Understanding Composability in Manufacturing
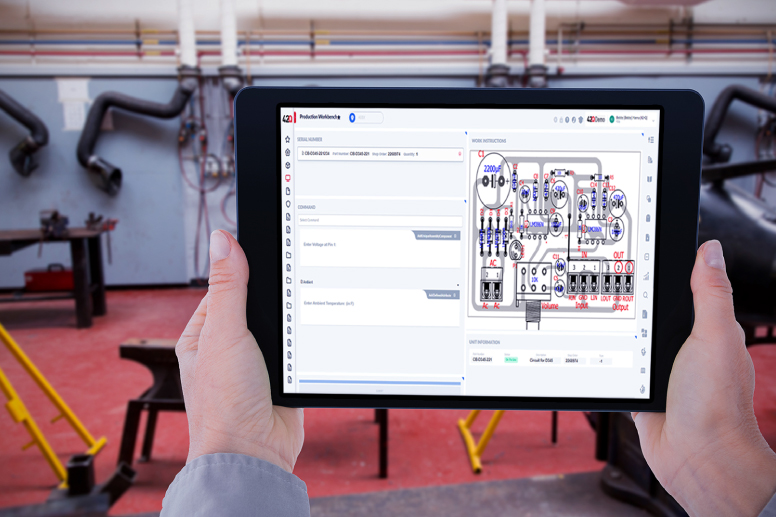
Understanding Composability in Manufacturing
Manufacturers must rethink traditional production models to meet shifting needs, integrate emerging technologies, and maintain efficiency.
Rigid, monolithic systems no longer provide the adaptability to optimize workflows and minimize disruptions. Composable manufacturing introduces a modular approach, allowing production lines to be reconfigured quickly without extensive downtime or costly overhauls. Manufacturers can increase agility, reduce operational risks, and scale production capacity by focusing on standardization, interoperability, and automation. Understanding how composable manufacturing works, its key benefits, and its practical applications provides valuable insight into its growing role in modern production.
What is Composability in Manufacturing?
Manufacturing composability refers to the ability to assemble, disassemble, and reconfigure manufacturing processes and systems based on modular, interoperable components. Unlike rigid, monolithic production systems, composable manufacturing equips manufacturers to create highly adaptable production settings that quickly adjust to shifting market needs, new product requirements, and developing supply chain conditions.
This approach relies on standardized, plug-and-play components that can be reconfigured with minimal downtime, allowing for greater agility and efficiency. Manufacturers using composable systems can respond to fluctuations in production volume, introduce new technologies seamlessly, and integrate automation solutions without overhauling existing infrastructure. The result is a more flexible, scalable, and cost-effective production model that enhances operational efficiency and reduces time to market.
The Evolution of Flexible Manufacturing Systems
Manufacturing has shifted from rigid, labor-intensive production models to adaptable, technology-driven systems that improve efficiency and scalability. The path toward composable manufacturing builds on key advancements in automation, digitalization, and modular system design. Each stage of this progression has introduced solutions to reduce waste, lower costs, and improve production flexibility.
- Manual Production Lines: Early manufacturing relied entirely on human labor, making production processes slow, costly, and prone to errors. Adjustments to production workflows required extensive retraining and manual retooling, leading to significant downtime and inefficiencies. Despite these challenges, manual systems allowed for high levels of customization, which was difficult to achieve with later automated methods.
- Introduction of Automated Assembly Systems: As industries sought ways to increase output and reduce labor costs, automated machinery became a standard feature of production lines. Mechanized conveyor belts, robotic arms, and programmable logic controllers (PLCs) allowed for higher efficiency and consistency. However, early automation systems were rigid, requiring costly modifications when introducing new products or production methods.
- Development of Flexible Manufacturing Systems (FMS): Recognizing the limitations of static automation, manufacturers introduced flexible manufacturing systems that allowed for faster adjustments. These systems incorporated robotics, computer-controlled machinery, and programmable automation to support multiple product variations on a single production line. Despite offering greater adaptability, FMS often required specialized expertise to configure and maintain, limiting adoption in smaller manufacturing operations.
