Why Agile Manufacturing Starts with a Composable, AI-Ready MES
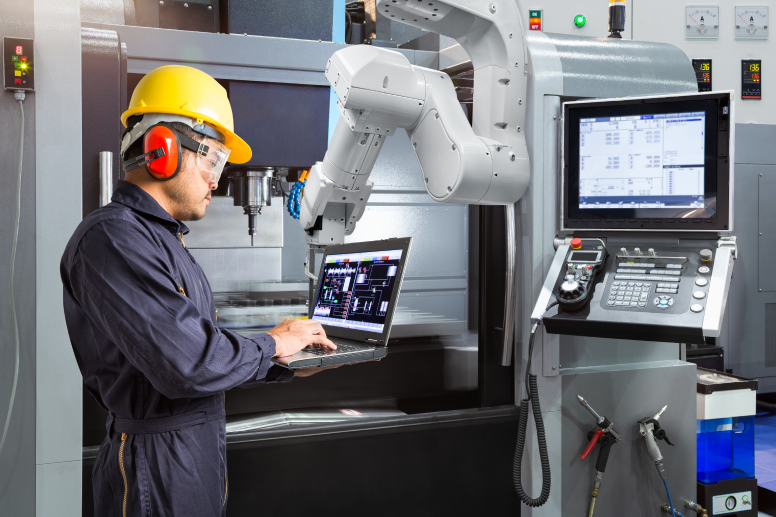
Why Agile Manufacturing Starts with a Composable, AI-Ready MES
Rigid, monolithic manufacturing systems can no longer keep up with modern demands.
To remain competitive, manufacturers must pivot to a composable, cloud-native MES architecture infused with artificial intelligence. This combination enables the agility, efficiency, and scalability that legacy systems lack. Forward-thinking manufacturers realize that a modular, AI-powered MES is not just an IT upgrade – it’s a strategic necessity for driving down costs, accelerating time to market, improving quality, and building a resilient operation.
Composability in manufacturing, which signifies building systems from independent, interchangeable components, is central to this necessity. Instead of a single, rigid system, a composable Manufacturing Execution System (MES) utilizes distinct modules that can be flexibly added, removed, or updated without affecting the entire operation. This approach helps manufacturers adapt to evolving demands, facilitates the integration of new technologies, and optimizes processes with enhanced flexibility and precision.
Traditional MES Hinders Manufacturing Agility
Traditional manufacturing execution systems (MES) were not built for change. Many factories still rely on monolithic, on-premises MES that are deeply customized and rigid. This inflexibility directly undercuts a manufacturer's ability to adapt quickly. Common issues with traditional MES include:
- Rigid architecture slows adaptation: Hard-coded workflows require lengthy reprogramming to handle process changes, delaying time to market.
- Siloed systems and data: Legacy MES often struggles to integrate with modern enterprise systems or IIoT devices, resulting in fragmented data, manual workarounds, and poor real-time visibility.
- Costly customizations and upgrades: Heavy customization makes upgrades cumbersome and expensive, locking plants into outdated software and raising maintenance costs.
- Limited scalability: Monolithic solutions cannot easily scale to new facilities or higher volumes without major effort. This hinders growth and the agility to ramp up output when demand spikes.
- Inflexible processes impact quality: When quality issues or new regulations emerge, traditional MES cannot adjust quickly. This results in inconsistent quality or compliance gaps.
These constraints translate to lost opportunities and higher operating costs. In a fast-moving market, a static MES means slower responses to customer demands, longer production lead times, and an inability to continuously improve operations. Manufacturing leaders recognize that clinging to these legacy systems is untenable if they want to compete on speed, efficiency and innovation.
Composable MES: A Modular Approach to Future-Ready Manufacturing
To achieve agility, manufacturers are shifting from rigid systems to composable MES architectures. A composable MES is built from a set of interoperable, plug-and-play modules rather than one giant application. Each module can operate independently yet integrate through open APIs and a unified data platform. This modular, cloud-native approach offers the flexibility to support a future-ready operation.
Gartner predicts that by 2027, 80% of manufacturing operations management solutions will be cloud-native and edge-driven. Unlike traditional MES, a composable MES can be reconfigured on demand. Need to add a new process or data source? Easier to deploy another module or service without overhauling the entire system. If a capability needs an upgrade, it can be improved in isolation and rolled out, reducing disruption to other functions. The result is a system evolving with the business.
Crucially, a modular MES can accelerate speed to market. Gartner reports that organizations embracing composability delivered new features 80% faster than competitors, enabling them to respond more swiftly to disruptions or customer demands by deploying new capabilities as needed. This modular model is also cost-effective; after the initial investment it reduces the cost of future changes and expansions, lowering total cost of ownership.
