Streamlining Manufacturing with MES Software in 2025
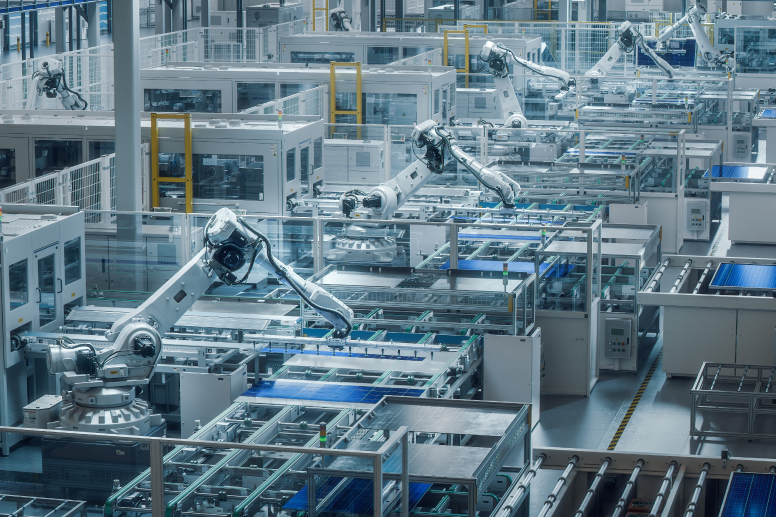
Streamlining Manufacturing with MES Software in 2025
"MES software bridges the gap between enterprise-level planning systems and the equipment and processes used in production, ensuring manufacturers can execute their schedules effectively."
MES software is redefining how manufacturers manage and optimize their operations, offering the tools needed to connect production processes with enterprise systems seamlessly.
With its ability to provide real-time data and ensure smooth collaboration between the shop floor and broader business goals, MES software has become essential for maintaining efficiency, enhancing quality control, and meeting the challenges of modern manufacturing environments.
As manufacturers aim to reduce downtime, maintain compliance, and adapt to shifting demands, MES manufacturing software delivers the structure and insights needed to keep operations running at peak performance. Understanding what MES software is and how it works is key to unlocking its potential to streamline workflows, improve traceability, and enable smarter decision-making.
Understanding MES Software in Manufacturing
Manufacturing Execution System (MES) software is the backbone of modern manufacturing operations, acting as the central hub for monitoring, managing, and optimizing production processes in real time. Its primary purpose is to connect, track, and analyze the critical activities occurring on the shop floor, providing manufacturers with the visibility and control needed to enhance efficiency and productivity.
At its essence, MES software bridges the gap between enterprise-level planning systems, like Enterprise Resource Planning (ERP), and the equipment and processes used in production. It ensures manufacturers can execute their production schedules effectively by managing resources, enforcing quality standards, and providing actionable insights through data analytics.
MES manufacturing software is pivotal in reducing errors, improving quality, and minimizing downtime. It enables manufacturers to adapt quickly to changes in demand, maintain compliance with industry regulations, and achieve greater traceability of products and processes.
Why MES Software Implementation Drives Scalability
"MES software provides manufacturers with the tools to scale efficiently and sustainably, ensuring they can adapt to market demands without compromising on quality or productivity."
Scaling operations in manufacturing requires more than just increasing production capacity—it demands a strategic approach to maintaining efficiency, quality, and resource optimization. MES software serves as a vital tool for manufacturers aiming to achieve scalability without compromising operational performance. Through seamless integration with shop floor systems and enterprise planning tools, MES software enables businesses to streamline processes, reduce inefficiencies, and respond effectively to changing production needs.
The ability of MES manufacturing software to enhance flexibility, improve resource allocation, and support informed decision-making makes it indispensable for manufacturers navigating growth. Its capabilities provide a strong foundation for expanding operations while maintaining the agility required to adapt to market demands and emerging challenges. These benefits position MES software as an essential component of scalable, future-ready manufacturing systems.
Enhancing Flexibility in Production
Flexibility is vital for manufacturers adapting to fluctuating demand or introducing new products. MES software provides this adaptability by creating a dynamic framework that allows manufacturers to modify workflows, adjust production schedules, and allocate resources in real-time. Its ability to integrate with various equipment and systems ensures that changes can be implemented seamlessly without disrupting ongoing operations.
This level of responsiveness empowers manufacturers to scale production efficiently, whether expanding capacity to meet demand spikes or transitioning to new product lines. MES software eliminates inefficiencies and bottlenecks by providing a clear view of operations, ensuring a smooth scaling process.
Optimizing Resource Allocation
Effective resource management is a cornerstone of scalability. MES software tracks and monitors resource availability, usage, and performance, including equipment, materials, and labor. With these insights, manufacturers can allocate resources more effectively, ensuring maximum output with minimal waste.
This optimization prevents underutilization or overuse of critical assets, reducing downtime and extending the lifespan of equipment. For manufacturers scaling operations, MES software ensures that resources are aligned with business goals, resulting in cost-efficient growth.
Supporting Better Decision-Making
Data is the foundation of informed decision-making, and MES manufacturing software excels at providing actionable insights. Its ability to collect, analyze, and present data in real time gives manufacturers the information to make proactive adjustments and forecast future needs.
This capability becomes especially important during periods of growth, where small inefficiencies can compound and disrupt operations. MES software mitigates these risks by offering predictive insights, enabling manufacturers to anticipate challenges and implement solutions before issues arise.
Effective scalability in manufacturing hinges on the ability to balance growth with operational excellence. MES software equips manufacturers with the insights, tools, and flexibility necessary to expand operations seamlessly and sustainably. Whether it’s optimizing resource utilization, ensuring smooth production adjustments, or enabling predictive decision-making, MES software supports the critical processes that drive scalable success.
For manufacturers focused on meeting market demands while maintaining quality and efficiency, MES software is a proven solution. It fosters sustainable growth, minimizes inefficiencies. Investing in MES software paves the way for long-term operational resilience and scalability.
Identifying Business Potential with MES Software
MES software is a transformative tool for untapped business potential in manufacturing. Its robust capabilities give manufacturers the insights and control needed to improve operational efficiency, reduce costs, and enhance product quality. Beyond streamlining day-to-day operations, MES software enables manufacturers to identify and seize new growth opportunities.
One significant area of potential lies in improved production visibility. MES manufacturing software delivers real-time data on every aspect of the production process, highlighting inefficiencies and bottlenecks that might otherwise go unnoticed. With this level of transparency, manufacturers can make precise adjustments that lead to immediate performance gains.
Another critical advantage of MES software is its ability to support compliance and traceability efforts. Many industries, including medical devices and automotive, face stringent regulatory requirements. MES software simplifies compliance by tracking every step of production and maintaining detailed records, giving businesses an industry edge in regulated markets. Lastly, MES software equips manufacturers with the tools to embrace innovation. From implementing innovative manufacturing practices to integrating advanced automation, the platform supports continuous improvement and fosters a culture of innovation that drives long-term business growth.
Key Steps for Seamless MES Software Deployment
Deploying MES software successfully requires careful planning, clear communication, and a focus on minimizing disruptions while maximizing benefits. A well-executed implementation ensures manufacturers can align production goals with broader business objectives while addressing unique operational challenges. This process calls for a structured approach that anticipates potential obstacles and builds a foundation for sustained operational improvements. Effective deployment not only optimizes workflows but also enhances overall productivity and compliance.
- Define Clear Objectives and Prioritize Goals: Set measurable objectives to guide the implementation process. Focus on goals such as improving efficiency, reducing production downtime, or achieving faster order fulfillment. Clear priorities help ensure the deployment delivers meaningful results for the business.
- Conduct a Comprehensive Needs Assessment: Analyze workflows, equipment compatibility, and data requirements to identify gaps and opportunities for integration. Gathering input from production and IT teams helps ensure the MES software addresses specific manufacturing challenges effectively.
- Select the Right MES Software Vendor: Partner with a vendor capable of tailoring the software to your needs. Key considerations include scalability, proven integration with ERP systems , and robust support services. A reliable vendor ensures a smoother implementation and ongoing success.
- Develop a Phased Deployment Plan: Roll out the MES software in stages to avoid overwhelming operations. Start with a pilot program in one production area to gather feedback, test functionality, and refine processes before scaling to additional locations or departments.
- Invest in Comprehensive User Training: Equip employees with the skills they need to operate the MES software effectively. Training should include hands-on sessions, clear documentation, and ongoing support to build confidence and foster adoption across teams.
- Monitor and Optimize Post-Deployment: Continuously evaluate the system’s performance after implementation. Use collected insights to refine workflows, address inefficiencies, and ensure the software continues to meet operational needs.
A successful MES software deployment enables manufacturers to achieve greater efficiency, streamline workflows, and minimize risks during implementation. Taking the time to prepare thoroughly, engage stakeholders, and monitor performance ensures the software aligns with operational goals and delivers lasting benefits. With the right approach, businesses can establish a strong foundation for future growth and improved productivity.
Overcoming Implementation Challenges
Implementing MES software can be a complex process that presents several challenges. However, understanding these potential obstacles and addressing them proactively can ensure a smoother transition and successful outcomes.
One common challenge is resistance to change among employees. Introducing new systems often disrupts familiar workflows, leading to hesitation or pushback from staff. Engaging employees early, providing comprehensive training, and demonstrating the tangible benefits of MES software can foster acceptance and encourage adoption. Another challenge is ensuring seamless integration with existing systems, such as ERP platforms or legacy manufacturing equipment. MES manufacturing software must work harmoniously within the current infrastructure to deliver value. Conducting a detailed compatibility assessment and collaborating with an experienced vendor can mitigate these risks.
Data management complexity also poses a hurdle. MES software generates and relies on vast amounts of real-time data, which must be accurately collected, analyzed, and stored. Manufacturers must invest in reliable IT infrastructure and data security measures to ensure the system functions efficiently and protects sensitive information. Scalability concerns may arise if the MES software is not designed to grow alongside the business. Choosing a flexible solution that can adapt to expanding operations, new products, or changing market demands is critical for long-term success.
While challenges in MES software implementation can seem daunting, addressing them with a proactive, structured approach ensures they are minimized, unlocking the full potential of this transformative technology.
Strategies to Maximize ROI with MES Software
Maximizing the return on investment (ROI) from MES software requires a strategic approach that aligns the system’s capabilities with organizational goals. MES software empowers manufacturers to optimize operations, enhance productivity, and support decisions with data that reduce costs and improve efficiency. Achieving measurable ROI with MES software depends on implementing processes that capitalize on its full potential while addressing specific challenges faced on the shop floor.
Each of these strategies focuses on leveraging MES software to drive sustainable growth, enhance operational efficiency, and ensure profitability. Whether addressing resource utilization, minimizing downtime, or enhancing employee productivity, these methods are essential for manufacturers aiming to remain innovative and adaptable.
Streamline Production Processes
One of the most significant benefits of MES software is its ability to enhance efficiency on the shop floor. The system identifies inefficiencies by tracking real-time production data, pinpointing bottlenecks, and highlighting underperforming equipment. Manufacturers can optimize workflows using this data to restructure tasks, balance workloads, and improve team coordination.
MES manufacturing software enables real-time communication between machines and operators, ensuring swift responses to disruptions or anomalies. This approach reduces downtime and accelerates production cycles, leading to higher throughput and cost savings without requiring additional resources.
Strengthen Quality Assurance
MES software enhances quality control by monitoring production at every stage and enforcing quality standards. Automated checks and real-time alerts identify defects or deviations early, allowing immediate corrective action. With built-in tracking features, manufacturers can maintain consistent product quality while meeting regulatory requirements.
The software also records all quality-related data, simplifying audits and compliance reporting. Lower defect rates and improved traceability reduce waste and foster customer confidence, creating long-term value for the business.
Drive Predictive Maintenance
Unplanned equipment downtime can disrupt production and inflate costs. MES software provides predictive maintenance capabilities by monitoring machine performance metrics such as vibration, temperature, and cycle counts. These insights help manufacturers schedule maintenance activities proactively, preventing unexpected breakdowns and extending equipment life.
A predictive maintenance strategy also reduces the frequency of costly emergency repairs and minimizes disruptions to production schedules. This approach ensures that critical resources remain available when needed, supporting operational continuity and long-term profitability.
Optimize Resource Utilization
MES software offers visibility into resource usage, including materials, labor, and equipment. This visibility enables manufacturers to allocate resources more effectively and reduce waste. For example, the system can track inventory levels in real-time to prevent overstocking or understocking, optimizing raw material usage.
Efficient resource allocation reduces costs associated with excess inventory, labor inefficiencies, and unnecessary overtime. It also allows manufacturers to scale operations sustainably, improving ROI as production demands grow.
Leverage Data for Strategic Decision-Making
MES software generates detailed, actionable data that empowers manufacturers to make informed decisions at every level of the organization. Historical data can be analyzed to identify production trends, forecast demand, and develop long-term strategies. Real-time analytics enable quick adjustments to schedules, inventory, or staffing, reducing the risk of inefficiencies.
Additionally, manufacturers can use MES data to evaluate the success of new initiatives or investments, ensuring continuous improvement. This capability fosters a culture of accountability, driving sustained growth and maximizing ROI.
Enable Scalable Growth
Scalability is essential for manufacturers aiming to expand operations or enter new markets. MES software supports this growth by offering flexible configuration options that adapt to changing production requirements. Features like multi-plant visibility and cloud-based accessibility make integrating new facilities, products, or equipment into existing workflows easier. Scaling with MES software ensures manufacturers can meet high demand without sacrificing efficiency or quality, providing a clear path to higher profitability and ROI.
Enhance Employee Productivity
MES software simplifies tasks and empowers employees with real-time insights, allowing them to work more effectively. User-friendly dashboards and automation of repetitive processes reduce administrative burdens, enabling workers to focus on high-value activities.
Well-trained employees with the right tools can identify and resolve issues faster, improving overall productivity. Increased employee engagement and efficiency contribute directly to better ROI and a more competitive operation.
Achieving measurable ROI with MES software requires a clear focus on strategies that integrate its capabilities into everyday operations. By improving efficiency, reducing costs, and enabling smarter decision-making, MES software becomes a powerful tool for driving sustained business success. Manufacturers that prioritize strategic implementation and optimization of MES software unlock its potential to deliver both immediate benefits and long-term profitability. With the right approach, MES software not only enhances current performance but also builds a foundation for future scalability and growth.
Future-Proofing Manufacturing with MES Software
Adapting to change and embracing innovation are crucial for manufacturers. MES software creates a strong foundation for operational resilience, enabling seamless integration of emerging technologies, optimized workflows, and improved scalability. Manufacturers can address industry challenges, streamline production processes, and maintain efficiency while preparing for future growth.
MES software empowers manufacturers to anticipate potential obstacles, improve decision-making, and leverage advanced solutions to enhance productivity. It provides the tools necessary to strengthen operations, support compliance, and deliver measurable improvements, ensuring businesses stay ahead of the curve.
- Adopt Advanced Analytics and AI: Leverage the data capabilities of MES software to integrate artificial intelligence and machine learning technologies. These tools enable predictive analytics, process optimization, and enhanced decision-making, ensuring manufacturers can stay ahead of trends and anticipate operational needs.
- Enable IoT Integration: MES software supports seamless integration with Internet of Things (IoT) devices, creating connected manufacturing environments. IoT-enabled sensors and equipment provide real-time data that enhances efficiency, reduces waste, and supports more intelligent automation.
- Enhance Agility with Cloud-Based Solutions: Cloud-based MES manufacturing software allows manufacturers to scale quickly, update processes remotely, and access critical data from anywhere. This flexibility ensures businesses can respond effectively to changes in production demands or disruptions.
- Improve Compliance and Traceability: MES software simplifies adherence to regulatory requirements through built-in compliance tracking and detailed documentation. Enhanced traceability features improve product recalls and auditing processes, reducing risk and building customer trust.
- Implement Digital Twin Technology: MES software can integrate with digital twin models to simulate production scenarios and test process changes virtually. This capability allows manufacturers to refine workflows and improve outcomes without disrupting operations.
- Promote Workforce Empowerment: Use MES software to create user-friendly dashboards, automate repetitive tasks, and provide workers with actionable insights. Empowered employees are more productive, adaptable, and engaged, which supports long-term operational success.
MES software is a strategic investment for manufacturers seeking to align operations with industry demands. Advanced features like analytics, IoT connectivity, and workforce automation ensure smoother processes, stronger compliance, and greater adaptability. Manufacturers that embrace these tools position themselves to overcome challenges, enhance operational excellence, and seize opportunities for long-term success. MES software transforms current operations into a platform for innovation and sustainable growth, creating a resilient, future-ready enterprise.
Manufacturers worldwide embrace cloud-based solutions to achieve efficiency, precision, and scalability. At 42Q, we combine decades of manufacturing expertise with cutting-edge technology to deliver smart, connected manufacturing. Our flexible, cloud-native MES platform enhances visibility, streamlines operations, and accelerates digital transformation. Discover how our solutions can empower your factory to achieve its full potential.
Key Takeaways
- MES software connects enterprise planning systems with shop floor operations, enabling real-time monitoring and control of production processes.
- Scalability is enhanced with MES software through resource optimization, seamless integration, and data-driven decision-making.
- Predictive maintenance features reduce downtime and prolong equipment life, directly impacting operational efficiency and ROI.
- MES manufacturing software simplifies compliance and traceability, ensuring manufacturers meet stringent industry standards.