- Advancements in Smart Manufacturing Technologies: The rise of data-driven production introduced smart sensors, cloud computing, and industrial IoT (IIoT) solutions that enhanced flexibility. Real-time analytics and predictive maintenance tools equip manufacturers to make informed decisions about process improvements, reducing downtime and improving overall efficiency. Despite these innovations, manufacturers faced integration challenges when connecting legacy systems with newer digital technologies.
- Adoption of Composable Manufacturing: The shift toward composable manufacturing builds on the strengths of earlier systems while addressing their shortcomings. Modular production components, software-defined automation, and AI-driven optimization allow manufacturers to reconfigure operations with minimal disruption. Unlike traditional automation, which often requires dedicated infrastructure, composable systems support plug-and-play adaptability, making production lines more scalable and cost-effective.
Manufacturers seeking to improve operational efficiency must consider how composability builds on past advancements while addressing the limitations of earlier manufacturing models. Implementing modular systems, digital tools, and flexible automation provides a structured approach to adapting production processes based on market shifts, supply chain variability, and emerging technologies.
Benefits of Composability in Manufacturing
Manufacturing composability allows companies to create highly adaptable production systems that improve efficiency, scalability, and cost control. Traditional manufacturing systems often require significant investments in infrastructure changes to accommodate new products, production methods, or automation technologies. Composable manufacturing eliminates these barriers by enabling manufacturers to reconfigure production lines and integrate new components with minimal disruption. This approach provides several operational advantages that help manufacturers meet shifting requirements while reducing unnecessary costs and downtime.
- Increased Agility in Production Processes: Traditional manufacturing setups are often complex to modify, requiring extensive planning and downtime when adjusting for new products or processes. Composable manufacturing eliminates these bottlenecks by allowing production lines to be reconfigured with modular equipment and software-defined automation. This makes it easier to accommodate shifts in product need, introduce new materials, or adjust workflows without overhauling existing systems.
- Lower Operational and Capital Costs: Replacing entire production lines or investing in new infrastructure can be costly and time-consuming. Composable manufacturing reduces the need for large-scale capital expenditures by allowing manufacturers to repurpose existing equipment and integrate new technologies without significant financial commitments. Lower maintenance costs and improved resource allocation further contribute to long-term cost savings.
- Scalability for Production Volume Adjustments: Manufacturers often need to adjust output based on supply chain conditions, seasonal need, or shifts in consumer preferences. Composable manufacturing allows for incremental scaling, increasing or decreasing production capacity without requiring an entirely new setup. This ensures that manufacturers can remain efficient while avoiding overproduction or supply shortages.
- Faster Integration of New Technologies: Emerging automation solutions, AI-driven analytics, and IoT monitoring systems provide significant advantages, but integrating these technologies into traditional manufacturing settings can be complex and expensive. Composable manufacturing systems use standardized interfaces that simplify adopting new technologies, allowing manufacturers to upgrade processes without costly or time-intensive retrofits.
- Improved Resilience Against Disruptions: Unplanned equipment failures, supply chain shortages, and shifting regulatory requirements can disrupt traditional production systems. Composability minimizes these risks by ensuring that production lines can be quickly reconfigured in response to unexpected challenges. Manufacturers can swap out components, adjust workflows, or reallocate resources to maintain operational continuity.
- Enhanced Product Customization Without Sacrificing Efficiency: Consumers and industries slowly require more personalized and specialized products, yet traditional mass production methods struggle to meet these expectations. Composable manufacturing equips high levels of customization by allowing manufacturers to quickly adapt production lines for different product variations, materials, or specifications without compromising efficiency or increasing costs.
Manufacturers looking to increase efficiency, reduce operational risks, and improve scalability can benefit from composable manufacturing’s modular and adaptable structure. This approach ensures that production systems remain flexible and cost-effective while supporting long-term innovation and operational stability.
