- Better data accuracy: Automated synchronization of transactions, production details, and inventory levels curtails duplication and manual errors.
Stronger clarity around planning, scheduling, and output lays a foundation for consistent growth. Modern manufacturing ecosystems reap additional advantages when shared data streams guide pivotal decisions. Visibility across production lines and corporate operations saves time, money, and labor. A closer look at best practices ensures these benefits become a reality on a wider scale.
Best Practices for Successful ERP and MES Integration
Leaders often focus on structured methods when merging ERP and MES. Effective planning sets the stage for a reliable system rollout and reduces friction among teams. Each stage of implementation demands proper communication and meticulous execution to avoid misalignment. Adopting best practices ensures a seamless transition, minimizes disruptions, and creates lasting improvements across manufacturing operations.
Clear Scope Definition
Defining the scope clearly at the beginning prevents scope creep and operational confusion. Teams must explicitly outline what the integration aims to achieve, including detailed objectives related to cost efficiency, throughput, and data visibility. This approach helps align the technical selection of hardware and software components directly to business goals. Establishing clear milestones and checkpoints further assists in tracking progress, addressing any deviations swiftly, and ensuring the project's objectives are consistently met.
Early Stakeholder Engagement
Engaging stakeholders early in the integration process significantly improves alignment and reduces resistance. Stakeholders across departments, including production, IT, finance, and quality control, should participate in initial planning sessions to express requirements and identify potential obstacles. This inclusive strategy ensures multiple perspectives are incorporated, fostering a sense of ownership and commitment among participants. Additionally, regular stakeholder briefings throughout the project enhance transparency, facilitate feedback, and build continuous support that drives successful implementation.
Structured Data and Governance
A structured approach to data governance is essential to successful ERP and MES integration. Standardizing and cleansing data, such as part numbers, bills of material, and routing instructions, reduces inconsistencies and errors during integration. Clearly defined governance policies establish accountability, define data ownership, and set protocols for data handling and security. Implementing robust governance structures also facilitates easier compliance management, provides clarity during audits, and enables smooth scaling when extending the integrated system to new manufacturing sites or processes.
Comprehensive Training and Support
Providing thorough training and continuous support to users and administrators is crucial for successful integration. Comprehensive training programs should cover system functionalities, data entry standards, troubleshooting procedures, and best practices. Equipping employees with user-friendly documentation, online resources, and dedicated support channels ensures they can navigate the new system confidently. Consistent post-implementation support addresses issues promptly, reinforcing user adoption, maximizing system utilization, and providing long-term efficiency.
Regular Performance Reviews and Optimization
Conducting regular performance reviews after implementation helps ensure the ERP and MES integration remains effective and aligned with evolving business needs. Monitoring system performance against predefined metrics, such as data accuracy, throughput speed, and cost savings, enables continuous improvement. Periodic reviews provide insights into areas requiring optimization, ensuring the integrated systems remain agile and responsive to changing manufacturing conditions. A commitment to ongoing optimization supports lasting efficiency gains and maximizes return on investment.
Common Challenges in ERP and MES Integration
Some organizations face a range of obstacles when aligning these systems. Delays or miscommunication can derail efforts and limit return on investment. Multiple variables, including legacy technology and user skepticism, require careful attention. These difficulties often arise when planning is incomplete or insufficient resources are allocated to critical stages.
- Limited IT resources: Lack of skilled personnel or inadequate budgets can stall progress and slow the introduction of new features.
- Incompatible legacy systems: Older platforms may require specialized middleware or extensive updates to function seamlessly with modern systems.
- Resistance from employees: Longtime staff members may be hesitant to adopt new tools, underscoring the importance of training and open dialogue.
Teams that anticipate these challenges often build stronger project plans from the start. Early audits of existing infrastructure, stakeholder alignment sessions, and ongoing communication mitigate many sources of risk. Leaders who address these complexities proactively foster a more stable connection between ERP and MES. Awareness of potential pitfalls lays the groundwork for a smoother transition.
The Role of PLM in ERP and MES Integration
Product Lifecycle Management (PLM) solutions merge design, production, and after-market processes for a comprehensive view of product data. Information captured during design can guide production settings on the shop floor, ensuring consistent quality outputs. This loop of constant feedback helps leaders identify inefficiencies and prioritize improvements across production lines. Seamless interaction among ERP, PLM, and MES platforms unifies critical data streams that once existed in isolation.
Stakeholders benefit from having design data linked to real-time manufacturing metrics to reveal patterns that drive cost savings and faster releases. This synergy cuts down on rework and fosters a deeper sense of accountability across every phase of a product’s journey. Companies that integrate PLM with ERP and MES often tap into previously hidden operational capacities. A dynamic communication loop ensures that each stage remains aligned to market requirements.
Future Trends in ERP and MES Integration
Machine learning and artificial intelligence are gaining traction for predictive maintenance and process optimization. Sensor data from the shop floor can be analyzed in real time to recommend adjustments that avoid downtime or quality issues. This level of insight positions teams to respond promptly and increase production precision. Cloud-based architectures also attract interest because they simplify deployment and allow faster expansion.
Augmented reality tools show promise for advanced operator training, remote collaboration, and ongoing safety improvements. Robotics often work hand in hand with connected systems, creating consistent output and reducing labor-intensive tasks. Upcoming developments suggest deeper integration of supply chain systems to create a more holistic view of procurement and inventory. Organizations that stay agile will likely discover new ways to refine their technology stack and stay ahead of shifting requirements.
Manufacturers worldwide are adopting cloud-based solutions to achieve efficiency, precision, and scalability. At 42Q, we combine decades of manufacturing expertise with cutting-edge technology to deliver connected manufacturing. Our flexible, cloud-native MES platform enhances visibility, streamlines operations, and accelerates digital factory advancement. Discover how our solutions can empower your factory to reach its full potential.
Key Takeaways
- A unified ERP and MES platform allows real-time data exchange that drives process consistency and measurable gains.
- A structured plan for scope, governance, and stakeholder collaboration helps prevent confusion and costly delays.
- Thorough user training and regular system audits address potential setbacks and strengthen adoption.
- PLM solutions connect design and manufacturing data, opening fresh insights for product improvements and faster releases.
- Cloud-based architectures, AI, and robotics continue to shape the future of integrated manufacturing systems.
FAQs
ERP and MES integration links backend business processes with shop floor production data. This connection ensures consistent information flow and allows you to fine-tune resource planning, scheduling, and quality management. Manufacturing outcomes often improve thanks to real-time insights and precise data.
Managers gain immediate updates on labor hours, material usage, and production status. Accurate information leads to faster adjustments, reducing waste and operational expenses. Greater clarity over expenditures also helps in budgeting and resource allocation.
The main difference between these three platforms lies in their core responsibilities and data focus. ERP manages corporate and financial processes, MES focuses on real-time production activities, and PLM centralizes product design and lifecycle information. When used in combination, they offer a more comprehensive framework for efficient output and improved scalability.
Many legacy platforms can merge with modern solutions through middleware or targeted software upgrades. This approach addresses compatibility concerns and aligns older equipment with new data protocols. The result is a seamless flow of information without the need for a total system overhaul.
Clear objectives and early stakeholder involvement often produce better alignment and acceptance. Comprehensive training and open communication lower resistance and reinforce consistent data standards. Ongoing reviews of performance metrics help sustain progress and refine best practices.