- Cloud-based MES solutions provide flexibility, faster implementation, and multi-plant visibility, supporting global manufacturing operations.
FAQ's
MES software monitors and manages real-time production processes on the shop floor. It tracks resources, enforces quality standards, and provides actionable insights, ensuring manufacturers can improve efficiency, reduce waste, and maintain compliance.
MES software supports scalability by integrating existing systems, enabling real-time adjustments, and optimizing resource utilization. These features allow manufacturers to expand production capacity, adapt to new products, and meet increased demand without compromising quality.
MES manufacturing software offers real-time production monitoring, predictive maintenance, quality control enforcement, compliance tracking, and data analytics. These features ensure manufacturers can streamline operations and make informed decisions.
MES software tracks production steps and records data for each process, making tracing products and meeting industry regulations easy. This capability simplifies audits, enhances transparency, and supports product recalls when necessary.
Cloud-based MES software offers advantages like faster deployment, scalability, and remote accessibility. These benefits allow manufacturers to adapt quickly to changes, reduce IT infrastructure costs, and achieve better visibility across multiple plants.
How AI and Machine Learning are Shaping Production Lines in 2025
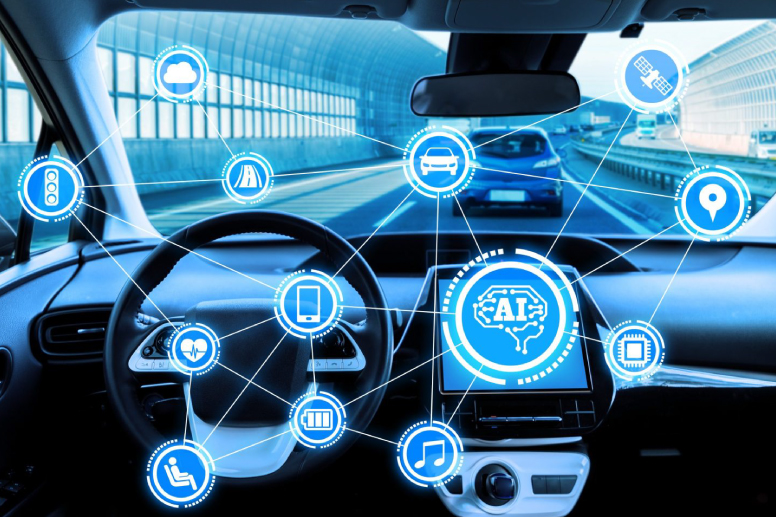
How AI and Machine Learning are Shaping Production Lines in 2025
AI and machine learning are reshaping production systems, offering solutions beyond traditional automation to create intelligent, adaptive manufacturing environments.
These technologies bring unparalleled efficiency, precision, and agility to production lines, allowing manufacturers to remain aggressive in a market that demands rapid adaptability and flawless execution. With tools like predictive maintenance, real-time quality control, and data-driven decision-making, AI empowers manufacturers to reduce costs, minimize waste, and deliver scale-quality products.
What is AI in Production?
Artificial intelligence (AI) in production refers to the application of intelligent systems and algorithms designed to optimize manufacturing processes, improve decision-making, and enhance operational efficiency. These technologies leverage advanced capabilities such as machine learning, predictive analytics, and automation to address key challenges in manufacturing environments. AI enables manufacturers to identify patterns, predict outcomes, and respond proactively to issues, resulting in increased precision, minimized waste, and faster adaptation to shifting market demands.
Unlike traditional automation, AI in production introduces systems capable of learning from historical data, adapting to new scenarios, and making proactive adjustments in real time. This means manufacturers can predict customer demand, detect and prevent equipment failures, and fine-tune inventory management with unprecedented accuracy. As a result, AI empowers businesses to maintain consistent quality, reduce costs, and enhance the flexibility of production lines.
The integration of AI and machine learning in production lines has become essential for manufacturers aiming to remain agile. From improving forecasting to optimizing maintenance schedules, AI-based tools deliver actionable insights and measurable results. These advancements mark a significant evolution in how manufacturing is managed, ensuring operations stay efficient and responsive.
Benefits of Implementing AI in Production
“AI-driven systems analyze vast amounts of production data to identify inefficiencies and improve workflows, maximizing productivity and reducing errors.”
Integrating artificial intelligence into production systems delivers significant advantages for manufacturers seeking to enhance efficiency, maintain consistent quality, and reduce operational costs. AI transforms traditional manufacturing by providing actionable insights, improving decision-making, and automating repetitive tasks. These capabilities enable manufacturers to meet customer demands, optimize resource allocation.
AI systems are particularly effective in addressing inefficiencies, preventing downtime, and scaling operations without sacrificing quality. Below are the most impactful benefits of AI in production, showcasing how this technology is shaping the future of manufacturing.
- Enhanced Process Optimization: AI systems analyze vast production data to detect inefficiencies, minimize errors, and improve productivity. Advanced algorithms dynamically adjust workflows, reduce cycle times, and optimize resource utilization, resulting in streamlined operations.
- Improved Quality Control: AI-powered tools such as computer vision and predictive analytics monitor production processes and identify defects early. This ensures consistent quality, reduces waste, and minimizes rework, enhancing customer satisfaction and strengthening product reliability.
- Predictive Maintenance Capabilities: AI leverages equipment performance data to anticipate potential failures before they occur. This proactive maintenance approach minimizes costly downtime, extends machinery lifespan, and reduces repair expenses, allowing teams to focus on strategic priorities.
- Lower Operational Costs: Automating repetitive and labor-intensive tasks reduces reliance on manual labor, enabling manufacturers to allocate human resources to higher-value activities. AI also improves energy efficiency and materials usage, leading to significant cost savings across the operation.
- Faster Time-to-Market: AI systems accelerate production agility by adapting to fluctuating market demands and streamlining design and testing processes. Manufacturers can bring new products to market more efficiently while maintaining consistent quality and delivery standards.
- Sustainability Improvements: AI supports resource optimization by reducing waste and energy consumption. These enhancements promote environmentally sustainable manufacturing practices while meeting growing consumer and regulatory expectations.
AI production tools change traditional manufacturing operations into intelligent, agile systems that respond to challenges. From improving efficiency and reducing costs to delivering exceptional product quality, the benefits of AI integration create lasting value and scalability for manufacturers. These tools help align production capabilities with long-term business objectives, driving sustainable growth and market leadership.
Understanding Machine Learning in Production
“Machine learning algorithms in production identify patterns, predict outcomes, and optimize operations in real-time, allowing smarter manufacturing processes.”
Machine learning in production involves using algorithms and data-driven models to improve efficiency and accuracy across manufacturing processes. Unlike traditional programming, machine learning allows systems to learn from historical data and improve their performance over time without requiring explicit instructions. This ability makes it a valuable tool for tackling complex challenges in production environments.
Machine learning algorithms in production are used to identify patterns, predict outcomes, and optimize operations in real time. For instance, supervised learning models can classify defective products by analyzing size, shape, or colour features. In contrast, unsupervised learning models can detect anomalies in equipment performance that indicate potential failures. Reinforcement learning, another branch of machine learning, can refine robotic processes through trial-and-error simulations, allowing machines to continuously adapt and improve their tasks.
Integrating machine learning into production gives manufacturers predictive maintenance, request forecasting, and process optimization capabilities. These technologies allow production systems to operate more efficiently, reduce waste, and respond quickly to shifts in market requests. The adaptability of machine learning ensures that manufacturers can stay ahead in an environment where precision and speed are critical for success.
6 Steps to Deploying Machine Learning Models in Production
Deploying machine learning models in production transforms data insights into actionable results, allowing businesses to optimize processes and improve decision-making. A successful deployment strategy ensures these models operate seamlessly, providing real-time predictions and long-term scalability. Machine learning models can drive innovation, reduce inefficiencies, and support better resource allocation when integrated effectively into production systems.
Every stage in the deployment process is critical to achieving reliable, efficient, and impactful results. With careful attention to data preparation, testing, and system integration, machine learning models can meet operational needs while adapting to future demands in manufacturing and other industries.
1. Data Preparation and Preprocessing
High-quality data is the foundation of any successful machine-learning model. This step involves collecting, cleaning, and preprocessing data to ensure it is relevant and consistent. Data preprocessing includes removing duplicates, handling missing values, and standardizing formats. Properly prepared data minimizes errors and enhances model accuracy, allowing robust predictions.
2. Model Development and Training
After data preparation, the next step is developing and training the machine learning model. This process involves selecting the right algorithms based on the specific use case, such as regression, classification, or clustering. The model is trained using historical data, learning patterns and relationships to make predictions or decisions. Training requires iterative adjustments to parameters to optimize model performance.
3. Model Validation and Testing
Validation and testing ensure the model performs accurately in scenarios. This step involves evaluating the model on a separate dataset not used during training, measuring accuracy, precision, and recall metrics. Robust testing helps identify potential weaknesses, ensuring the model is reliable and meets the required performance standards before deployment.
4. Integration into Production Systems
Once validated, the model is integrated into the production environment. This involves embedding the model into software systems, such as Manufacturing Execution Systems or enterprise platforms, where it can process live data. Integration also includes developing APIs or pipelines facilitating seamless communication between the model and existing systems.
5. Monitoring and Maintenance
Continuous monitoring ensures the model remains accurate and effective over time. Monitoring involves tracking performance metrics, identifying data drift, and addressing changes in production environments that might affect outcomes. Regular updates and retraining with new data keep the model relevant and aligned with operational needs.
6. Scalability and Optimization
Scaling the machine learning model to handle increased data volume or expanded operations is essential for long-term success. Optimization involves fine-tuning the model and infrastructure to ensure it operates efficiently as production requirements grow. Tools such as cloud-based platforms can support scalability while maintaining cost efficiency.
Machine learning deployment enables businesses to unlock the full potential of their data, enhancing production efficiency and enabling smarter decision-making. Clear processes for training, integration, and monitoring ensure models remain relevant and effective over time. These efforts help businesses achieve operational success and position themselves for continued growth in competitive manufacturing environments.
Challenges to Implementing AI in Production
Introducing artificial intelligence into production environments offers transformative potential but is not without its challenges. Manufacturers must address various obstacles to ensure AI systems integrate seamlessly, operate effectively, and deliver measurable benefits. These challenges often stem from data quality issues, resource limitations, and organizational resistance, requiring a well-structured approach to overcome.
Effectively navigating these barriers ensures AI-driven tools can improve efficiency, enhance decision-making, and contribute to long-term operational success.
- Data Quality and Availability: Poor-quality or incomplete historical data can undermine the accuracy of AI models during training and deployment. Inconsistent datasets limit the effectiveness of predictive tools, making high-quality data preparation essential for success.
- Integration with Existing Systems: Many manufacturers rely on legacy systems that are incompatible with AI technologies. Bridging this gap often requires substantial investment in infrastructure upgrades and time to establish seamless integration with modern AI tools.
- High Implementation Costs: While AI can reduce costs over time, the initial expenses associated with acquiring new technologies, hiring skilled personnel, and upgrading systems can be significant, particularly for smaller manufacturers.
- Workforce Resistance to Change: Employees may be hesitant to adopt AI-driven tools due to concerns about job displacement or unfamiliarity with new technologies. Resistance can hinder adoption and reduce the effectiveness of AI initiatives.
- Scalability Issues: Scaling AI tools to larger production lines or multi-site facilities demands robust infrastructure and clearly defined processes. Without careful planning, scaling efforts can create inefficiencies and resource constraints.
- Cybersecurity Risks: AI systems often rely on connected networks, making them vulnerable to data breaches and cyberattacks. Protecting production systems requires secure data handling, intellectual property safeguards, and continuous monitoring for threats.
Overcoming these challenges is essential for manufacturers aiming to realize the full potential of artificial intelligence. Addressing data quality, system integration, workforce readiness, and security concerns requires strategic planning and stakeholder collaboration. With the right approach, manufacturers can mitigate these risks while achieving the transformative benefits AI offers, including enhanced efficiency, cost savings, and operational scalability.
Measuring ROI of AI in Production
Evaluating the return on investment (ROI) of AI in production involves analyzing its contributions to efficiency, cost savings, and operational scalability. Metrics such as production throughput, defect rates, downtime reduction, and resource utilization highlight the measurable benefits AI delivers. Predictive maintenance reduces equipment downtime by identifying potential failures early, leading to cost savings and improved productivity. AI also enhances profitability over time through better resource allocation, lower energy consumption, and optimized inventory management, ensuring manufacturers can adapt to shifting demands effectively.
Qualitative benefits, such as improved product quality, faster time-to-market, and higher customer satisfaction, also play a critical role in ROI assessment. These factors strengthen brand loyalty and support long-term growth, even when they do not produce immediate financial returns. Combining both tangible and intangible results helps manufacturers fully understand AI’s value, empowering them to expand its role strategically and achieve sustained operational success.
Manufacturers worldwide embrace AI-driven solutions to enhance efficiency, precision, and scalability. At 42Q, we combine decades of manufacturing expertise with innovative cloud-based technology to deliver smart, connected manufacturing. Our flexible, cloud-native MES platform enhances visibility, streamlines operations, and accelerates digital congestion. Discover how our solutions can empower your factory to achieve its full potential.
Key Takeaways
- AI in production changes manufacturing processes through real-time optimization, predictive maintenance, and quality control.
- Machine learning adapts to production challenges using data-driven models that improve accuracy and efficiency over time.
- Implementing AI requires addressing data quality, system integration, and cybersecurity risks.
- Measuring ROI involves tracking quantitative metrics like defect rates and downtime reduction alongside qualitative benefits like customer satisfaction.
- Scalable and adaptable AI systems help manufacturers future-proof operations and respond to market requests.
FAQ's
AI in production refers to applying intelligent systems and algorithms to manufacturing processes. These technologies analyze data, identify patterns, and automate decision-making, helping manufacturers improve efficiency, optimize workflows, and reduce errors in real-time.
Machine learning improves production systems by allowing predictive maintenance, quality control, and request forecasting. It uses historical and real-time data to identify inefficiencies, detect anomalies, and adapt to conditions, making manufacturing operations more innovative and agile.
Industries such as automotive, medical devices, consumer electronics, and aerospace benefit significantly from AI production. These sectors rely on precision, scalability, and efficiency, all enhanced by AI-driven tools and processes.
The initial cost of deploying machine learning models in production can be substantial, covering technology acquisition, skilled personnel, and system upgrades. However, the long-term savings from optimized workflows, reduced downtime, and improved product quality often outweigh these upfront expenses.
Metrics like production throughput, defect rates, equipment downtime, and energy consumption are commonly used to measure AI’s impact. These indicators clearly show how AI contributes to cost savings, efficiency improvements, and operational scalability.
7 Differences Between MES vs SCADA
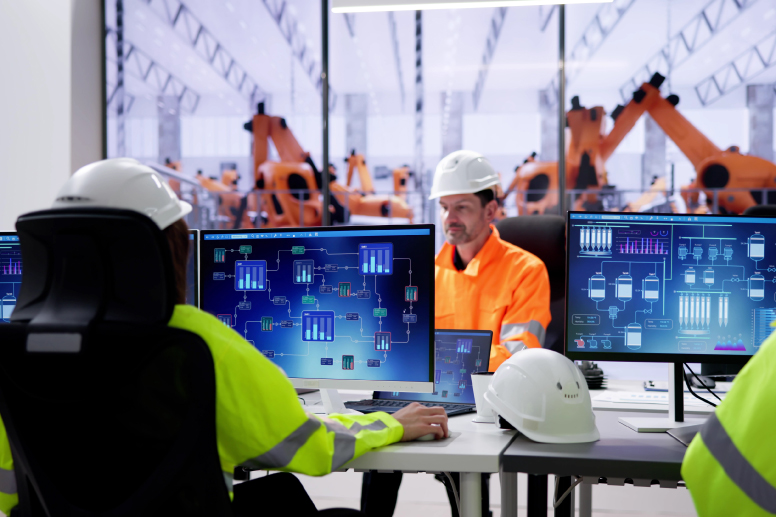
7 Differences Between MES vs SCADA
Manufacturers seeking to optimize operations and achieve sustainable growth face the challenge of selecting the right systems to manage production.
MES and SCADA, two essential manufacturing solutions, serve distinct but complementary purposes in ensuring efficiency and scalability. MES focuses on long-term optimization of the production lifecycle, while SCADA provides real-time monitoring and control of equipment. They enable manufacturers to meet modern demands with precision, agility, and strategic alignment.
What is an MES System?
"MES manages the entire production lifecycle, ensuring efficiency from planning to finished goods."
A Manufacturing Execution System (MES) is a software platform designed to monitor, control, and optimize the entire production lifecycle in manufacturing operations. Its primary function is to provide real-time insights and streamline processes from when raw materials are introduced into production to the delivery of finished products. MES bridges the gap between enterprise-level systems, such as Enterprise Resource Planning (ERP), and the operational level of the factory floor.
MES excels at resource allocation, production scheduling, quality management, and performance tracking. It transforms raw operational data into actionable insights, empowering managers to make strategic decisions that enhance productivity, reduce waste, and improve overall efficiency. MES is critical in enabling scalable and efficient manufacturing operations by offering end-to-end visibility and historical analysis.
What is a SCADA System?
A Supervisory Control and Data Acquisition (SCADA) system is designed to monitor and control industrial processes in real-time. It operates at the equipment and process level, helping operators to supervise machinery, sensors, and devices while ensuring seamless functionality. SCADA systems are widely used in manufacturing, energy, and utilities industries to oversee operations and respond to equipment or system changes instantly.
