6 Benefits of Composability in Manufacturing
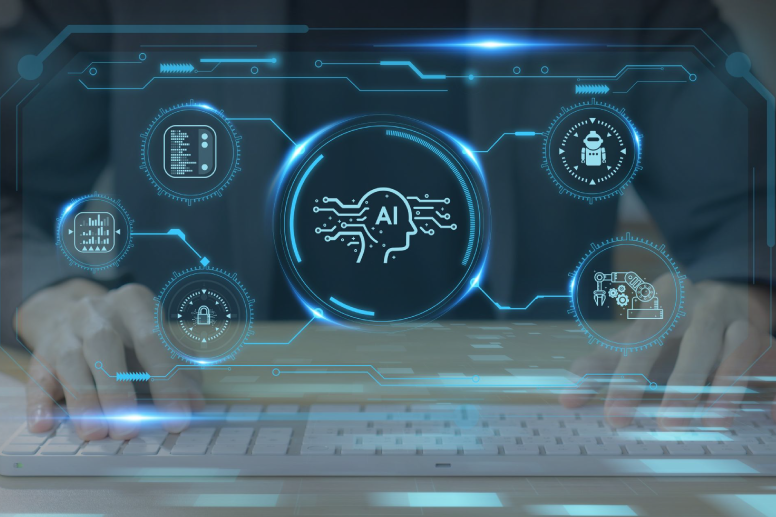
6 Benefits of Composability in Manufacturing
Composability in manufacturing refers to the ability to combine modular components in a flexible and efficient way to meet specific production needs. It allows manufacturers to break down complex systems into simpler, easily manageable pieces that can be reconfigured, upgraded, or scaled as needed. This approach leads to increased efficiency, faster adaptation to changes, and a significant reduction in costs. Embracing composability is essential in today’s highly competitive manufacturing environment, where businesses must respond quickly to changing market demands and technological advancements. By integrating composability into manufacturing processes, companies can unlock new opportunities for growth, innovation, and optimization.
What is Composability in Manufacturing?
Composability in manufacturing involves assembling different modular components within production processes to create flexible, adaptable, and efficient systems. Each component can function independently or interconnect with others, making it possible to add, remove, or reconfigure specific modules with minimal disruption. This approach promotes better responsiveness when demands shift, technologies evolve, or production requirements grow more complex. Manufacturers benefit from streamlined workflows, easier scalability, and the opportunity to adopt cutting-edge solutions without overhauling their entire operation.
Composability is rooted in the concept of designing processes to be change-ready. Modular design allows manufacturers to update individual elements without impacting the overall production pipeline, saving both time and resources. Businesses can replace legacy components or introduce novel solutions whenever the need arises, which accelerates innovation and fosters continuous improvement. This is especially important in a sector where new methods, materials, and regulations often emerge, requiring agile responses and robust operational structures that protect profitability and product quality.
MES and Composability
Manufacturing Execution Systems (MES) play a crucial role in enabling composability in modern manufacturing environments. These systems act as the backbone of a connected, flexible, and scalable factory. By incorporating modular components into MES platforms, manufacturers can achieve greater flexibility in adapting to specific production needs. MES solutions that support composability allow for seamless integration with various tools, equipment, and processes across the factory floor. This means that manufacturers can implement changes quickly, ensure optimal resource utilization, and drive innovation in production workflows, all while reducing operational complexities. With the right MES in place, the benefits of composability are more achievable and impactful than ever before.
6 Benefits of Composability in Manufacturing
The advantages of composability in manufacturing are numerous. Below are six key benefits that illustrate how adopting composable systems can enhance operational efficiency and drive success.
1. Enhanced Agility
Manufacturers today face constant pressure to adapt to shifting market conditions, supply chain disruptions, and customer demands. One of the most significant benefits of composability is its ability to enhance agility in production processes. With modular systems, manufacturers can quickly adjust production lines, replace outdated components, or integrate new technologies without disrupting the entire workflow. This flexibility ensures faster response times, improved throughput, and better alignment with market trends. The ability to pivot quickly offers manufacturers a competitive advantage, allowing them to stay ahead in the industry.