Real-World Applications of Composable Manufacturing
Industries with complex production requirements and high variability in product specifications require manufacturing systems that can quickly adapt to new processes, materials, and regulations. Composable manufacturing provides the flexibility to integrate automation, customize production lines, and respond to shifting supply chain conditions. This approach has been widely adopted across industries that require high precision, regulatory compliance, and rapid production adjustments.
Automotive Manufacturing
Automakers must regularly adjust production lines to accommodate new models, alternative powertrains, and shifting consumer preferences. Composable manufacturing allows automotive plants to modify assembly lines with modular robotic systems and flexible tooling, making transitioning between internal combustion engine vehicles and electric vehicle (EV) production easier. Software-driven automation also allows manufacturers to adjust workflows without manual intervention, reducing downtime and improving production efficiency.
Medical Device and Pharmaceutical Production
Strict regulatory requirements in medical device and pharmaceutical manufacturing require high precision and traceability levels. Composable manufacturing allows these industries to reconfigure production lines to meet compliance standards, implement digital quality control systems, and integrate real-time monitoring solutions. This flexibility reduces the time and effort required to adjust for new regulatory updates while ensuring that products meet safety and efficacy standards.
Aerospace and Defense Manufacturing
Aerospace and defense manufacturers require production systems that support high-mix, low-volume production and mass production of standardized components. Composable manufacturing allows switching between custom-built aircraft parts and standardized military components without significant production delays. Digital twins and AI-driven simulations also play a key role in optimizing assembly processes, reducing errors, and minimizing material waste.
Semiconductor and Electronics Production
Semiconductor manufacturing requires highly controlled production conditions and frequent process updates to accommodate next-generation chip designs. Composable manufacturing supports modular cleanroom production systems, allowing manufacturers to reconfigure fabrication processes without shutting down entire facilities. Automation and AI-powered process optimization further enhance efficiency by identifying opportunities for reducing material waste and improving defect detection.
Heavy Machinery and Industrial Equipment Manufacturing
Manufacturers producing industrial equipment, mining machinery, and construction tools need flexible production systems for customization and scalability. Composable manufacturing supports standardized component integration, making it easier to produce different product configurations while maintaining high levels of efficiency. Modifying production lines for new equipment models without investing in entirely new infrastructure reduces costs and improves long-term production flexibility.
Industries adopting composable manufacturing benefit from reduced production downtime, improved cost control, and the ability to integrate advanced automation solutions. This approach ensures that manufacturing systems remain adaptable, scalable, and efficient without costly infrastructure overhauls.
Implementing Composability in Manufacturing
Manufacturers seeking composable manufacturing must focus on system interoperability, modular equipment design, and data-driven automation. A structured implementation approach ensures that production systems remain flexible while minimizing disruptions.
Modular Equipment and Standardized Interfaces
Manufacturing systems built with interchangeable components allow for easier reconfiguration when production requirements shift. Standardized machine interfaces ensure that equipment from different vendors can work, eliminating compatibility issues that often delay integration. Modular design also reduces the need for custom-built solutions, lowering costs and improving scalability.
Digital Twin Technology for Process Optimization
Digital twins provide virtual simulations of production workflows, allowing manufacturers to test new configurations before making physical adjustments. This technology improves control by identifying potential bottlenecks, optimizing resource allocation, and ensuring that production changes do not introduce inefficiencies. Manufacturers using digital twins can confidently implement process modifications, reducing trial-and-error disruptions.
AI-Driven Automation and Robotics Integration
Automation plays a critical role in composable manufacturing by allowing production lines to adapt to shifting requirements with minimal manual intervention. AI-powered robotics and process control systems adjust workflows based on real-time data, improving efficiency and reducing waste. Collaborative robots (cobots) further enhance flexibility by assisting with assembly tasks that require human-machine interaction.
Data Standardization and Industrial IoT Connectivity
Seamless communication between production systems ensures that composable manufacturing functions as a unified operation. Standardized communication protocols such as OPC UA and MQTT allow data to flow securely between machines, sensors, and cloud-based analytics platforms. Real-time monitoring and predictive maintenance systems help manufacturers prevent equipment failures, reducing downtime and improving overall equipment effectiveness.