The system collects data from sensors and programmable logic controllers (PLCs) on the factory floor and displays it in an easy-to-understand interface for operators. This enables immediate responses to issues like equipment malfunctions or process deviations. SCADA focuses on maintaining consistent control and operation of processes rather than analyzing historical data or optimizing long-term performance. Its primary strength lies in real-time visibility and control of shop floor activities, making it indispensable for operational management.
7 Differences Between MES vs SCADA
The main differences between MES and SCADA lie in their scope, functionality, and the types of decisions they support. MES (Manufacturing Execution System) focuses on managing the entire production lifecycle, ensuring strategic alignment between shop floor operations and broader business objectives. SCADA (Supervisory Control and Data Acquisition), on the other hand, is designed for real-time monitoring and control of equipment, providing operators with visibility into machinery performance and process conditions.
While both systems are essential for manufacturing environments, understanding their distinct roles is critical for selecting the right tool or ensuring effective integration. Below are the seven key differences that highlight the unique strengths of MES and SCADA.
Aspect | MES | SCADA |
Scope | Manages the entire production lifecycle, including planning, resource allocation, and quality control. | Focuses on real-time monitoring and control of equipment on the shop floor. |
Data Handling | Processes and analyzes data for actionable insights, supporting long-term optimization. | Collects real-time data from sensors and PLCs for immediate adjustments. |
Primary Users | Designed for managers and decision-makers to support strategic planning and performance tracking. | Used by operators and technicians for monitoring equipment and process control. |
Function | Connects shop floor operations to enterprise systems for holistic production management. | Ensures stability and control of machinery and production processes. |
Integration | Integrates with ERP and enterprise tools for end-to-end visibility across production. | Interfaces directly with sensors, PLCs, and shop floor equipment for real-time communication. |
Decision-Making | Supports tactical and strategic decisions based on production trends and resource optimization. | Facilitates operational decisions like responding to alarms and troubleshooting. |
Analysis Type | Focuses on historical data analysis for identifying trends and driving long-term improvements. | Provides real-time monitoring and immediate insights for quick responses. |
1. Scope of Operation
The primary distinction between MES and SCADA lies in their scope. MES covers the entire production lifecycle, including resource planning, production scheduling, quality control, and performance monitoring. It is designed to bridge the gap between shop floor operations and enterprise-level systems, ensuring that production processes align with broader business objectives. MES enables manufacturers to track, manage, and optimize every step, from raw materials to finished goods delivery.
SCADA, on the other hand, operates on a narrower scope, focusing exclusively on real-time monitoring and control of equipment and processes on the shop floor. It ensures machinery operates correctly and processes remain stable, safeguarding production continuity. Unlike MES, SCADA does not extend into areas like resource allocation or product lifecycle management.
2. Data Handling
SCADA specializes in collecting real-time data from sensors, actuators, and PLCs. The data is immediately processed and used for quick adjustments to maintain equipment performance and production stability. For example, SCADA might detect a temperature fluctuation in a machine and trigger a system response to stabilize it. This level of precision is essential for maintaining consistent operations.
MES takes data a step further by analyzing and processing it to uncover actionable insights. It uses historical data trends and production metrics to inform long-term decision-making. This includes identifying bottlenecks, predicting maintenance needs, and improving overall efficiency. MES provides manufacturers with the insights needed to move from reactive problem-solving to proactive optimization.
3. Primary Users
SCADA is designed for operators and technicians who focus on real-time equipment monitoring and control. These users rely on SCADA to detect issues, respond to alarms, and maintain uninterrupted production processes. Their primary concern is keeping the shop floor running smoothly and ensuring equipment performs as expected.
MES is tailored for managers and decision-makers who need a broader perspective on production operations. It provides tools for tracking performance metrics, managing resources, and ensuring quality standards are met. MES supports high-level planning, empowering leadership to align production processes with organizational goals and strategic priorities.
4. Control vs. Management
SCADA’s primary function is control. It ensures that machinery operates within predefined parameters, monitoring equipment for deviations and making adjustments to prevent downtime or inefficiencies. SCADA excels in maintaining process stability, focusing on the immediate needs of the shop floor.
MES emphasizes management, connecting production activities with higher-level business objectives. It oversees resource allocation, workflow optimization, and performance tracking to ensure production processes are efficient and aligned with organizational strategies. MES provides a more comprehensive view of operations, helping manufacturers to optimize their processes holistically.
5. Integration Capabilities
MES integrates seamlessly with ERP systems and other enterprise tools, creating end-to-end visibility across the production lifecycle. This integration allows manufacturers to link shop floor data with financial, logistical, and strategic goals. For example, MES can provide insights into production costs, helping businesses align their operations with budgetary requirements.
SCADA interfaces directly with shop floor equipment, such as sensors, PLCs, and actuators. Its integration capabilities are focused on unlocking communication between devices to ensure smooth operations. While effective for real-time control, SCADA lacks the broader integration capabilities of MES, which extend to enterprise-level systems.
6. Decision-Making Levels
SCADA supports real-time operational decisions, such as troubleshooting equipment, responding to alarms, and making adjustments to maintain process stability. Operators rely on SCADA’s immediate feedback to keep production running without interruption.
MES enables more strategic and tactical decision-making. Managers use MES to analyze production trends, optimize resource allocation, and implement long-term improvements. MES helps manufacturers identify inefficiencies, improve productivity, and align production with business goals, supporting decisions that go beyond the shop floor.
7. Real-Time vs. Historical Analysis
"SCADA excels at real-time monitoring and control, giving operators immediate visibility into equipment performance and process conditions."
SCADA excels in real-time monitoring, providing immediate insights into equipment performance and process conditions. This enables quick responses to issues, such as machinery malfunctions or process deviations, preventing costly disruptions to production.
MES focuses on historical data analysis, compiling information over time to identify trends, inefficiencies, and areas for improvement. This data supports predictive maintenance, resource planning, and strategic optimization efforts, ensuring continuous improvement and long-term success. MES transforms raw data into actionable insights that drive sustained operational excellence.
MES and SCADA serve distinct but complementary roles in manufacturing environments. SCADA ensures real-time control and stability at the equipment level, enabling smooth operations and quick responses to process changes. MES, on the other hand, drives strategic improvements across the production lifecycle, optimizing workflows, resource allocation, and decision-making.
Understanding the difference between MES and SCADA helps manufacturers implement the right systems for their needs or integrate them effectively. Together, these tools create a powerful framework for operational excellence, scalability, and long-term success in modern manufacturing.
Benefits of MES for Scalable Manufacturing
Manufacturing Execution Systems (MES) are essential for manufacturers seeking to meet increasing production demands without compromising on quality or efficiency. These systems enable seamless coordination of processes, allowing businesses to adapt to changes, eliminate inefficiencies, and maintain consistent standards across production lines. MES supports scalability by delivering real-time insights, ensuring resource optimization, and fostering a culture of continuous improvement.
Whether addressing operational bottlenecks, improving scheduling, or integrating enterprise systems, MES provides the tools manufacturers need to achieve growth while maintaining reliability.
- Real-Time Production Visibility: MES provides real-time insights into production performance, bottlenecks, and resource use, ensuring smooth and efficient operations as production scales.
- Enhanced Quality Control: Built-in quality checkpoints ensure consistent standards and minimize defects, reducing waste and maintaining customer satisfaction.
- Optimized Resource Allocation: MES tracks and allocates materials, equipment, and labor efficiently, ensuring resources are deployed where they are needed most.
- Predictive Maintenance: Proactive equipment monitoring prevents unplanned downtime, extends machinery lifespan, and ensures uninterrupted production.
- Seamless ERP Integration: MES connects with ERP systems, aligning shop floor data with business objectives to enhance decision-making and scalability.
- Faster Decision-Making: Consolidated production data provides actionable insights, making quick adjustments to schedules, resources, and operations.
MES is a vital asset for manufacturers focused on scalability and operational efficiency. Its ability to enhance production visibility, streamline workflows, and ensure quality makes it indispensable in modern manufacturing environments. With tools like predictive maintenance, resource optimization, and ERP integration, MES allows manufacturers to scale their operations confidently while meeting market demands. Investing in MES systems creates a foundation for sustained growth and ensures businesses remain agile.
When to Use MES, SCADA, or Both?
Selecting the right system for your manufacturing operations is critical to achieving both immediate and long-term goals. MES and SCADA serve distinct purposes, with MES focusing on production management and efficiency and SCADA addressing real-time equipment monitoring and control. The decision to use one, the other, or a combination of both depends on your specific operational requirements, such as optimizing workflows, maintaining process stability, or aligning shop floor activities with enterprise objectives.
Understanding when to implement MES , SCADA, or both systems helps manufacturers unlock the full potential of their operations. Whether the goal is to improve scalability, reduce downtime, or gain better insights into production, these systems offer valuable solutions tailored to different needs.
When to Use MES
MES is an excellent choice for manufacturers focused on improving overall production efficiency, resource allocation, and long-term operational planning. It is instrumental in environments with complex production workflows, where seamless coordination across multiple processes is essential. MES enables consistent quality control, detailed performance tracking, and alignment with enterprise-level systems like ERP. Manufacturers looking to scale operations without compromising efficiency or quality benefit from the actionable insights MES provides, ensuring production remains aligned with business goals.
When to Use SCADA
SCADA is ideal for real-time equipment monitoring and process control. It is best suited for applications requiring immediate responses to operational changes or equipment performance issues. Industries that rely heavily on automation, such as energy, utilities, or high-volume manufacturing, depend on SCADA to maintain process stability and ensure operational consistency. SCADA systems excel at providing real-time data from sensors and machinery, enabling operators to make quick adjustments to avoid downtime or disruptions.
When to Use Both
Using MES and SCADA together delivers the most comprehensive solution for manufacturers looking to integrate real-time control with strategic production management. SCADA ensures smooth day-to-day operations by monitoring and controlling equipment, while MES provides insights into long-term performance, resource planning, and quality management. Together, these systems enable end-to-end visibility, supporting manufacturers in achieving innovative factory initiatives and leveraging advanced analytics for continued improvement. Integration of MES and SCADA is particularly beneficial for businesses that align shop floor activities with enterprise-wide goals, ensuring short-term operational stability and long-term efficiency.
MES and SCADA are complementary systems that cater to different manufacturing needs but offer the greatest value when used together. MES drives production efficiency and strategic alignment, while SCADA ensures equipment stability and immediate responsiveness. Implementing these systems in tandem enables manufacturers to achieve operational resilience, and meet production demands. Choosing the right approach allows businesses to address both present challenges and future growth opportunities effectively.
Manufacturers worldwide are embracing cloud-based solutions to achieve efficiency, precision, and scalability. At 42Q, we combine decades of manufacturing expertise with cutting-edge technology to deliver smart connected manufacturing. Our flexible, cloud-native MES platform enhances visibility, streamlines operations, and accelerates digital transformation. Discover how our solutions can empower your factory to achieve its full potential.
Key Takeaways
- MES optimizes the entire production lifecycle, enabling manufacturers to enhance efficiency, maintain quality, and scale operations seamlessly.
- SCADA provides real-time monitoring and control, ensuring equipment and processes run smoothly without interruptions.
- MES and SCADA serve different purposes but complement each other when integrated, offering end-to-end visibility and operational efficiency.
- Integrating MES with ERP systems provides strategic insights, helping manufacturers align production with business goals.
- Predictive maintenance, traceability, and brilliant factory support make MES critical for manufacturers pursuing scalable and sustainable growth.
FAQs
MES focuses on managing the entire production lifecycle, optimizing processes, and aligning operations with business goals. SCADA is designed for real-time monitoring and control of equipment, ensuring stability at the shop floor level. Both systems play distinct roles but can complement each other when integrated.
MES and SCADA can be integrated to provide end-to-end visibility across production and operations. SCADA manages real-time control, while MES handles strategic optimization and resource planning, making their combined use ideal for scaling and achieving long-term efficiency.
MES is particularly beneficial for large-scale manufacturers because it streamlines production processes, enhances resource management, and provides actionable insights. Its ability to handle complex workflows and integrate with ERP systems makes it a powerful tool for scaling operations.
SCADA improves operational efficiency by providing real-time monitoring and control of equipment. It allows operators to respond immediately to process changes or equipment issues, minimizing downtime and ensuring consistent performance on the shop floor.
Industries like automotive, aerospace, medical devices, and energy benefit significantly from MES and SCADA. MES provides robust traceability, quality control, and resource optimization, while SCADA supports real-time process control and automation, making both systems critical for modern manufacturing.
Understanding ERP Manufacturing Execution Systems
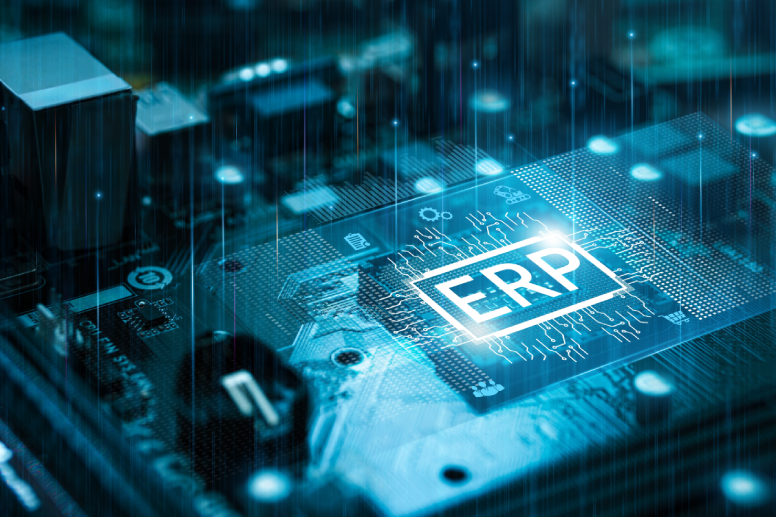
Understanding ERP Manufacturing Execution Systems
Integrating enterprise resource planning (ERP) systems with manufacturing execution systems (MES) is reshaping the way manufacturers operate.
This fusion delivers a powerful combination of real-time production insights and enterprise-level control, empowering manufacturers to address operational challenges, enhance decision-making, and streamline processes. With an increased demand for more intelligent, more connected factories, ERP-MES systems are becoming essential for achieving efficiency, accuracy, and growth in the manufacturing sector.
What is an ERP Manufacturing Execution System?
An ERP Manufacturing Execution System (MES) is a strategic integration that connects enterprise resource planning (ERP) software with MES technology to provide a unified solution for managing and optimizing manufacturing processes. ERP systems focus on overarching business operations such as finance, procurement, and inventory. In contrast, MES systems are designed to handle real-time production floor activities like scheduling, quality control, and performance monitoring.
Fusing these two systems enables manufacturers to streamline operations, minimize inefficiencies, and create a seamless data flow from the shop floor to the boardroom. Bridging the gap between operational and enterprise-level decision-making helps ERP-MES systems empower organizations to make more efficient decisions, improve productivity, and remain innovative.
How ERP and MES Systems Work Together
"ERP systems oversee high-level business processes like financial planning, procurement, and inventory management, while MES focuses on real-time production floor activities like scheduling, quality control, and performance monitoring."
The main difference between an ERP system and an MES lies in its focus and function. ERP systems oversee high-level business processes like financial planning, procurement, and inventory management. On the other hand, MES focuses on manufacturing operations, including production scheduling, quality assurance, and tracking real-time data on the factory floor.
When these systems work together, they create a robust ecosystem that ensures seamless communication between business and production processes. ERP provides the strategic oversight and long-term planning needed for resource allocation, while MES delivers real-time insights and control over manufacturing operations. Together, they close the gap between the administrative office and the factory floor, with data synchronization that improves decision-making, resource utilization, and operational efficiency.
For example, integrating ERP and MES systems allows inventory levels tracked by the ERP system to update dynamically based on production data provided by the MES. This ensures material shortages are avoided, production schedules remain on track, and customer demands are met promptly. This collaboration enhances both productivity and profitability across the organization.
Key Benefits of ERP-MES Integration
"Real-time data visibility enables manufacturers to identify inefficiencies and make informed decisions quickly, ensuring proactive management of production schedules and resource planning."
Integrating an ERP manufacturing execution system is a critical step for manufacturers to be efficient in modern production environments. These systems create a seamless connection between strategic planning and real-time operations, ensuring optimized workflows, enhanced visibility, and precise control over every aspect of the manufacturing process. By bridging this gap, ERP MES systems empower manufacturers to achieve better operational efficiency, improved quality, and scalability for growth. In this piece, we’ll focus on the key benefits and why this integration is essential for businesses in industries ranging from automotive to medical devices.
- Real-Time Data Visibility: ERP and MES systems work together to centralize data, giving manufacturers instant insights into production schedules, inventory, and operational metrics. This real-time access helps more informed decision-making and reduces inefficiencies on the factory floor.
- Enhanced Production Efficiency: Eliminating communication gaps between departments ensures production schedules align with material availability and workforce capacity. This streamlining of operations minimizes downtime and accelerates time-to-market.
- Improved Quality Control: With MES data seamlessly integrated into ERP systems, manufacturers can monitor production processes and quickly address potential quality issues. This ensures consistent adherence to industry standards while reducing defects.
- Scalability for Growth: ERP-MES integration allows businesses to maintain operational consistency across multiple locations. Whether scaling up production or adapting to demands, manufacturers can rely on these systems for stability and flexibility.