It also enhances traceability and quality. All modules share data to a common backbone, contributing to end-to-end visibility of production. This makes it easier to trace materials, processes, and results across different parts of the operation. If a quality issue arises, manufacturers can help pinpoint the root cause faster across connected modules.
Integrating AI with Composable MES Enhances Operational Efficiency
Making MES modular is only part of the transformation. The next level of efficiency comes from integrating artificial intelligence into these composable systems. Nearly 93% of industrial manufacturers already use AI in some form within their operations – from machine vision inspection to predictive analytics – underscoring how critical AI has become for productivity. A cloud-based, composable MES offers an ideal foundation to embed AI at key points in the workflow. By doing so, manufacturers can convert the massive streams of shop-floor data into actionable insights and autonomous decisions.
In a modular architecture, AI-driven tools can plug in more smoothly as another set of services. Below are several ways that integrating AI with a composable MES drives greater operational efficiency:
Predictive Maintenance Minimizes Downtime
Machine learning algorithms in an AI-enhanced MES analyze equipment sensor data and production trends to predict machine failures before they happen. Instead of reacting to breakdowns, maintenance is scheduled proactively when AI signals an issue. This reduces unplanned downtime, extends equipment life, and increases asset utilization while lowering maintenance costs. Ultimately, this leads to more reliable operations and a better bottom line.
Automated Quality Control and Traceability
Integrated into a composable MES, AI-powered vision systems inspect products in real time, catching defects that traditional methods might miss. They can flag anomalies on the line and trigger immediate corrective actions. All events are recorded, giving granular traceability to pinpoint where any fault occurred. This enables faster root-cause analysis and supports continuous improvement. The result is a higher first-pass yield and helps achieve compliance with strict quality standards.
Intelligent Scheduling and Resource Optimization
Advanced algorithms can rapidly recalibrate production schedules in response to real-time conditions – for example, a machine outage or a rush order. Re-planning production might take managers hours; an AI-driven scheduling engine can do it in seconds, optimizing throughput and minimizing idle time. This gives manufacturers greater agility, enabling shorter lead times and faster order fulfillment. Intelligent resource optimization also cuts waste, lowering the cost per unit with automations that can cut costs by 30%.
Adopting Composable MES Positions Manufacturers for Sustained Success
Manufacturers face unrelenting pressure: customers demand faster delivery and high quality, and disruptions can strike at any time. A modular, AI-ready MES can help provide the agility to pivot quickly – whether reconfiguring for a new product or scaling up to meet a surge in demand. It also future-proofs operations. New technologies can be added as modules without overhauling the system, and cloud delivery helps ensure updates roll smoothly. This approach is rapidly becoming the norm, and early adopters gain an edge. Key benefits include lower costs from reduced downtime and scrap, faster time to market, easier scalability, and improved quality through better traceability. Manufacturers that embrace this shift can better weather disruptions and seize new opportunities, while others lag behind. The path forward is clear: build IT around modularity, openness and intelligence. A composable, AI-driven MES is the blueprint for manufacturing excellence, enabling continuous adaptation and innovation.
42Q supports the transition to a modular, plug-and-play, AI-ready MES as the blueprint for modern manufacturing excellence. Leveraging our cloud-native MES platform with interoperable modules empowers manufacturers to modernize at their own pace while integrating advanced AI-driven insights. The result is a scalable, agile operation that drives continuous improvement in quality and efficiency – exactly what companies need.
Key Takeaways
- Modular MES frameworks allow plants to adapt quickly to new requirements.
- Cloud deployment shortens implementation and helps cut operational expenses.
- Unified data models streamline analytics and support AI-backed insights.
- Digital traceability reduces compliance overhead and prevents quality issues.
- Composable architecture fosters cost-effective scaling for sustained production gains.
FAQs
Composable manufacturing involves using modular, interoperable building blocks that work seamlessly within production processes. A composable MES breaks down functionality into flexible components, allowing you to upgrade or switch out features without overhauling the entire system.
A traditional MES often comes with rigid architectures and lengthy implementation cycles. A composable approach offers smaller, adaptable modules that deploy quickly, creating a path to faster returns and easier updates.
Cloud-based architectures simplify AI integration by offering open interfaces and standardized protocols. This structure helps you incorporate predictive analytics, machine learning, or robotics modules without large-scale redevelopment.
Yes, modular elements provide granular traceability and version control that align with regulatory mandates. You can quickly adjust or add new compliance features to meet emerging standards.
A subscription-based model can reduce upfront hardware costs and spread expenses predictably over time. The option to add or remove modules ensures you only pay for what your operation needs.