Supply Chain Integration and Vendor Collaboration
Manufacturers implementing composable systems must work closely with suppliers that support modular component compatibility. Selecting technology providers prioritizing interoperability ensures that new equipment and software solutions integrate smoothly. This approach minimizes disruptions when introducing new materials, automation systems, or production line modifications.
A structured approach to implementing composable manufacturing allows companies to optimize efficiency, integrate emerging technologies, and adjust production processes without significant disruptions. This adaptability ensures manufacturers meet shifting production requirements while improving cost control and resource utilization.
Future of Composability in Manufacturing
Manufacturers are expected to increase their adoption of composable manufacturing as the industry needs to shift toward greater flexibility, automation, and sustainability. Modular production systems will play a key role in meeting these needs while minimizing operational disruptions.
Artificial intelligence and machine learning will refine composable manufacturing by automating real-time process adjustments and predictive maintenance. Advanced analytics will equip manufacturers to optimize production schedules, reduce waste, and improve overall equipment effectiveness (OEE). Cloud-based platforms will also enhance system interoperability, seamlessly integrating new technologies without costly infrastructure overhauls.
Sustainability will remain a priority, with composable manufacturing supporting energy-efficient production methods and waste reduction. The ability to reconfigure production lines based on material availability and regulatory requirements will help manufacturers lower costs while meeting goals.
Adopting composable manufacturing will become an industry standard as companies seek to improve agility, reduce operational risks, and integrate advanced technologies into their production workflows.
Manufacturers worldwide embrace cloud-based solutions to achieve efficiency, precision, and scalability. At 42Q, we combine decades of manufacturing expertise with cutting-edge technology to deliver innovative, connected manufacturing. Our flexible, cloud-native MES platform enhances visibility, streamlines operations, and accelerates digital transformation. Discover how our solutions can empower your factory to achieve its full potential.
Key Takeaways
- Composable manufacturing enhances production flexibility by enabling quick system modifications without requiring significant downtime or reconfiguration.
- Modular components and standardized interfaces simplify integration, allowing manufacturers to incorporate automation, robotics, and AI-driven analytics efficiently.
- Industries such as automotive, aerospace, and semiconductor manufacturing benefit significantly from composable manufacturing due to its scalability and adaptability.
- Data-driven automation and digital twins improve production efficiency, allowing manufacturers to simulate, test, and optimize workflow adjustments in real time.
- Cost savings result from reduced infrastructure investment, lower maintenance requirements, and the ability to adapt existing production systems without complete replacements.
FAQs
Manufacturing composability refers to the ability to configure, adjust, and optimize production systems using modular, interoperable components. This approach allows manufacturers to reconfigure workflows, integrate automation, and adapt to supply chain variability with minimal disruption. The result is a more efficient, scalable, and cost-effective production model.
Composable manufacturing improves efficiency by allowing manufacturers to quickly adjust production lines without costly retooling. Modular systems reduce downtime, optimize resource allocation, and integrate seamlessly with automation and AI-driven monitoring. This adaptability ensures continuous production flow, even during disruptions or product design changes.
Industries requiring high precision, scalability, and customization benefit the most from composable manufacturing. Automotive, aerospace, medical device, semiconductor, and industrial equipment manufacturers use this approach to optimize production while meeting strict regulatory and quality requirements. The ability to modify workflows without major overhauls makes it ideal for industries with frequently shifting needs.
Composable manufacturing supports automation using standardized interfaces that integrate seamlessly with robotic systems and AI-driven process controls. This approach automated adjustments in workflow configuration, material handling, and real-time monitoring. Manufacturers can implement collaborative robots (cobots) and AI-driven analytics without disrupting operations.
The modular nature of composable manufacturing reduces capital expenditures by eliminating the need for large-scale infrastructure changes. Manufacturers can repurpose existing equipment, integrate new technologies incrementally, and reduce waste associated with inefficiencies. Lower maintenance costs and improved adaptability contribute to long-term financial savings.