- Cost Savings Through Process Optimization: Streamlined workflows and improved operational efficiency reduce waste and carrying costs. Manufacturers can reinvest these savings into innovation and expansion efforts.
- Regulatory Compliance Support: By automating data collection and ensuring traceability , ERP-MES systems simplify adherence to industry regulations. Documentation for audits and certifications becomes easily accessible.
- Enhanced Customer Satisfaction: Integrated systems help ensure on-time deliveries, accurate production timelines, and consistent quality—all of which contribute to meeting or exceeding customer expectations.
Adopting an ERP manufacturing execution system offers manufacturers the opportunity to unify and optimize their operations, ensuring long-term success. With key benefits like real-time visibility, improved efficiency, and streamlined compliance processes, ERP MES systems are indispensable tools for any organization focused on innovation and growth. Investing in this integration now ensures not only immediate performance improvements but also the ability to adapt and succeed in future manufacturing challenges.
8 Steps for Implementing an ERP-MES System
A successful ERP-MES system implementation requires a structured and methodical approach to minimize risks and maximize benefits. With proper planning, manufacturers can align the system’s capabilities with their specific operational goals, ensuring a smoother transition and improved overall performance. Every phase, from evaluating business needs to post-deployment monitoring, plays a vital role in ensuring that the system delivers measurable improvements in productivity, compliance, and decision-making efficiency.
1. Assess Business Needs and Goals
Begin the process by conducting a comprehensive evaluation of your manufacturing operations. Identify pain points, inefficiencies, and areas where the integration can create value. Consider factors like production delays, resource allocation challenges, or data silos that slow decision-making. Define measurable goals such as reducing production downtime, improving product quality, or enhancing supply chain visibility. Setting clear objectives ensures the implementation delivers targeted outcomes.
2. Select the Right ERP-MES Solution
The success of the integration heavily depends on selecting software that aligns with your specific manufacturing processes. Evaluate solutions based on their compatibility with existing systems, scalability for future growth, and ability to support real-time data exchange. Focus on features like ease of use, vendor support, and compliance with industry-specific standards. Conduct demos and involve relevant stakeholders to ensure the solution meets technical and operational requirements.
3. Develop a Detailed Implementation Plan
A well-defined plan is crucial for a smooth rollout. Outline key milestones, resource requirements, and timelines to avoid unexpected delays or cost overruns. Assign roles and responsibilities to cross-functional teams, including IT, operations, and management, to ensure department alignment. Phased rollouts often prove effective, allowing you to test the system on a smaller scale before full deployment.
4. Ensure Infrastructure Readiness
Evaluate and prepare your existing infrastructure to support the ERP-MES integration. This includes assessing hardware, software, network capabilities, and security protocols. Upgrading outdated equipment or systems may be necessary to ensure seamless data exchange and operational efficiency. Collaborate with IT teams to address technical gaps and establish the system’s foundation for success.
5. Data Migration and Validation
Accurate and complete data migration is essential for the new system to function effectively. Cleanse and standardize existing data to eliminate inconsistencies or inaccuracies. Securely transfer critical information such as inventory records, production schedules, and supplier details into the new system. After migration, validate data accuracy and integrity through rigorous testing to prevent errors that could disrupt operations.
6. Train Employees on the New System
Comprehensive training equips employees with the skills to use the ERP-MES system effectively. Conduct workshops hands-on training sessions, and provide user-friendly guides tailored to different organizational roles. Address any concerns or resistance to change by highlighting the system’s benefits and demonstrating how it simplifies workflows. Continuous support during and after deployment ensures employees feel confident using the new tools.
7. Monitor and Optimize the System Post-Deployment
After rolling out the ERP-MES system, closely monitor its performance against predefined goals. Gather feedback from users to identify any operational bottlenecks, inefficiencies, or areas for improvement. Use real-time analytics and system-generated insights to fine-tune processes and ensure maximum value. Periodic reviews and updates align the system with business needs and technological advancements.
8. Establish Ongoing Support and Maintenance
Maintaining the system is vital for long-term success. Develop a support structure that includes vendor assistance, internal IT teams, and a robust help desk. Regular software updates, security checks, and system health monitoring protect against vulnerabilities and maintain optimal performance. Proactive maintenance ensures the ERP-MES system remains reliable and scalable as your organization grows.
Implementing an ERP-MES system is not just about adopting new technology—it’s about fostering an operational shift that delivers sustained improvements. Each step in the process is critical to creating a seamless integration that supports both immediate objectives and long-term growth. With the right planning and execution, manufacturers can unlock the full potential of ERP-MES systems, improving efficiency, reducing costs, and staying innovative in their industries. Ensuring ongoing support and periodic evaluations will further strengthen the system’s ability to adapt and evolve with organizational needs.
Overcoming Challenges in ERP-MES Deployment
Implementing an ERP-MES system transforms manufacturing operations, but can introduce unique challenges during deployment. Addressing these challenges requires strategic planning, strong stakeholder collaboration, and proactive solutions. Anticipating potential obstacles and preparing actionable strategies ensures smoother integration, reduces downtime, and maximizes the value of an ERP-MES system investment.
- Complexity of Integration: Connecting ERP and MES systems involves merging diverse data sources, software, and processes. Selecting a solution with high compatibility and engaging experienced technical support can reduce integration hurdles.
- Resistance to Change: Employees may resist new technologies due to fear of disruption or lack of familiarity. Clear communication, ongoing support, and robust training help teams embrace and utilize the system effectively.
- High Initial Costs: The upfront investment in an ERP-MES system can appear significant. Conducting a detailed cost-benefit analysis highlights long-term savings and operational improvements, justifying the initial expenditure.
- Data Security Risks: Merging data from production and business systems increases exposure to cyber threats. Choosing a system with strong security features, such as encryption and role-based access control, protects sensitive data.
- Customization Requirements: Manufacturing processes often require tailored solutions. Customizing ERP-MES systems to meet unique operational needs can be time-intensive. Selecting a flexible system that supports modular upgrades ensures scalability and adaptability.
- Downtime During Implementation: System deployment may temporarily disrupt manufacturing operations. Planning phased rollouts or testing the system in smaller environments minimizes downtime and avoids large-scale interruptions.
- Data Migration Challenges: Transferring historical data into the new system without errors can be complex. Ensuring thorough data validation during migration prevents inaccuracies and ensures system reliability.
Overcoming deployment challenges is critical to ensuring the success of ERP-MES system implementation. Careful preparation, clear communication, and collaborative efforts help manufacturers minimize disruptions and address key obstacles. Each challenge presents an opportunity to refine processes, enhance decision-making, and build a more resilient production environment. Proactively addressing these issues unlocks seamless integration and delivers the long-term benefits of improved productivity, operational efficiency, and scalability.
Maximizing ROI with ERP-MES Systems
Achieving a strong return on investment (ROI) with an ERP-MES system requires aligning the technology with business goals and focusing on measurable outcomes. Manufacturers can unlock significant value by leveraging the system’s capabilities to enhance efficiency, reduce costs, and improve customer satisfaction.
Streamlining operations is one of the most effective ways to maximize ROI. Integrating ERP and MES ensures data flows seamlessly across departments, reducing manual effort and operational bottlenecks. This leads to faster decision-making, higher productivity, and fewer production delays. Focusing on quality improvements also drives ROI. Real-time monitoring and reporting help manufacturers detect and resolve quality issues early in production. This minimizes waste, reduces rework, and ensures compliance with stringent industry standards.
Effective use of predictive analytics within the system supports equipment maintenance and lowers unplanned downtime. Monitoring real-time data from MES systems enables manufacturers to anticipate equipment failures and address issues before they disrupt operations. This increases uptime and extends the life of manufacturing assets. Maximizing ROI also involves training employees to use the ERP-MES system efficiently. Empowering your team with the knowledge and skills to leverage the system enhances productivity and drives better results across all operations.
These efforts ensure that ERP-MES integration delivers measurable business value, helping manufacturers optimize resources and meet customer demands. Focusing on these areas establishes a pathway to long-term operational excellence and financial success.
Future Trends in ERP and MES Technology
ERP and MES technologies continue to adapt to meet the demands of modern manufacturing. By integrating advanced innovations, these systems are driving operational efficiency, improving decision-making, and helping manufacturers to adapt to emerging challenges. Staying ahead of technological advancements is not just about remaining competitive—it’s about improving operations to achieve higher productivity, sustainability, and flexibility.
Below are some of the most influential advancements shaping the future of ERP and MES systems.
- Artificial Intelligence Integration: AI-powered capabilities are being embedded into ERP and MES systems to analyze vast datasets, forecast production schedules, and detect maintenance needs before they become critical. This integration enhances operational efficiency while reducing downtime and increasing predictive decision-making.
- Cloud-Based Solutions: Cloud technology is becoming the backbone of ERP and MES systems. It offers scalability, cost-effectiveness, and secure remote access to manage operations globally. Cloud platforms also allow for real-time visibility across facilities, supporting agile and connected manufacturing.
- Industrial Internet of Things (IIoT): IIoT-enabled ERP-MES systems leverage sensors and connected devices to gather real-time production data. This connectivity allows manufacturers to optimize operations, predict maintenance requirements, and enhance resource management through precise monitoring and control.
- Digital Twin Technology: Digital twins create virtual replicas of physical manufacturing systems, offering manufacturers the ability to simulate, monitor, and optimize operations. By integrating with ERP and MES systems, digital twins provide actionable insights into system performance.
- Advanced Analytics and Dashboards: Advanced analytics and dynamic dashboards are empowering manufacturers with actionable insights into production performance. Customizable dashboards help users to monitor KPIs, identify inefficiencies, and make data-driven decisions in real time, improving overall operational effectiveness.
The evolution of ERP and MES technology is reshaping how manufacturers approach efficiency, scalability, and sustainability. Adopting advancements such as AI, IIoT, and cloud-based solutions ensures businesses are equipped to address future challenges while staying ahead in their industries. By leveraging these powerful tools, organizations can enhance their processes, improve visibility, and drive long-term results.
Manufacturers worldwide are adopting integrated solutions to improve efficiency, visibility, and operational control. At 42Q, we bring decades of manufacturing expertise and advanced technology to deliver cloud-native ERP-MES solutions. Our innovative platform simplifies operations, optimizes resource allocation, and accelerates digital transformation. Learn how we can help your factory unlock its true potential.
Key Takeaways
- ERP-MES integration unifies enterprise-level planning with real-time production management, enabling data-driven decision-making.
- Manufacturers benefit from enhanced visibility, improved efficiency, and streamlined workflows.
- Scalable ERP-MES solutions support small and large manufacturers, adapting to diverse industries and operational needs.
- Sustainability is a growing focus, with ERP-MES systems helping businesses reduce waste and track environmental metrics.
- Advanced technologies like AI, IIoT, and edge computing are shaping the future of ERP-MES systems, offering increased efficiency and innovation.
FAQ's
An ERP-MES system bridges the gap between enterprise-level planning and real-time production management. Its purpose is to synchronize processes, improve data visibility, and enhance decision-making to boost overall operational efficiency in manufacturing.
ERP-MES integration provides centralized data, real-time monitoring, and streamlined workflows. These benefits lead to reduced downtime, improved production accuracy, and optimized resource utilization, which support better business outcomes.
ERP-MES systems are scalable, making them accessible to manufacturers of all sizes. Small manufacturers can benefit by reducing inefficiencies, automating manual processes, and improving production planning with the system's powerful features.
ERP-MES systems are versatile and serve industries including automotive, medical devices, aerospace, and clean energy. These systems support with productivity, compliance, and enable advanced operational control in various manufacturing environments.
7 Benefits of Traceability in Manufacturing
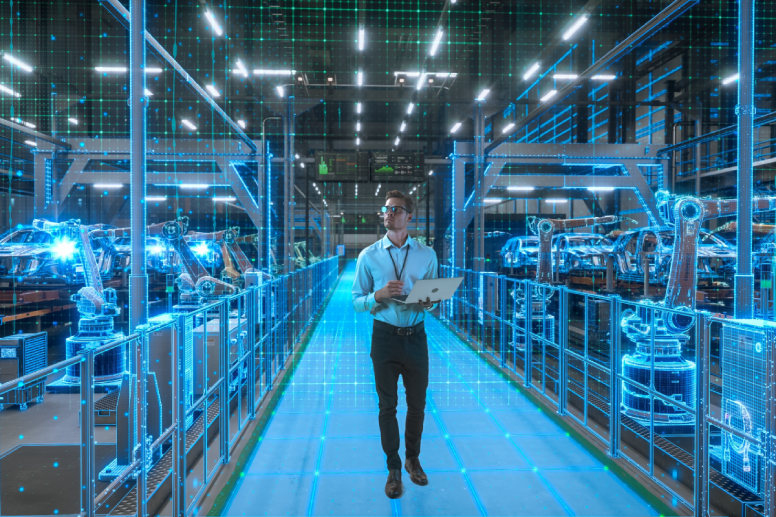
7 Benefits of Traceability in Manufacturing
Manufacturing traceability is one of the most effective strategies for achieving operational excellence while meeting rising demands for transparency and accountability.
It enables manufacturers to track every aspect of a product’s lifecycle, from sourcing raw materials to delivering the final product, offering unparalleled insights into production workflows. As industries highly prioritize quality, compliance, and efficiency, implementing traceability systems has become essential for optimizing processes, safeguarding reputation, and ensuring customer satisfaction.
What is Traceability in Manufacturing?
Traceability in manufacturing refers to the ability to track and document every stage of a product's lifecycle, from sourcing raw materials to final delivery. This process encompasses capturing data related to production, assembly, testing, and distribution, creating a detailed and comprehensive product history. With manufacturing traceability, businesses ensure every component and process is accounted for, providing the visibility needed to identify inefficiencies, maintain compliance with industry standards, and enhance overall operational effectiveness.
At its core, traceability focuses on building transparency throughout the supply chain by ensuring seamless information flow. This clarity plays a crucial role in mitigating production risks, reducing quality control issues, and improving accountability. Manufacturing traceability benefits extend beyond operations, as it also strengthens relationships with stakeholders by providing confidence in the accuracy and reliability of the production process.
Why Traceability in Manufacturing Matters
Traceability is an essential factor in maintaining operational efficiency and protecting product quality in manufacturing environments. It serves as a cornerstone for achieving compliance with strict regulatory requirements, improving workflow transparency, and addressing operational risks before they escalate. By enabling manufacturers to retain accurate and detailed records at every stage of production, traceability fosters proactive decision-making and continuous process improvement. These benefits of traceability in manufacturing contribute directly to a company’s ability to meet customer expectations and adhere to industry demands.
Furthermore, manufacturing traceability benefits include safeguarding brands from financial and reputational risks tied to recalls and quality failures. Traceability systems help manufacturers quickly trace and isolate issues without interrupting production lines, ensuring that operations continue without compromise. This level of accountability is essential for meeting the expectations of regulators, supply chain partners, and consumers who demand greater visibility into the origins and handling of products.
7 Benefits of Traceability in Manufacturing
Traceability in manufacturing is a critical enabler of operational excellence, regulatory compliance, and customer trust. It provides manufacturers with the tools to monitor and document every step of production, from sourcing raw materials to delivering finished products. This capability enhances visibility across the supply chain, ensures adherence to quality standards, and supports faster decision-making when issues arise. As industries continue to demand higher levels of accountability and transparency, traceability emerges as an essential practice, not just an advantage.
The benefits of traceability in manufacturing extend beyond quality control. Organizations can improve efficiency, reduce operational risks, and respond more effectively to market needs. Whether it’s minimizing the costs associated with product recalls or building confidence with consumers through transparency, traceability creates tangible value across all levels of operations. This overview highlights the seven most significant benefits that traceability brings to manufacturing environments, underscoring its role in driving success.
1. Improves Product Quality and Consistency
Consistent product quality is essential for manufacturers operating in highly regulated industries. Traceability systems enable real-time monitoring of production processes, allowing manufacturers to identify deviations or anomalies at any stage. This capability minimizes defects and enhances the uniformity of outputs, creating products that consistently meet quality standards.
Detailed tracking of materials, equipment usage, and operator activities allows manufacturers to pinpoint the root causes of defects. Identifying and resolving recurring issues leads to continuous improvement, reducing waste and strengthening production reliability. Manufacturers can elevate customer satisfaction and reduce the financial losses associated with defective goods by standardizing quality assurance across the entire production cycle.
2. Enhances Supply Chain Transparency
The modern supply chain often involves multiple vendors, geographies, and production sites, creating a complex ecosystem of interdependencies. Traceability simplifies this complexity by providing an end-to-end view of material and product flows, ensuring stakeholders can monitor every step in real-time. Transparency reduces the risks of delays, miscommunication, and inefficiencies while fostering greater accountability among suppliers and partners.
Supply chain visibility ensures manufacturers can trace raw materials back to their source, confirming compliance with ethical and regulatory standards. Additionally, clear documentation enables businesses to identify and resolve potential disruptions quickly, avoiding costly downtime. This level of oversight strengthens supply chain resilience and improves collaboration across all tiers of the manufacturing network.
3. Reduces Recall Costs and Risks
Product recalls are one of the most significant financial and reputational risks manufacturers face. Traceability systems allow manufacturers to act quickly and decisively when issues arise, effectively isolating affected products. This targeted approach significantly reduces the scale and costs of recalls compared to less efficient methods.