2. Improved Scalability
As businesses grow, their operational requirements change. Composability allows manufacturers to scale production capabilities up or down as needed without significant investments in new infrastructure. Modular systems enable businesses to add or remove components to match the level of demand, ensuring resources are allocated effectively. Whether expanding operations to new facilities or adapting to seasonal fluctuations in demand, composability provides the flexibility to adjust production capacity quickly and cost-effectively. This scalability is essential for long-term growth and ensures that businesses can meet market demands without incurring excessive costs or inefficiencies.
3. Cost Efficiency
Cost control is a critical concern for any manufacturing operation. Composability helps reduce costs by allowing manufacturers to optimize their resource usage and avoid unnecessary expenses. Modular components can be replaced or upgraded individually, eliminating the need for large-scale overhauls or expensive custom-built solutions. This approach also reduces downtime, as manufacturers can swap out faulty components or implement improvements without shutting down entire systems. Additionally, composable systems promote better inventory management, as manufacturers can adjust their production to match actual demand, avoiding the costs associated with overproduction or stockpiling. These cost-saving benefits significantly improve the bottom line.
4. Better Resource Utilization
Effective resource utilization is essential for maximizing the efficiency of manufacturing processes. Composability enables manufacturers to make the most of their existing resources by tailoring production processes to specific needs. With modular systems, businesses can allocate resources more effectively, ensuring that machinery, labor, and materials are used in the most efficient way possible. This reduces waste and ensures that production lines are running at optimal capacity. Furthermore, better resource utilization can lead to fewer delays, higher product quality, and reduced energy consumption, all of which contribute to improved overall performance.
5. Increased Innovation
In today’s competitive market, innovation is key to staying relevant and achieving long-term success. Composability fosters innovation by allowing manufacturers to experiment with new technologies and processes without risking major disruptions to existing systems. Because modular components can be swapped in and out easily, manufacturers can pilot new ideas, test improvements, and implement innovative solutions with minimal risk. This adaptability encourages creativity within the production environment, leading to faster implementation of new features, enhanced product designs, and the ability to respond to consumer needs more effectively. Innovation is made more accessible when businesses can integrate new technologies into their workflows seamlessly.
6. Seamless Integration
A primary benefit of composability is its ability to facilitate seamless integration between different tools, systems, and technologies within the manufacturing environment. By adopting modular systems, manufacturers can integrate new software applications, sensors, or machinery without disrupting existing operations. This integration reduces the complexity of managing diverse technologies and ensures that all components work together efficiently. With the right composability framework in place, manufacturers can integrate their operations with other systems, such as Enterprise Resource Planning (ERP) or supply chain management tools, resulting in smoother workflows and improved data sharing across departments. Seamless integration ultimately leads to enhanced collaboration and faster decision-making.
Examples of Composability in Manufacturing
Examples of composability highlight how modular systems can make manufacturing processes more adaptable, scalable, and cost-effective. These examples often showcase how everyday production tasks benefit from plug-and-play components that ensure minimal downtime. Organizations use composable frameworks to simplify tasks like assembly line reconfigurations, product customization, and equipment updates, without the need for full-scale replacements. This flexibility is essential for aligning production capabilities with new opportunities, emerging technologies, and business objectives.
- Modular production lines: Modular systems allow manufacturers to set up production lines that can be adjusted to different product types, volumes, or configurations without requiring major reengineering.
- Flexible automation: Robotic systems and automated equipment that can be easily reprogrammed or replaced based on changing production needs.
- Cloud-based MES solutions: Modular MES platforms that can integrate with a variety of production tools and systems, enhancing visibility and flexibility.
- Customizable assembly workflows: Workflow automation that can be reconfigured to suit varying production requirements, improving both efficiency and throughput.
- Digital twins: Virtual replicas of physical assets that allow manufacturers to simulate and optimize production processes, helping identify potential improvements.