The ability to trace products and materials back through the production process streamlines investigations into quality or safety concerns. Manufacturers can respond swiftly to regulatory inquiries, mitigating potential penalties and reinforcing consumer trust. Minimizing recall-related expenses also protects the bottom line, helping manufacturers allocate resources toward innovation and growth.
4. Facilitates Regulatory Compliance
Industries such as automotive, aerospace, and medical devices must adhere to stringent regulatory standards to ensure product safety and reliability. Traceability systems provide the documentation and tracking capabilities necessary to meet these requirements. Detailed records of material origins, production conditions, and testing data make compliance audits seamless and efficient.
Manufacturers that invest in traceability systems demonstrate their commitment to accountability and responsibility. This proactive approach reduces the risk of legal penalties, delays, or loss of certifications. Meeting compliance standards consistently also strengthens relationships with customers, partners, and regulators, enhancing a manufacturer’s reputation as a reliable and ethical business.
5. Boosts Operational Efficiency
Operational inefficiencies can result in costly delays, wasted materials, and dissatisfied customers. Traceability offers manufacturers the tools to optimize production by identifying workflow bottlenecks and inefficiencies. Access to real-time data enables teams to make quick adjustments, ensuring processes run smoothly, and resources are used effectively.
Efficiency gains from traceability extend to inventory management, as manufacturers can monitor stock levels, reduce waste, and prevent overproduction. These improvements lower operational costs and enhance production speed without compromising quality. A streamlined, efficient operation ultimately positions manufacturers to respond more effectively to market demands and customer expectations.
6. Enables Improved Decision Making
Traceability systems generate a wealth of data manufacturers can use to improve decision-making processes. Analyzing this data helps identify trends, anticipate challenges, and identify growth opportunities. Manufacturers can optimize production schedules, fine-tune resource allocation, and predict maintenance needs based on historical insights.
The strategic use of traceability data empowers businesses to move away from reactive problem-solving and toward proactive planning. Decision-making backed by reliable data reduces risks and enhances outcomes across production, quality control, and supply chain management. This level of precision drives innovation and keeps manufacturers innovative.
7. Strengthens Customer Trust and Brand Reputation
Modern customers value transparency and accountability, and manufacturers that can demonstrate these qualities gain a significant edge. Traceability systems ensure manufacturers can provide customers with detailed information about product origins, quality assurance, and compliance with ethical standards. This visibility builds trust and reassures consumers that their purchases align with their values.
Establishing a reputation for transparency and reliability strengthens customer loyalty and boosts brand reputation. A manufacturer’s ability to respond effectively to quality concerns or recalls reinforces its commitment to consumer safety. By prioritizing trust and accountability, businesses can differentiate themselves in crowded markets and secure long-term customer relationships.
Traceability is a vital component for manufacturers striving to achieve higher standards in quality, compliance, and operational efficiency. It empowers businesses to address challenges with confidence, mitigate risks, and deliver consistent results that align with customer and regulatory expectations. Through its ability to streamline processes, reduce costs, and foster trust, traceability plays an indispensable role in strengthening supply chain performance and positioning manufacturers as reliable and ethical leaders in their industries.
Organizations adopting traceability systems are better equipped to adapt to demands while safeguarding their brand reputation. With the right tools and processes in place, manufacturers can create a culture of accountability and precision that fuels long-term growth. Traceability ensures manufacturers remain agile, proactive, and prepared to meet the challenges and opportunities.
Implementing a Scalable Manufacturing Traceability System
Implementing a scalable traceability system in manufacturing requires careful planning and the right technology to ensure success. A robust traceability solution should provide real-time visibility, integrate seamlessly with existing systems, and adapt to the unique needs of your operations. Prioritizing scalability ensures the system can grow with your business, accommodating increased production volume, expanded product lines, or additional facilities without significant disruptions.
Choosing the right tools is essential to achieving effective traceability. Cloud-based solutions, for example, enable centralized data collection and global visibility across multiple locations. Integration with Enterprise Resource Planning (ERP) systems, production equipment, and quality management platforms allows streamlined workflows and more accurate tracking. Automation further enhances traceability by reducing manual errors and ensuring data consistency.
Training employees and fostering a culture of accountability are also critical to a successful implementation. Teams should be well-versed in using the system to track, document, and analyze production processes effectively. Additionally, clear communication of the system's benefits encourages buy-in from all stakeholders, ensuring the long-term success of your traceability efforts. A well-implemented traceability system is not just a technical investment—it’s a strategic decision that drives operational excellence and builds trust throughout your value chain.
Manufacturers worldwide embrace cloud-based solutions to achieve efficiency, precision, and scalability. At 42Q, we combine decades of manufacturing expertise with cutting-edge technology to deliver smart, connected manufacturing. Our flexible, cloud-native MES platform enhances visibility, streamlines operations, and accelerates digital transformation. Discover how our solutions can empower your factory to achieve its full potential.
Key Takeaways
- Traceability ensures product quality and consistency by identifying and addressing defects early in production.
- Supply chain transparency improves accountability and helps mitigate risks such as delays or material disruptions.
- Efficient recall management reduces costs and protects brand reputation by precisely isolating issues.
- Regulatory compliance is streamlined through detailed tracking and documentation of production workflows.
- Data-driven insights enable proactive decision-making, optimizing operations and fostering innovation.
FAQ's
Manufacturing traceability ensures that every product’s lifecycle is accurately tracked and documented. This approach provides manufacturers with insights into production processes, enhances product quality, and ensures compliance with regulatory standards. Traceability also helps businesses address operational challenges, such as recalls or inefficiencies, in a more targeted and efficient manner.
Traceability creates a data flow across the supply chain, allowing stakeholders to monitor materials and products at every stage. This level of transparency helps businesses reduce delays, improve accountability, and quickly address disruptions. Additionally, supply chain visibility ensures compliance with ethical and quality standards, which builds trust among partners and customers.
Industries such as automotive, aerospace, medical devices, and food manufacturing benefit significantly from traceability due to strict compliance requirements and the need for high-quality standards. However, any manufacturing sector can leverage traceability to improve operational efficiency, enhance product quality, and reduce risk.
Technology is a critical enabler of traceability, providing tools like cloud-based platforms, automation, and real-time data collection. These technologies streamline processes, reduce human errors, and ensure the accuracy of tracking and documentation efforts. Integration with ERP systems and production equipment further enhances the effectiveness of traceability systems.
Traceability systems provide detailed documentation of materials, production conditions, and quality assurance measures. This information helps manufacturers meet regulatory standards more efficiently, simplifying audits and reducing the risk of penalties. Compliance with regulations also enhances brand reputation and builds trust with customers and stakeholders.
A Guide to Traceability
in Manufacturing
A Guide to Traceability in Manufacturing
Traceability is redefining how manufacturers approach quality, efficiency, and compliance.
As a critical component of modern production, traceability allows businesses to track every stage of the manufacturing process, from raw materials to finished products. This ensures greater accountability, enhances product quality, and supports compliance with industry regulations. With growing consumer expectations and stricter regulatory demands, traceability has shifted from a competitive advantage to a necessity.
What is Traceability in Manufacturing?
Traceability in manufacturing refers to tracking and documenting every stage of a product’s lifecycle, from raw materials to the finished product delivered to the customer. This systematic process ensures manufacturers can identify the origin, journey, and current status of materials, components, and products within their supply chain and production workflows. Traceability is vital for meeting regulatory compliance, improving product quality, and swiftly addressing any issues arising during or after production.
Manufacturing traceability typically involves documenting two key dimensions: tracking, which monitors the forward movement of materials and products through production stages, and tracing, which identifies and retraces the journey of materials and components backward in the event of defects, recalls, or quality checks. These aspects help create a transparent and efficient manufacturing process that fosters accountability, efficiency, and customer confidence.
Importance of Traceability in Manufacturing
Traceability in manufacturing is essential for ensuring high-quality production standards, meeting strict regulatory requirements, and fostering operational excellence. It empowers manufacturers with the ability to track, monitor, and analyze every stage of the production process—from raw materials to finished goods—while maintaining full transparency and accountability. As supply chains become more complex and consumer demands for safety and sustainability rise, implementing robust traceability systems has become a cornerstone of modern manufacturing.
The ability to trace materials, processes, and outcomes equips businesses to proactively manage risks, improve workflows, and strengthen trust with customers and regulators. Traceability is not just a compliance tool—it is a strategic advantage that helps manufacturers while meeting their operational goals.
Enhancing Quality Control and Regulatory Compliance
Traceability ensures that manufacturers maintain consistent quality across all products by providing detailed records of materials, processes, and outcomes. This level of documentation allows manufacturers to identify deviations from established standards and take corrective action before issues escalate. Compliance with safety standards is non-negotiable in highly regulated industries such as medical devices and automotive. Traceability systems provide the data to prove adherence to these requirements, helping businesses avoid legal penalties, protect their certifications, and uphold consumer trust.
Manufacturers that invest in traceability solutions are also better equipped to meet international standards like ISO 9001 or industry-specific regulations. For example, aerospace companies often rely on traceability to ensure that every component used in aircraft production meets stringent quality and safety criteria. This ability to provide a complete audit trail demonstrates the company’s commitment to reliability and operational excellence.
Managing Recalls and Mitigating Risks
Traceability systems are essential for managing recalls and mitigating risks associated with defective products. If a quality issue is detected, manufacturers can identify the specific lot, material, or product that caused the problem. This targeted approach significantly reduces a recall's financial and reputational impact by isolating the affected items rather than pulling entire production runs from the market.
For example, in the food and beverage sector, traceability can track the origin of contaminated ingredients, ensuring that manufacturers recall only the necessary batches. In addition to reducing waste, this approach reinforces consumer confidence by showcasing the company’s ability to respond quickly and responsibly to potential hazards.
Traceability also helps manufacturers identify trends that might indicate underlying risks, such as supplier inconsistencies or equipment malfunctions. With this information, businesses can take proactive steps to prevent future issues, saving time and money in the long term.
Improving Supply Chain Visibility and Efficiency
A robust traceability system creates a transparent supply chain, enabling manufacturers to track raw materials, components, and finished goods in real-time. This level of visibility helps businesses identify inefficiencies, such as production delays or overstocked inventory, and make data-driven decisions to optimize their workflows. Supply chain visibility also allows manufacturers to work more effectively with suppliers and distributors, strengthening relationships and fostering better communication.
In industries such as clean energy or semiconductors, where complex global supply chains are familiar, traceability ensures that manufacturers can monitor the movement of critical materials from their source to the production floor. This visibility minimizes disruptions and supports sustainability initiatives by providing insight into the environmental impact of supply chain operations.
With access to real-time data, businesses can streamline production processes, implement lean manufacturing principles, and reduce waste without sacrificing efficiency. This adaptability ensures manufacturers maintain resilience and agility in their operations, driving long-term success. Traceability systems not only support compliance but also empower businesses to innovate and deliver higher-value outcomes for both their customers and stakeholders.
Benefits of Implementing Traceability in Manufacturing Systems
"Traceability ensures real-time visibility into the movement of materials, components, and finished products, improving supply chain coordination and reducing bottlenecks."
Traceability in manufacturing has become a vital component of modern production, enabling businesses to meet high standards of quality, compliance, and efficiency. This system gives manufacturers the ability to track and analyze every aspect of their operations, from raw materials to finished goods, fostering transparency and accountability. With stricter regulations and increasing consumer demands for sustainable and reliable products, implementing traceability systems has transitioned from being an advantage to a fundamental necessity.
Manufacturers leveraging traceability can identify and address inefficiencies, mitigate risks, and strengthen their supply chain operations. This proactive approach not only ensures operational excellence but also boosts customer confidence, making traceability an indispensable tool in achieving long-term business success.
- Improved Product Quality and Consistency: Traceability systems ensure manufacturers can monitor each production stage, verifying that all materials and processes meet strict quality standards. This reduces variability and enhances customer satisfaction by delivering consistent, high-quality products.
- Regulatory Compliance and Documentation: Industries such as aerospace and pharmaceuticals face rigorous compliance demands. Traceability systems simplify this process by maintaining detailed records of materials, production activities, and outcomes, ensuring manufacturers can meet audits and certifications efficiently.
- Increased Transparency Across the Supply Chain: Real-time insights into the movement of materials, components, and finished goods enable businesses to enhance collaboration with suppliers and distributors. This transparency reduces bottlenecks, ensures timely deliveries, and strengthens overall supply chain performance.
- Proactive Risk Management: Manufacturers can detect recurring issues, such as equipment failures or supplier inconsistencies, using traceability systems. These systems allow for preventative actions, mitigating risks before they escalate into costly disruptions or regulatory violations.
- Optimized Inventory Management: Real-time tracking of materials and finished goods reduces overstocking and shortages, ensuring manufacturers always have the right resources available. This minimizes waste, streamlines inventory processes, and improves cash flow.
- Boosted Customer Confidence and Loyalty: Detailed traceability data demonstrates a commitment to quality and accountability. Customers gain confidence knowing manufacturers can resolve issues quickly, leading to stronger relationships and repeat business.
Traceability transforms manufacturing processes by ensuring greater visibility, reducing risks, and supporting compliance with complex regulations. It empowers manufacturers to operate more efficiently while meeting customer expectations for quality and reliability. Investing in traceability systems positions businesses to remain innovative, enhance their reputation, and adapt to evolving industry demands with confidence.
Lot vs Material vs Product Traceability
The main differences between lot, material, and product traceability lie in the level of detail and the specific focus areas they address within the manufacturing process. Lot traceability centers on tracking batches of products or materials produced under identical conditions, material traceability emphasizes the journey of raw materials through production, and product traceability provides an end-to-end record of an individual product’s lifecycle. Each serves a distinct purpose, ensuring compliance, enhancing quality control, and optimizing workflows based on specific operational needs.
Understanding these distinctions is critical for manufacturers aiming to implement robust traceability systems. Each type contributes to addressing regulatory requirements, managing recalls, and improving supply chain efficiency.
Lot Traceability
Lot traceability focuses on tracking and documenting specific groups or batches of products produced under the same conditions or using the same raw materials. Manufacturers use lot traceability to ensure that each batch meets quality and safety standards. It becomes especially valuable in industries where batch consistency is critical, such as pharmaceuticals, food production, and consumer goods.
For instance, if a contamination issue arises in food manufacturing, lot traceability allows manufacturers to identify and isolate the specific batch affected, minimizing the scope of recalls. This approach saves time, reduces costs, and protects consumer safety and brand reputation. Lot traceability also ensures compliance with industry-specific standards, such as FDA or ISO certifications, by providing detailed batch production records.
Material Traceability
Material traceability focuses on tracking the journey of raw materials and components from their source to their integration into the final product. This type of traceability is critical in industries with strict compliance requirements and high safety risks, such as aerospace, automotive, and medical devices.
Manufacturers rely on material traceability to verify the origin and quality of the materials used in production. It helps ensure suppliers meet sourcing standards and that all materials comply with regulatory guidelines. Material traceability also supports ethical sourcing initiatives, giving businesses visibility into their supply chains and helping them meet sustainability goals.
For example, in aerospace manufacturing, material traceability ensures that every component used in a product, such as a jet engine, can be traced back to its origin. This level of detail is necessary to meet safety regulations and build customer confidence in the final product.
Product Traceability
Product traceability provides a complete record of an individual product’s lifecycle, from initial production to delivery to the end customer. This type of traceability is significant in industries requiring high accountability and transparency, such as medical devices, high-tech manufacturing, and clean energy.
With product traceability, manufacturers can document every step of the production process, including raw materials used, manufacturing stages, quality checks, and distribution details. This comprehensive approach enables businesses to quickly identify and resolve issues with specific products, reducing downtime and minimizing costs. Product traceability also improves customer satisfaction by allowing firms to provide detailed documentation and support for the products they deliver.
Aspect | Lot Traceability | Material Traceability | Product Traceability |
Definition | Tracks batches of products produced under the same conditions or using the same materials | Tracks raw materials and components from origin to final product integration | Tracks the lifecycle of an individual product from production to delivery |
Focus | Batches or groups of products | Raw materials and components | Individual finished products |
Primary Purpose | Isolating issues within specific production batches | Ensuring material quality and compliance | Documenting complete product history |
Use Case Examples | Food recalls, pharmaceutical safety | Aerospace component tracking, ethical sourcing | Medical devices, high-tech manufacturing |
Regulatory Alignment | Ensures batch-level compliance | Verifies material standards and supplier quality | Meets end-to-end product documentation requirements |
Implementing a combination of lot, material, and product traceability offers manufacturers a comprehensive approach to quality assurance, compliance, and operational optimization. Each system strengthens a different aspect of the production process, from managing recalls efficiently to maintaining visibility across the supply chain and ensuring customer satisfaction.
Incorporating these traceability types into manufacturing systems enables businesses to meet stringent industry standards, minimize risks, and build trust with stakeholders. As production demands grow and regulatory expectations evolve, traceability remains a foundational tool for achieving sustainable success.
How to Implement a Scalable Traceability System
Establishing a scalable traceability system is essential for manufacturers aiming to meet industry regulations, improve operational efficiency, and enhance product quality. Such systems provide the transparency needed to monitor production processes, reduce risks, and ensure accountability at every stage. Traceability supports compliance while also empowering businesses to address recalls, optimize workflows, and foster stronger relationships with customers and suppliers.
To build a traceability system that aligns with organizational needs, manufacturers must focus on clear objectives, advanced technology, and seamless integration with existing operations. This approach ensures the system remains flexible, scalable, and prepared to meet future industry demands.
- Define Your Traceability Goals: Begin by identifying the specific objectives of your traceability system. Determine whether your focus is on lot traceability, material traceability, product traceability, or a combination of all three. Establishing clear goals ensures that your system is tailored to your business needs.
- Map the Manufacturing Process: Analyze your current production processes to identify critical control points where traceability data should be collected. Mapping the entire workflow, from raw material sourcing to product delivery, ensures comprehensive data coverage and helps identify areas for improvement.
- Choose the Right Technology: Choose a traceability solution that aligns with your manufacturing requirements and is scalable for future growth. Advanced tools, such as cloud-based manufacturing execution systems (MES), enterprise resource planning (ERP ) integrations, and Internet of Things (IoT) devices, offer real-time tracking, automated data collection, and seamless scalability.
- Standardize Data Collection and Labeling: Implement a consistent method for capturing and recording data throughout production. Label raw materials, components, and finished products with barcodes, RFID tags, or QR codes. Standardized labelling ensures accuracy and facilitates seamless data integration across systems.
- Train Your Workforce: Educate your employees on the importance of traceability and provide training on using the new system effectively. A well-informed workforce is essential for accurate data entry, process consistency, and system adoption across all levels of the organization.
- Integrate with Existing Systems: Ensure the traceability system integrates seamlessly with other manufacturing systems, such as inventory management, quality control, and supplier management platforms. Integration minimizes duplication of effort and provides a unified view of production data.
- Establish a Feedback and Improvement Loop: Continuously monitor the performance of your traceability system and gather feedback from stakeholders. Use this information to identify bottlenecks, refine processes, and improve system performance.
Traceability systems drive significant improvements in quality control, compliance, and operational efficiency, making them indispensable for manufacturers navigating today’s dynamic markets. With robust systems in place, businesses can reduce risks, optimize resource use, and strengthen their position by meeting evolving regulatory and customer expectations.
Investing in a future-ready traceability solution provides manufacturers with the adaptability to grow and succeed while maintaining high standards of transparency and accountability. This foundation ensures long-term success and positions organizations as leaders in delivering reliable, high-quality products.
Overcoming Challenges in Manufacturing Traceability Adoption
Implementing traceability in manufacturing systems can pose several challenges, but proactive strategies ensure these obstacles are effectively addressed. Resistance to change is often a significant hurdle, as employees and stakeholders may be hesitant to adopt new technologies and workflows. To overcome this, manufacturers need to prioritize employee training and highlight the long-term benefits of traceability , such as enhanced product quality, operational efficiency, and compliance.
System integration complexities can also arise, particularly when connecting traceability solutions with legacy equipment, ERP platforms, or other manufacturing systems. Seamless integration requires careful planning and selecting scalable, adaptable technologies that align with operational goals. Manufacturers should collaborate with technology providers to design solutions that bridge the gap between existing processes and modern traceability requirements.
Data accuracy and security management remain critical for successful traceability adoption. Incomplete or inaccurate data can undermine the system’s effectiveness, while inadequate security measures leave businesses vulnerable to breaches. Establishing standardized data collection protocols and leveraging secure cloud-based solutions ensures reliable, accessible, and protected information. These steps position manufacturers to unlock the full potential of traceability, improving compliance, customer trust, and operational resilience.
Future-Proof Strategies for Manufacturing with Traceability
Adopting traceability systems that can evolve with changing industry demands ensures manufacturers remain secure while safeguarding operational efficiency. Future-proof strategies enable businesses to anticipate challenges, integrate innovative technologies, and meet the needs of complex global markets. Below are key strategies that manufacturers can implement to future-proof their traceability efforts.
Embrace Emerging Technologies
Leveraging advanced technologies like artificial intelligence (AI), blockchain, and the Internet of Things (IoT) strengthens traceability systems by enhancing data collection, accuracy, and security. AI-powered analytics can process large datasets to identify trends and optimize production workflows, while blockchain ensures tamper-proof records for material and product tracking. IoT devices provide real-time monitoring of production equipment, materials, and shipments, delivering higher visibility and control.
Prioritize Sustainability and Ethical Sourcing
Traceability systems should align with sustainability goals by enabling manufacturers to track environmental impact and ensure compliance with ethical sourcing practices. Tools that monitor carbon footprints, waste reduction efforts, and responsible material sourcing address regulatory demands and appeal to environmentally conscious consumers. Manufacturers can use traceability data to demonstrate their commitment to sustainability and build trust with stakeholders.
Design for Scalability and Flexibility
A future-ready traceability system must be capable of scaling with business growth and adapting to new requirements. Cloud-based platforms offer the flexibility to handle increasing data volumes and integrate with evolving technologies. Modular designs allowing incremental upgrades and expansions enable businesses to respond quickly to market changes without overhauling their systems.
Foster Collaboration Across the Supply Chain
Collaboration between suppliers, manufacturers, and distributors is essential for creating a seamless traceability framework. Sharing data and standardizing practices across the supply chain improves visibility and ensures that all stakeholders contribute to maintaining quality and compliance. Manufacturers should establish partnerships prioritizing transparency and mutual accountability to strengthen the overall traceability ecosystem.
Invest in Workforce Development
As traceability systems become more advanced, the workforce must adapt to effectively manage and operate these tools. Manufacturers should provide ongoing training to ensure employees are proficient in using new technologies and interpreting traceability data. Building a skilled workforce not only maximizes the benefits of traceability but also empowers employees to contribute to continuous improvement initiatives.
Future-proofing traceability requires manufacturers to combine innovation, adaptability, and collaboration. These strategies position businesses to maintain compliance, enhance efficiency, and drive customer confidence even as the industry evolves.
Manufacturers worldwide embrace cloud-based solutions to achieve efficiency, precision, and scalability. At 42Q, we combine decades of manufacturing expertise with cutting-edge technology to deliver innovative, connected manufacturing. Our flexible, cloud-native MES platform enhances visibility, streamlines operations , and accelerates digital transformation. Discover how our solutions can empower your factory to achieve its full potential.
Key Takeaways
- Traceability in manufacturing ensures visibility across the entire production lifecycle, improving quality control, compliance, and supply chain transparency.
- Lot, material, and product traceability serve different purposes, addressing batch consistency, raw material tracking, and end-to-end product documentation.
- Implementing scalable traceability systems enhances efficiency and risk management, enabling businesses to respond to recalls or defects with precision.
- Advanced technologies like IoT, blockchain, and cloud-based platforms strengthen traceability, delivering real-time data and improving process optimization.
- Future-proof traceability strategies focus on sustainability, workforce development, and collaboration, ensuring long-term operational success and adaptability.
FAQs
Industries like medical devices, automotive, aerospace, and food manufacturing rely heavily on traceability systems to meet stringent safety standards, improve quality control, and manage recalls efficiently. Additionally, sectors such as clean energy and semiconductors benefit from enhanced supply chain transparency.
Traceability ensures that manufacturers document every stage of production, enabling them to meet regulatory requirements with detailed audit trails. It also helps businesses maintain certifications by verifying material origins, quality standards, and safety protocols.
Advanced technologies like cloud-based MES platforms, IoT devices, and blockchain improve traceability by enabling real-time data tracking, automating processes, and ensuring tamper-proof records. These tools provide unparalleled visibility and scalability.
By identifying inefficiencies and monitoring material usage, traceability minimizes waste in production. It prevents overproduction, reduces inventory costs, and allows manufacturers to pinpoint defects early, avoiding large-scale product losses.
Yes, traceability systems provide insights into sourcing practices, carbon footprints, and material usage, helping manufacturers align with sustainability initiatives. Transparent supply chains also enable ethical sourcing and compliance with environmental standards.
11 Considerations for
Choosing an MES
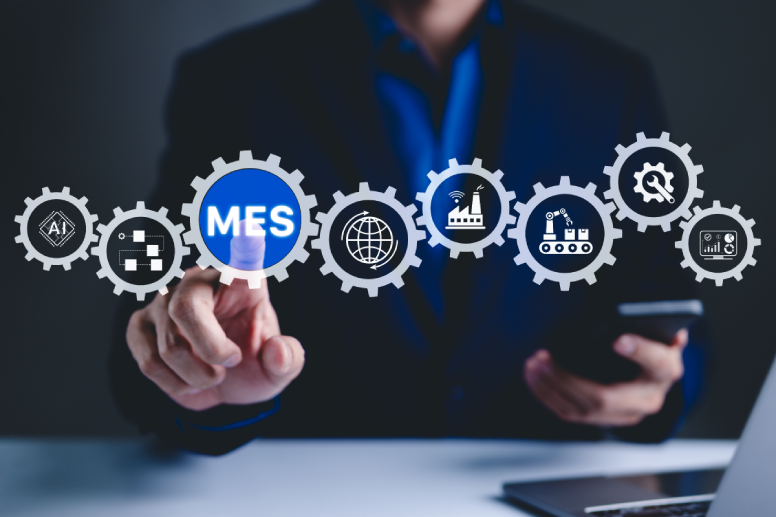
11 Considerations for Choosing an MES
Selecting a manufacturing execution system (MES) is one of the most impactful decisions a manufacturing company can make.
With new manufacturing technologies, an MES provides the tools needed to streamline processes, facilitate compliance, and drive data centric decisions. However, not all MES solutions are created equal, and choosing one requires careful consideration of various factors to meet your unique business needs. A well-chosen MES can optimize workflows, enhance visibility, and empower your factory to achieve its full potential.
What is an MES?
A manufacturing execution system is an advanced digital platform designed to manage and optimize production processes in real time. Acting as the connective tissue between enterprise resource planning (ERP) systems and the shop floor, an MES provides unparalleled visibility into production workflows while automating and standardizing key operations. This ensures efficiency, reduces errors, and allows for proactive problem-solving.
Its core functionalities include real-time tracking of production data, quality control management, and end-to-end product traceability. An MES integrates seamlessly with equipment and software across the factory, creating a unified ecosystem that enables informed decision-making. An MES facilitates adherence to regulations while maintaining robust documentation and audit trails for industries with stringent compliance needs—such as medical devices, aerospace, and automotive.
Beyond operational oversight, an MES delivers actionable insights through advanced analytics, allowing manufacturers to predict equipment maintenance needs, refine scheduling, and optimize resource allocation. Whether managing multi-site operations or scaling production, an MES is an indispensable tool for achieving consistency and productivity in manufacturing.
Why Should You Implement an MES?
Implementing an MES is a transformative step for any manufacturing organization seeking to streamline operations, improve quality, and stay innovating. Operational inefficiencies and compliance risks within manufacturing ecosystems can quickly escalate costs and hinder growth. An MES addresses these challenges by offering a real-time centralized platform to monitor and manage production, ensuring seamless coordination between teams, systems, and machinery.
- Real-time visibility: Full transparency into production processes, enabling quick responses to potential bottlenecks.
- Improved quality control: Automated inspections and traceability tools to reduce defects and enhance product standards.
- Regulatory compliance: Built-in features to support adherence to industry regulations.
- Operational efficiency: Reduction in downtime and waste, with improved resource utilization.
- Global standardization: Consistency in operations across plants, regardless of location.
- Enhanced decision-making: Data-driven insights to refine planning, scheduling, and forecasting.
- Better customer satisfaction: Faster delivery times and reliable quality outcomes.
Leveraging the capabilities of an MES enables manufacturers to achieve higher productivity, minimize risks, and drive profitability while ensuring long-term scalability and innovation. An MES resolves immediate operational pain points and positions manufacturers for future success through improved agility, enhanced analytics, and scalable technology infrastructure.
11 Considerations for Choosing an MES
Selecting the right MES is not just about addressing immediate manufacturing needs—it’s a strategic decision that will impact operational efficiency, scalability, and long-term growth. The process involves evaluating numerous factors to ensure the solution aligns with your unique workflows, compliance requirements, and business goals.
1. Define Your Business Needs
Understanding your business's unique requirements is the foundation of selecting an MES. Start by assessing your manufacturing goals, production challenges, and existing processes to determine the specific capabilities you need in a system.
Consider whether your operations prioritize high-volume production, customization, regulatory compliance, or advanced analytics. Do you need specific functionality like equipment integration, product traceability, or defect tracking? If you operate across multiple locations, assess whether centralized visibility is a priority.
Defining these needs ensures the MES you choose aligns with your operational goals and delivers measurable outcomes. A clear understanding of your priorities narrows your options and sets the stage for long-term success.
Key takeaway: The right MES starts with deeply understanding your operational pain points and strategic goals. Defining these allows you to focus on solutions that deliver tangible benefits and align with your growth trajectory.
2. Evaluate Customization Options
Manufacturing operations vary widely between industries, and a one-size-fits-all MES rarely delivers the efficiency and precision modern manufacturers require. Customization ensures the system adapts to your workflows rather than forcing your processes to fit rigid software constraints.
Look for an MES that allows configurable workflows, tailored reporting templates, and adjustable dashboards to meet the specific demands of your production environment. Assess whether the vendor offers industry-specific features, such as compliance tracking for medical devices or batch traceability for food manufacturing. This flexibility helps ensure the MES changes with your business, addressing current and future needs.
Standardization across facilities may also require some degree of customization. For companies managing multi-location operations, the ability to implement site-specific configurations without losing overarching visibility is critical. Flexibility in adapting to unique process flows can reduce the need for costly workarounds or third-party integrations.
Key takeaway: A customizable MES aligns directly with your processes, enabling seamless adoption and maximizing ROI. Systems that fail to adapt to your operations risk inefficiencies, employee resistance, and higher operational costs.
3. Assess Integration Capabilities
An MES does not operate in isolation—it must integrate seamlessly with your existing technology ecosystem. Manufacturing environments often involve a complex web of ERP systems , warehouse management systems (WMS), and various types of shop-floor equipment. Ensuring smooth integration is essential for leveraging the full potential of an MES.
Evaluate whether the MES supports standard integration protocols, such as APIs or OPC Unified Architecture (UA). Compatibility with your existing ERP is especially critical, as these systems often share production schedules, inventory, and order fulfillment data. Additionally, assess whether the MES can communicate with legacy equipment and newer Industry 4.0 technologies like IoT devices or predictive maintenance tools.
Effective integration minimizes data silos, enabling real-time data flow across all connected systems. This connectivity drives more informed decision-making and reduces manual interventions, increasing operational efficiency.
Key takeaway: The MES you choose should integrate effortlessly with existing systems and equipment to create a unified ecosystem. Poor integration can lead to costly delays, inefficiencies, and missed opportunities for optimization.
4. Consider Scalability Features
Manufacturing is rarely static, and your MES should accommodate current and future needs. Scalability ensures the system can support business growth through increased production volume, new product lines, or expanding operations across multiple sites.
Cloud-based MES solutions often provide the most flexible scalability. These systems allow you to add users, modules, or functionalities without significant infrastructure investment. On-premise solutions, while still viable for some manufacturers, may lack this flexibility and require costly upgrades to expand capabilities.
Scalability is significant for industries experiencing seasonal production peaks or unpredictable demand fluctuations. A robust MES should handle workload surges without compromising performance, ensuring seamless operations regardless of production demands.
Key takeaway: A scalable MES grows with your business, preventing costly system replacements and ensuring long-term alignment with your operational goals.
5. Prioritize Regulatory Compliance
For manufacturers in regulated industries, compliance is non-negotiable. An MES must include features that enable traceability, documentation, and audit readiness to facilitate adherence to industry standards and legal requirements.
Evaluate whether the system offers automated record-keeping, electronic signatures, and audit trail functionality. For example, medical device manufacturers may require compliance with ISO 13485 or FDA 21 CFR Part 11, while automotive manufacturers may need features supporting IATF 16949 standards. Ensure the MES can handle regional and global regulations if your business operates across multiple jurisdictions.
Non-compliance can lead to severe penalties, operational disruptions, or damage to your reputation. An MES with built-in compliance features reduces the risk of human error and simplifies the process of maintaining regulatory standards.
Key takeaway: Choose an MES with comprehensive compliance tools tailored to your industry, safeguarding your business against legal and operational risks.
6. Analyze Cost vs ROI Potential
Investing in an MES requires careful consideration of both initial costs and long-term returns. While upfront expenses such as licensing fees, implementation, and training are essential, the system's ability to deliver measurable benefits over time is the fundamental determinant of its value.
Begin with a detailed cost analysis that includes both direct and indirect expenses. Direct costs encompass software licenses, hardware (if needed), and consulting fees. Indirect costs, such as lost productivity during implementation or maintenance requirements, should also be considered. Balance these expenses against the potential ROI, including reductions in downtime, enhanced quality control, and improved productivity.
A strong MES often pays for itself through operational efficiencies. For instance, reducing scrap rates, minimizing errors, and accelerating production cycles directly impact the bottom line. Evaluate whether the vendor provides ROI estimates or case studies showcasing measurable outcomes from similar deployments in your industry.
Key takeaway: Choose an MES that delivers long-term value through enhanced efficiency and measurable financial gains. An upfront investment that results in sustained cost savings and increased productivity ensures the system pays for itself over time.
7. Review Vendor Support Quality
The success of an MES implementation depends heavily on the level of support the vendor provides. Comprehensive training, prompt troubleshooting, and proactive updates are essential for ensuring smooth operations after deployment.
Research the vendor’s reputation for customer service, including response times and problem-resolution rates. Evaluate whether they offer dedicated support teams, live assistance, or self-service resources. Some vendors provide additional services like continuous training or on-site visits, which can be invaluable during the early stages of adoption.
Ongoing support is equally important. You may require system updates, additional training, or new integrations. A vendor with a proven track record for long-term partnership ensures your MES remains relevant and functional as your business grows.