These examples demonstrate that composability is more than just a buzzword; it is a strategic method for improving efficiency and responsiveness. Each composable element supports easier maintenance, faster upgrades, and better alignment between diverse production requirements. This approach empowers decision-makers to refine their operations based on accurate data insights, while limiting waste and downtime. By applying these examples, organizations can refine their existing processes, stay ahead of market shifts, and maintain stable growth in any manufacturing setting.
Common Challenges Implementing Composability in Manufacturing
Adopting composability in manufacturing offers many rewards, but there are hurdles to address before those rewards become reality. Leaders may encounter issues integrating modular components with legacy systems or finding skilled personnel who can support advanced automation. Organizational resistance can also slow the transition if teams are hesitant to shift away from traditional production approaches. Understanding these potential obstacles can help businesses develop practical strategies to successfully integrate composable designs.
- Integration complexity: Connecting disparate systems and technologies can be difficult, particularly if legacy systems are involved.
- Training requirements: Employees may need specialized training to adapt to new modular systems, which could lead to short-term disruptions.
- Cost of initial setup: While composable systems offer long-term savings, the upfront investment in modular components and software can be significant.
- Resistance to change: Employees or stakeholders who are accustomed to traditional manufacturing processes may resist transitioning to more flexible, modular systems.
- Data management: Managing and integrating the vast amounts of data generated by composable systems can be overwhelming without the right infrastructure in place.
Awareness of these challenges is the first step toward creating a roadmap for smoother composability adoption. Clear communication, robust training programs, and targeted technology investments can mitigate most of the difficulties that appear when introducing modular methods. Collaboration across departments ensures that each group understands the value of composability, easing common points of resistance. As organizations address these implementation barriers, they become better positioned to maximize long-term gains in efficiency, innovation, and agility.
Future Trends in Composability
Looking ahead, composability is expected to continue shaping the future of manufacturing. The ongoing advancements in IoT, AI, and cloud computing will only further enhance the flexibility and scalability of composable systems. With the integration of smart devices and sensors, manufacturers will have greater visibility and control over their production processes, enabling more precise adjustments and improvements. Additionally, the rise of Industry 4.0 and smart manufacturing technologies will create new opportunities for composability to thrive, making manufacturing systems more intelligent, automated, and connected than ever before.
Manufacturers worldwide are embracing cloud-based solutions to achieve efficiency, precision, and scalability. At 42Q, we combine decades of manufacturing expertise with cutting-edge technology to deliver smart connected manufacturing. Our flexible, cloud-native MES platform enhances visibility, streamlines operations, and accelerates digital transformation. Discover how our solutions can empower your factory to achieve its full potential.
Key Takeaways
- Composability allows manufacturers to adapt quickly to market changes and technological advancements, enhancing agility.
- Modular systems provide scalability, allowing manufacturers to adjust production capacity without major infrastructure changes.
- Composability leads to cost savings by reducing downtime and allowing for more efficient resource utilization.
- Modular systems enable better resource management, reducing waste and optimizing production workflows.
- Implementing composability promotes innovation by making it easier to integrate new technologies and experiment with improvements.
FAQs
Composability in manufacturing refers to the ability to integrate modular components into production systems, allowing for flexibility, scalability, and customization of workflows. This approach helps manufacturers adapt to changing demands and implement new technologies quickly.
Composability helps manufacturers reduce costs by enabling the use of modular components that can be upgraded or replaced without the need for major system overhauls. This results in savings from reduced downtime, optimized resource allocation, and the avoidance of large-scale investments.
MES plays a vital role in composability by providing a cloud-based platform that enables seamless integration of various systems, equipment, and workflows. MES helps manufacturers manage production in real time, ensuring greater efficiency and flexibility.
Composability fosters innovation by providing manufacturers with the ability to experiment with new technologies, products, and processes without disrupting existing systems. This makes it easier to implement new ideas and quickly adapt to market changes.
The challenges of implementing composability include integration complexities, initial setup costs, employee training, and potential resistance to change. However, the long-term benefits outweigh these challenges for manufacturers willing to adapt.