Key takeaway: Reliable vendor support ensures seamless adoption and consistent performance, minimizing downtime and maximizing the system’s effectiveness.
8. Plan Implementation Timeline
A well-structured implementation plan minimizes disruptions and ensures a successful MES rollout. Before selecting a system, assess whether the vendor provides a clear timeline with milestones and deliverables. An accelerated implementation may be beneficial but should not come at the expense of system reliability or thorough testing.
Collaborate with stakeholders to align the timeline with production schedules, ensuring minimal impact on operations. A phased rollout, where the MES is deployed to select departments or locations before full implementation, can help identify potential challenges early.
An effective timeline should include post-implementation support, user training and initial troubleshooting. Ensuring your team is comfortable with the system prevents delays and maximizes its impact.
Key takeaway: A realistic implementation plan tailored to your operations ensures a smooth transition and reduces downtime, allowing you to achieve faster results without compromising reliability.
9. Ensure Security Standards Compliance
As manufacturing highly relies on digital systems, cybersecurity has become a critical consideration. An MES must protect sensitive production data, intellectual property, and customer information from potential breaches or cyberattacks.
Choose a system with robust security features, including data encryption, user authentication, and role-based access controls. If the MES is cloud-based, confirm that it complies with industry security standards such as ISO 27001 or SOC 2. Manufacturers handling government contracts or regulated industries should also evaluate the system’s compliance with regional standards, such as ITAR or GDPR.
Proactive security measures prevent costly disruptions and protect your business’s reputation. Additionally, built-in disaster recovery and backup capabilities ensure operational continuity during a cyber incident.
Key takeaway: A secure MES protects critical data and operations from external threats, safeguarding your business and reputation.
10. Monitor Analytics and Reporting Tools
Real-time analytics and robust reporting capabilities are essential features of any MES. These tools provide actionable insights that help manufacturers identify inefficiencies, track performance, and make informed decisions.
Look for systems with customizable dashboards, automated reporting, and real-time data visualization. Advanced analytics capabilities, such as predictive maintenance or quality trend analysis, enhance decision-making and operational efficiency.
An effective MES should integrate with business intelligence platforms to consolidate data from multiple sources. This integration enables a holistic view of operations, empowering leadership teams to develop strategies based on accurate, real-time information.
Key takeaway: An MES with strong analytics and reporting capabilities enhances visibility, supports informed decision-making, and drives continuous improvement in manufacturing processes.
11. Align with Long-Term Business Goals
Selecting an MES is not just a tactical decision—it’s a strategic investment. The system must align with your company’s long-term objectives, such as scaling production, entering new markets, or adopting emerging technologies like IoT or AI.
Evaluate whether the MES vendor offers a roadmap for future enhancements, including new modules or integrations. A system that changes with your business ensures sustained value and eliminates the need for costly replacements. Consider how the MES can support broader goals, such as sustainability initiatives or digital transformation strategies.
When an MES aligns with your vision, it becomes a foundational tool for achieving both short-term gains and long-term growth.
Key takeaway: An MES that supports your long-term objectives ensures scalability and sustained competitiveness, enabling your business to adapt.
Considerations when choosing an MES should address a specific element of manufacturing complexity, from ensuring seamless system integration to prioritizing regulatory compliance and long-term scalability. Whether you operate a single facility or manage global operations, selecting the best MES is critical to driving measurable improvements and supporting your growth vision.
Measuring Successful MES Implementation
A successful MES implementation is measured by how well it integrates into existing operations and by the tangible improvements it delivers over time. Key performance indicators (KPIs) provide a clear framework for evaluating the system’s impact on productivity, quality, and overall operational efficiency.
Critical metrics to track include production cycle times, defect rates, and equipment utilization rates. For companies focusing on compliance, metrics like audit readiness and traceability coverage are essential indicators of success. Employee adoption rates should also be monitored to ensure the system is used effectively across departments.
Beyond immediate metrics, the accurate measure of success lies in how well the MES supports long-term goals. For instance, improved scalability, better decision-making enabled by real-time analytics, and enhanced customer satisfaction reflect the broader value of a well-chosen MES. Regularly revisiting these metrics ensures the system continues to align with business objectives, providing sustained benefits over time.
Manufacturers worldwide embrace cloud-based solutions to achieve efficiency, precision, and scalability. At 42Q, we combine decades of manufacturing expertise with cutting-edge technology to deliver smart connected manufacturing. Our flexible, cloud-native MES platform enhances visibility, streamlines operations, and accelerates digital transformation. Discover how our solutions can empower your factory to achieve its full potential.
Key Takeaways
- Identifying specific business needs ensures the MES aligns with your manufacturing goals and addresses unique challenges effectively.
- Customizable and scalable MES platforms support long-term growth by adapting to changing processes and production demands.
- Seamless integration with existing ERP systems, IoT devices, and legacy equipment maximizes the value of the MES.
- Built-in compliance features ensure regulatory requirements are met, reducing risks and maintaining operational continuity.
- Real-time analytics and robust reporting tools empower data-driven decision-making and continuous process improvement.
FAQs
An MES is designed to monitor and manage manufacturing processes in real time, bridging the gap between enterprise resource planning systems and shop-floor operations. It ensures production efficiency, enforces quality standards, and provides actionable insights to optimize workflows.
MES software automates manual processes, tracks real-time production data, and identifies inefficiencies such as downtime or bottlenecks. This leads to faster cycle times, reduced waste, and better resource utilization, making operations more efficient and cost-effective.
Industries like automotive, aerospace, medical devices, and consumer electronics see significant value from an MES due to their need for traceability, quality control, and compliance. However, any manufacturer aiming to streamline production and improve scalability can benefit.
A cloud-based MES offers greater scalability, faster deployment, and reduced upfront costs compared to on-premise systems. It also enables global visibility and real-time access to data, making it ideal for multi-plant or growing businesses.
Focus on integration capabilities, customization options, scalability, compliance features, and ROI potential. These elements ensure the MES aligns with your operational goals and supports current and future business needs.
What is Open Source MES?
What is Open Source MES?
An open source Manufacturing Execution System (MES) is a software solution designed to manage and monitor manufacturing processes on the production floor, with its source code made publicly accessible. Unlike proprietary systems that require users to operate within vendor-defined constraints, open source MES systems empower manufacturers to customize features, integrate tools, and adapt functionalities according to their specific operational needs. This flexibility can benefit industries with unique workflows or production requirements.
MES systems are critical in bridging the gap between enterprise resource planning (ERP) systems and physical manufacturing processes. Manufacturers gain access to a community-driven ecosystem by leveraging an open source model, fostering continuous improvement and collaboration. This model is cost-effective and scalable, making it an appealing choice for manufacturers seeking to modernize their operations without committing to rigid vendor solutions.
Open source MES is central to understanding how open innovation can redefine manufacturing agility. Whether you’re looking for a solution to improve real-time visibility, enforce production workflows, or monitor machine performance, an open source MES system provides the flexibility and transparency to align technology with your strategic goals.
Benefits of Open Source MES Systems
Open source MES systems provide manufacturers with a cost-effective and highly flexible alternative to proprietary solutions, making them an appealing choice for businesses across industries. These systems empower manufacturers to adapt the software to their unique workflows and production needs, ensuring greater operational efficiency and alignment with organizational goals. By leveraging an open source approach, companies can eliminate expensive licensing fees, maintain complete control over system functionality, and benefit from the collaborative improvements of a global development community.
Beyond financial savings, open source MES systems foster innovation and autonomy, enabling manufacturers to integrate cutting-edge technologies such as IoT devices and AI tools without vendor restrictions. The benefits extend to improved scalability, transparency, and security, ensuring manufacturers can create a solution tailored to their present and future needs. Below are the core advantages that make open source MES systems a powerful tool for modernizing and optimizing manufacturing processes.
- Cost Savings: open source MES eliminates costly licensing fees associated with proprietary systems. Manufacturers can allocate resources to implementation and customization rather than software acquisition.
- Customization Flexibility: Accessing and modifying source code allows manufacturers to tailor the system to their specific processes, ensuring a perfect fit for unique production requirements.
- Vendor Independence: With an open source MES system, manufacturers avoid reliance on a single vendor, reducing risks related to support availability or pricing changes.
- Community Collaboration: Many open source MES projects benefit from active user communities that contribute improvements, support, and share best practices, creating a rich knowledge base.
- Rapid Innovation: Open source systems allow manufacturers to integrate the latest technological advancements, such as IoT (Internet of Things) and AI tools, without waiting for vendor-driven updates.
- Transparency and Security: Access to the source code offers complete visibility into how the system operates, enabling manufacturers to identify and address potential vulnerabilities promptly.
The wide-ranging benefits of open source MES systems extend beyond financial savings, providing organizations with the tools and adaptability to stay innovative in dynamic manufacturing environments. Prioritizing flexibility and innovation helps these systems meet the demands of modern production facilities with precision and efficiency.
Key Features of Open Source Manufacturing Execution Systems
Open source MES systems offer a robust suite of features designed to address the dynamic needs of manufacturing operations. These systems provide unparalleled flexibility and control, empowering manufacturers to tailor the solution to their unique production requirements. Unlike proprietary platforms, open source MES enables businesses to fully access, modify, and integrate system components, fostering high customization. From real-time monitoring and workflow management to advanced analytics and seamless integrations, these features provide the tools to improve efficiency, ensure quality, and optimize production processes.
Whether managing a single production line or coordinating operations across multiple facilities, open source MES systems deliver the functionality needed to adapt to demands. Each feature is carefully designed to enhance visibility, automate workflows, and streamline decision-making, ensuring manufacturers can achieve their operational goals precisely and confidently. Below is a closer look at the key capabilities that make open source MES systems a vital asset for modern manufacturing environments.
Real-Time Production Monitoring
Real-time production monitoring is a cornerstone of any open source MES system. This feature allows manufacturers to track key performance metrics such as machine efficiency, production throughput, and overall equipment effectiveness (OEE). Continuous monitoring ensures operators and managers can quickly detect and address inefficiencies or equipment malfunctions, reducing downtime and maximizing productivity. Real-time dashboards visually represent manufacturing data, offering critical insights for optimizing operational performance.
Customizable Workflow Management
Every manufacturing process is unique, and open source MES systems provide the flexibility to configure workflows to fit specific production requirements. This capability allows businesses to create dynamic task assignments, enforce production rules, and establish automated triggers for key processes. Custom workflows eliminate inefficiencies caused by rigid, one-size-fits-all systems, enabling manufacturers to streamline operations and improve throughput while ensuring consistent quality standards.
Seamless Integration with Existing Systems
Interoperability is essential for any MES system. open source MES platforms excel at integrating with a wide range of tools and systems, including ERP software, IoT devices, and legacy equipment. This integration eliminates silos by ensuring a continuous flow of data across the organization. Manufacturers gain the ability to synchronize production schedules with inventory management, improve supply chain visibility, and automate data collection, leading to more efficient and cohesive operations.
Comprehensive Traceability and Compliance Tools
Traceability features are vital for industries requiring strict adherence to regulatory standards, such as medical devices and automotive manufacturing. open source MES systems provide end-to-end traceability, allowing manufacturers to monitor raw materials, components, and finished products throughout the production lifecycle. Advanced reporting tools make meeting compliance requirements, managing recalls, and improving quality assurance easier. Customizable tracking systems offer additional flexibility, ensuring the solution fits unique operational and regulatory needs.
Modular and Scalable Architecture
The modular design of open source MES systems enables manufacturers to deploy the exact features they need while maintaining the ability to expand as operations grow. This scalability ensures businesses can adapt the system to accommodate new production lines, facilities, or technologies without significant disruptions. A modular architecture also reduces upfront costs by allowing companies to prioritize essential features during initial implementation.
Enhanced Security and Code Transparency
Access to the system’s source code ensures manufacturers fully control software security and customization. Unlike proprietary systems, open source MES platforms allow organizations to audit code for vulnerabilities, implement specific safeguards, and maintain compliance with internal and industry-specific security standards. This transparency fosters trust while empowering manufacturers to adapt the system as new security threats or operational requirements emerge.
Advanced Analytics and Predictive Insights
Many open source MES systems include tools for advanced analytics, enabling manufacturers to gain deeper insights into production performance. When paired with IoT data, predictive analytics capabilities help identify potential issues before they escalate, allowing manufacturers to optimize processes, improve resource allocation, and reduce waste. These tools help businesses stay competitive by making data-driven decisions that enhance efficiency and product quality.
These features represent the foundation of open source MES systems and their ability to transform manufacturing operations. From real-time monitoring to advanced analytics and customization, these tools equip businesses with the resources to address today’s challenges and position themselves for future success.
Comparing Open Source vs. Proprietary MES
The main difference between open source and proprietary Manufacturing Execution Systems (MES) lies in flexibility versus ease of implementation. Open source MES systems prioritize customization and transparency, giving manufacturers complete control over system integration and adaptation to unique requirements. In contrast, proprietary MES systems offer ready-made, vendor-managed solutions designed for quick deployment but with limited adaptability.
Selecting the right MES is a critical decision for manufacturers, as it impacts operational efficiency, scalability, and long-term costs. Open source systems provide manufacturers with robust customization options but often require advanced technical expertise. On the other hand, proprietary MES solutions simplify implementation and support, reducing the burden on internal teams while providing vendor-managed maintenance and security. Understanding these differences helps manufacturers choose the best option for their goals, resources, and production needs.
Feature | Open Source MES | Proprietary MES |
Cost Structure | Typically free to access, with costs related to implementation, customization, and maintenance. | Requires licensing fees, often with recurring costs for updates and support. |
Customization | It is fully customizable, allowing access to the source code for modifications to fit specific workflows. | Limited customization options, constrained by vendor-specific features and permissions. |
Vendor Dependency | Reduces reliance on a single vendor, fostering greater autonomy in system management. | Heavy dependence on vendors for updates, support, and scalability. |
Implementation Speed | It can vary depending on in-house expertise but may allow rapid adjustments with the right resources. | Standardized processes often enable quicker initial deployment but limit long-term flexibility. |
Security Transparency | Full access to the source code ensures visibility into potential vulnerabilities and security fixes. | Security features are managed exclusively by the vendor, with limited user transparency. |
Community Support | Backed by user communities offering shared insights, best practices, and collaborative development. | Vendor-provided support, often requiring additional fees for advanced services or custom needs. |
Open source MES systems empower manufacturers with flexibility, cost savings, and independence, making them ideal for businesses seeking tailored solutions. Proprietary MES systems cater to manufacturers prioritizing simplicity and pre-configured solutions, though often at a higher cost and with reduced customization options.
Choosing between the two depends on operational needs, available resources, and long-term business goals. Each system type offers distinct advantages, and the decision should align with the unique requirements of the manufacturing environment.
How to Implement an Open Source MES
Implementing an open source MES system requires a structured approach to ensure seamless integration and long-term success. Manufacturers must carefully evaluate their operational needs, allocate resources, and prepare their teams for the transition. Below is a step-by-step breakdown of the process to guide effective implementation.
Assess Operational Needs and Objectives
Manufacturers must clearly define their goals before selecting an open source MES system. This includes identifying pain points in current workflows, such as inefficiencies in production tracking, quality control issues, or data silos. A thorough needs assessment ensures the selected system aligns with immediate requirements and future growth objectives. Engaging key stakeholders, such as production managers and IT teams, during this phase is critical to capturing diverse perspectives.
Select the Right Open Source Platform
Choosing the right platform is essential for success. Manufacturers should evaluate potential open source MES systems based on features, compatibility with existing infrastructure, scalability, and community support. Reviewing case studies or success stories from similar industries can provide insights into which platforms offer the best fit. Additionally, manufacturers must consider licensing terms, as some open source platforms have specific usage guidelines.
Develop a Customization and Integration Plan
open source MES systems offer significant advantages in terms of customization. Manufacturers should work with in-house IT teams or external experts to tailor the system to their workflows. This may include modifying dashboards, integrating IoT devices, or linking the MES with ERP systems . A well-defined integration plan minimizes disruptions and ensures the system communicates effectively with other tools in the production environment.
Pilot and Test the System
Testing the system in a controlled environment allows manufacturers to identify potential issues before full deployment. Piloting the MES on a single production line or department provides valuable feedback on system performance, usability, and compatibility with existing processes. During this phase, teams can refine workflows, address technical challenges, and ensure the system meets operational standards.
Train Teams and Prepare for Deployment
Employee training is crucial to a successful MES implementation. Manufacturers should provide comprehensive training sessions for all users, including production operators, managers, and IT staff. Clear documentation, user guides, and hands-on workshops help teams understand the system's features and functionality. Practical training ensures employees are confident and prepared to use the system entirely.
Monitor and Optimize Post-Deployment
Continuous monitoring and optimization are necessary to maintain performance after deploying the open source MES system across the facility. Regular evaluations of system usage, data accuracy, and overall effectiveness help identify areas for improvement. Manufacturers can leverage community forums, feedback from team members, and system updates to keep the MES aligned with changing operational needs.
Implementing an open source MES requires strategic planning, collaboration, and a commitment to continuous improvement. These steps ensure that the system meets initial expectations and delivers long-term value through enhanced efficiency, visibility, and adaptability.
Future Trends for Open Source MES in 2025
Open source MES systems are advancing as manufacturers seek innovative, adaptable solutions to manage complex production demands. Artificial intelligence (AI) and machine learning are pivotal, enabling predictive maintenance, automated decision-making, and advanced analytics. These capabilities allow manufacturers to proactively identify inefficiencies, predict machine failures, and optimize workflows to enhance productivity and reduce downtime. IoT connectivity further drives transformation, allowing MES systems to integrate with a growing array of sensors and devices on the shop floor. This real-time data collection improves visibility into production processes, enabling faster adjustments and more precise monitoring of performance metrics.
Cloud-native architectures are also shaping the future of open source MES, offering unmatched scalability and flexibility. Cloud deployment supports remote access, centralized data management, and the ability to coordinate operations across multiple facilities, making it an essential feature for global manufacturers. Developers prioritize cybersecurity enhancements, with open source platforms integrating robust encryption, threat detection, and compliance tools to safeguard critical production data and prevent vulnerabilities.
Sustainability is emerging as a key trend, with open source MES systems incorporating tools to track energy consumption, measure carbon emissions, and monitor waste production. These features help manufacturers align with regulatory requirements and corporate sustainability goals, enabling more efficient resource usage and environmentally conscious production practices. The open source community also continues to expand, creating ecosystems of plugins, integrations, and community-driven innovations that make these systems even more versatile and future-proof.
Manufacturers worldwide are embracing open source MES systems to drive efficiency, adaptability, and innovation.
At 42Q, we combine decades of manufacturing expertise with cutting-edge technology to deliver smart connected manufacturing. Our flexible, cloud-native MES platform enhances visibility, streamlines operations, and accelerates digital transformation. Discover how our solutions can empower your factory to achieve its full potential.
Key Takeaways
- Customization is Key: Open source MES systems empower manufacturers with the ability to adapt workflows, integrate tools, and align processes to specific operational needs.
- Cost Efficiency: Eliminating licensing fees and enabling flexible resource allocation make open source MES systems a budget-friendly alternative to proprietary platforms.
- Real-Time Insights: These systems provide real-time data monitoring, helping manufacturers quickly identify inefficiencies and improve decision-making.
- Future-Ready Technology: Open source MES systems seamlessly integrate emerging technologies like IoT and AI, supporting long-term scalability and innovation.
- Global Collaboration: Open source MES systems benefit from community-driven development, ensuring continuous improvement, shared insights, and cutting-edge features.
FAQs
An open source MES is a software platform that manages and monitors manufacturing operations with fully accessible and modifiable source code. This level of transparency allows manufacturers to customize the system to meet their specific production needs while improving efficiency and operational control.
The primary difference lies in access and flexibility. Open source MES systems offer customizable source code, enabling manufacturers to modify features and integrate additional tools. Proprietary systems, while often more straightforward to deploy, limit customization and require adherence to vendor-defined structures.
Yes, open source MES systems can be highly secure when implemented correctly. Manufacturers can audit the source code for vulnerabilities, apply necessary updates, and leverage community-driven enhancements to ensure robust security measures are in place.
Industries such as automotive, medical devices, electronics, and aerospace benefit greatly from open source MES systems due to their need for advanced customization, regulatory compliance, and real-time production monitoring capabilities.
While open source MES eliminates licensing fees, costs may include implementation, customization, integration with existing systems, and ongoing maintenance. These expenses are often significantly lower than those of proprietary systems, making open source solutions a cost-effective choice for many manufacturers.
7 Benefits of Implementing
a Cloud MES
7 Benefits of Implementing a Cloud MES
A cloud-based MES can transform manufacturing operations by delivering advanced tools that simplify workflows, reduce operational expenses, and provide actionable insights through real-time data. These systems empower manufacturers to overcome challenges like scaling production, maintaining compliance, and improving overall efficiency—all while minimizing the need for costly hardware and on-site IT support.
This approach perfectly aligns with the needs of modern manufacturers, who require flexible, adaptable solutions to remain competitive in a demanding market. Because it can centralize operations, ensure data accuracy, and foster seamless collaboration across multiple facilities, a cloud MES has become essential for businesses aiming to optimize production and accelerate growth.
1. Cost Savings and Efficiency
A cloud MES eliminates the need for significant upfront investments in hardware and infrastructure, making it a cost-effective alternative to traditional systems. Instead of purchasing and maintaining servers, manufacturers can leverage a subscription-based model that spreads costs over time. This approach also reduces ongoing expenses, such as IT support and energy consumption.
With a cloud-based MES, manufacturers gain a solution to optimize production efficiency. Automated workflows, real-time monitoring, and advanced analytics help reduce waste, minimize downtime, and improve resource utilization. These efficiencies directly impact profitability, enabling manufacturers to focus financial resources on growth and innovation.
2. Scalable Operations for Growth
A cloud-based MES system is inherently scalable, allowing manufacturers to expand their operations without being constrained by physical infrastructure. Whether adding new production lines, facilities, or geographical locations, the system seamlessly adapts to increased demands.
Scalability ensures manufacturers can respond to market changes and customer demands without the delays or high costs associated with upgrading legacy systems. This flexibility allows for operational continuity and sustainable growth without disruption.
3. Improved IT Resource Utilization
Unlike traditional systems that require extensive in-house IT involvement, a cloud MES significantly reduces the burden on internal teams. The service provider handles routine tasks like software maintenance, updates, and troubleshooting, freeing up IT staff to focus on strategic initiatives.
This improved allocation of IT resources saves time and costs and enhances overall system reliability. Manufacturers benefit from consistent uptime and optimized system performance without the strain of managing complex technology infrastructures.
4. Real-Time Data for Better Decisions
A cloud-based MES provides real-time visibility into production processes, enabling manufacturers to make informed decisions quickly. Key performance indicators (KPIs), production metrics, and inventory levels are available anytime, empowering teams with actionable insights.
Access to real-time data enhances agility, allowing manufacturers to instantly identify issues, adjust workflows, and optimize operations. This level of responsiveness improves overall efficiency and ensures businesses can stay competitive in dynamic markets.
5. Enhanced Security and Compliance
Security is a top priority for manufacturers, especially those handling sensitive data or operating in regulated industries. Cloud MES providers invest in advanced security measures, including encryption, multi-factor authentication, and regular audits, to ensure data integrity and compliance.
Many cloud-based MES solutions are designed to meet stringent industry standards, such as ISO certifications or government compliance requirements. This level of security and compliance allows manufacturers to operate confidently, knowing their data and processes are protected.
6. Faster Deployment and Integration
Traditional MES systems often take months or even years to deploy. In contrast, a cloud MES can be implemented, often within weeks. This accelerated timeline allows manufacturers to begin realizing benefits almost immediately.
Cloud-based MES solutions are also designed to seamlessly integrate with existing enterprise systems, such as ERP platforms or IoT devices. This ensures minimal disruption during implementation and enables manufacturers to create a connected, data-driven production environment more quickly.
7. Support for Industry Regulations
Manufacturers in medical devices, aerospace, and automotive industries face strict regulatory requirements. A cloud MES simplifies compliance by offering built-in features such as traceability, audit trails, and electronic documentation.
These tools streamline regulatory reporting and reduce non-compliance risk, saving manufacturers time and resources. With a cloud-based MES, manufacturers can stay ahead of industry standards while maintaining operational efficiency.
Cloud MES solutions provide measurable benefits across all aspects of manufacturing, from cost savings to enhanced security and compliance. Each of these advantages supports long-term growth and operational excellence, empowering manufacturers to modernize their processes and meet the demands of a competitive market.
How a Cloud MES Drives Scalability
A cloud-based MES is designed to grow alongside your business, offering unparalleled flexibility and adaptability for manufacturing operations. Unlike on-premises systems, which are limited by physical infrastructure and resource constraints, a cloud MES allows manufacturers to scale up or down based on operational needs without requiring significant investments in new hardware or IT infrastructure.
Scalability is particularly beneficial for manufacturers with multi-plant operations or expansion plans. A cloud MES provides centralized visibility and control across all locations, enabling seamless integration of new facilities or production lines. This centralized approach ensures consistent quality and efficiency, even as operations become more complex.
Moreover, cloud MES solutions are equipped to handle fluctuations in demand. Whether a business is experiencing seasonal production spikes or a long-term increase in orders, the system can effortlessly adjust resources to accommodate changes. This agility ensures manufacturers can maintain productivity and meet customer expectations, even during growth or market uncertainty.
Manufacturers worldwide embrace cloud-based solutions to achieve efficiency, precision, and scalability. At 42Q, we combine decades of manufacturing expertise with cutting-edge technology to deliver smart connected manufacturing. Our flexible, cloud-native MES platform enhances visibility, streamlines operations, and accelerates digital transformation. Discover how our solutions can empower your factory to achieve its full potential.
Key Takeaways
- A cloud-based MES reduces upfront costs and ongoing expenses while providing a subscription-based pricing model.
- Manufacturers can scale operations easily to meet growth demands without significant infrastructure investments.
- Real-time data and analytics enable quicker, more informed decision-making, improving operational efficiency.
- Advanced security features protect sensitive manufacturing data and support compliance with industry regulations.
- Faster deployment and seamless integration with existing systems accelerate production optimization.
FAQs
A cloud MES is a Manufacturing Execution System hosted on remote servers, offering centralized tools for production monitoring, workflow optimization, and data analysis. It connects to enterprise systems and provides real-time access to manufacturing data, enabling informed decisions from any internet-connected device.
Cloud-based MES improves efficiency by automating workflows, reducing downtime, and enhancing production visibility. It optimizes resource use, reduces waste, and provides actionable insights through real-time monitoring and advanced analytics.
Yes, cloud-based MES solutions are designed with advanced security features like encryption, multi-factor authentication, and regular audits. These measures protect sensitive data and ensure compliance with industry regulations, making them ideal for aerospace and medical devices.
Cloud MES solutions are particularly beneficial for industries requiring high scalability, traceability, and compliance, such as automotive, aerospace, medical devices, and consumer electronics. These systems support multi-facility operations and adapt to changing production needs.
Cloud-based MES systems can be deployed much faster than traditional systems, often within weeks. Their rapid implementation minimizes downtime and allows manufacturers to optimize production and gain value quickly.
AI and Machine Learning for
Manufacturing in 2025
What Are AI and Machine Learning in Manufacturing?
AI and machine learning have enhanced manufacturing by integrating advanced data processing with decision-making automation. AI involves creating systems that simulate human intelligence, such as reasoning, problem-solving, and learning from data. Machine learning, a subset of AI, uses algorithms to identify patterns and continuously improve performance without requiring manual reprogramming. These technologies allow manufacturers to move beyond traditional automation, enabling more innovative, adaptive, and efficient operations.
In manufacturing, AI and machine learning are applied to a wide range of tasks, such as optimizing production schedules, forecasting equipment failures, improving product quality, and streamlining supply chains. They also empower predictive analytics, helping companies make informed decisions based on real-time data. This results in fewer errors, reduced downtime, and more efficient resource utilization.
Leveraging machine learning in manufacturing helps companies implement proactive strategies, such as detecting potential defects during production, predicting demand changes, and managing inventories more effectively. These capabilities improve productivity and facilitate long-term adaptability and innovation.
Key Benefits of AI and Machine Learning for Manufacturers
AI and machine learning are delivering impactful benefits to manufacturers , driving efficiency, cost savings, and improved decision-making across the production process. These technologies provide actionable insights, reduce downtime, and enhance operational precision.
Improved Operational Efficiency
AI and machine learning help streamline manufacturing operations by automating routine tasks, optimizing workflows, and improving resource allocation. Advanced algorithms identify inefficiencies in production lines, enabling manufacturers to address issues before they escalate. With predictive models, companies can reduce waste and ensure that materials and labour are utilized effectively.
Predictive Maintenance and Reduced Downtime
Through predictive maintenance, machine learning algorithms analyze historical and real-time data to forecast equipment failures. This minimizes unplanned downtime, which can be costly for manufacturers. Preventive measures are triggered based on accurate forecasts, ensuring equipment remains operational while extending its lifespan.
Enhanced Quality Control
Machine learning improves product quality by detecting defects early in the manufacturing process. Image recognition and anomaly detection technologies allow manufacturers to monitor production in real time, ensuring that each item meets the required specifications. This reduces errors, enhances customer satisfaction, and lowers production waste.
Real-Time Data Insights for Decision-Making
Manufacturers gain a competitive edge by leveraging real-time data insights. AI-powered systems analyze production data, providing actionable intelligence to optimize supply chains, monitor inventory, and respond to market demand changes. These insights support strategic decision-making and help companies stay agile in fluctuating environments.
Cost Reduction Across Operations
AI and machine learning contribute to cost savings by reducing manual intervention, waste, and energy consumption. Process optimizations identify cost-heavy activities and recommend more efficient approaches. Over time, these cost reductions increase profitability and drive long-term sustainability.
The advantages of AI and machine learning for manufacturers extend beyond operational improvements. These technologies create opportunities for innovation, enabling companies to continually enhance their processes and product offerings. With improved efficiency, predictive maintenance, and cost savings, manufacturers can strategically allocate resources, driving short-term gains and long-term growth.
7 Applications of AI and Machine Learning in Manufacturing
AI and machine learning offer transformative applications in manufacturing, addressing longstanding challenges and enabling more intelligent, more efficient operations. These technologies improve productivity across production lines and open new customization, sustainability, and innovation avenues. Manufacturers can anticipate disruptions, optimize resources, and deliver consistent quality by leveraging machine learning.
The following applications showcase how machine learning in manufacturing solves critical problems and creates measurable outcomes. Each use case highlights the versatility and practicality of integrating AI and machine learning into modern production processes.
- Predictive Maintenance: Machine learning analyzes sensor data from equipment to predict failures before they occur. This allows manufacturers to schedule maintenance proactively, reducing costly downtime and preventing unexpected disruptions.
- Quality Assurance and Defect Detection: AI-powered visual inspection systems identify flaws in real-time, ensuring products meet quality standards. These systems minimize human error, reduce waste, and enhance customer satisfaction by delivering consistent results.
- Demand Forecasting and Inventory Optimization: Machine learning models analyze historical sales data, market trends, and seasonal variations to predict demand accurately. This optimizes inventory levels, reducing storage costs and preventing stock shortages.
- Process Automation: Robotic systems powered by AI automate repetitive tasks such as assembly, welding, and material handling. This improves efficiency, reduces labour costs, and enhances safety by minimizing human involvement in hazardous environments.
- Supply Chain Optimization: AI enhances supply chain management by analyzing logistics, transportation, and supplier data. Machine learning predicts disruptions, streamlines procurement, and ensures that materials are delivered on time to meet production schedules.
- Energy Management: Machine learning identifies inefficiencies in energy consumption, recommending adjustments to minimize waste. This reduces energy costs and supports sustainability initiatives by lowering carbon footprints.
- Custom Manufacturing and Product Design: AI-driven systems enable manufacturers to customize products based on specific customer preferences. Machine learning optimizes the design process by analyzing customer feedback, prototyping data, and market trends.
These applications highlight how machine learning for manufacturing is advancing operational efficiency, product quality, and supply chain management. From predictive maintenance to custom manufacturing, the benefits extend across all stages of the production cycle. Manufacturers that adopt these innovations gain the tools that are complex challenges and meet the growing demand for higher-quality, sustainable production.
How to Implement AI and Machine Learning in Manufacturing
Successfully integrating AI and machine learning into manufacturing operations requires a methodical approach. These technologies depend on robust data systems, clear objectives, and workforce readiness to deliver their full potential. Identifying key areas where machine learning can address inefficiencies or enhance production quality is an essential first step.
Once priorities are established, investing in data infrastructure and expertise ensures the foundation for scalable implementation. Collaborating with industry experts and training your team further accelerates the process, making it easier to adopt cutting-edge solutions effectively. A phased implementation strategy reduces risks while optimizing return on investment.
Assess Operational Needs and Goals
Start by identifying specific pain points or inefficiencies within your manufacturing processes. Whether the goal is to reduce downtime, improve product quality, or optimize energy usage, defining clear objectives helps tailor AI and machine learning solutions to align with business priorities. Conduct a thorough evaluation of your operations to determine where these technologies can provide the most significant impact.
Develop Data Infrastructure
AI and machine learning depend on high-quality data to deliver actionable insights. Manufacturers must ensure their data infrastructure is robust, integrating inputs from sensors, IoT devices, and production systems. Building centralized data repositories and providing real-time data availability are critical steps in laying a foundation for success.
Partner with Technology Experts
Collaborating with AI and machine learning experts simplifies adoption and ensures access to the latest innovations. Technology partners can guide manufacturers in choosing the right tools, platforms, and algorithms tailored to their needs. Outsourcing or consulting with specialized teams also minimizes the risks associated with internal skill gaps.
Train Workforce and Build Expertise
Educating employees on AI and machine learning is crucial for long-term adoption. Offering training programs, workshops, and upskilling opportunities ensures your team can work effectively alongside these technologies. Building in-house expertise helps manufacturers adapt quickly and make informed decisions about expanding the scope of AI-driven initiatives.
Pilot and Scale Solutions
A pilot program allows manufacturers to evaluate the performance and ROI of AI and machine learning technologies on a smaller scale. Start with one or two processes, assess their outcomes, and refine strategies before scaling to other areas. This phased approach reduces implementation risks and ensures a smoother integration across the organization.
Implementing machine learning in manufacturing is a transformative process that requires careful planning and execution. Starting with smaller-scale pilot programs allows manufacturers to measure results and refine their strategies before expanding into more extensive operations. This phased approach reduces risks and maximizes impact.
As these systems integrate fully, manufacturers benefit from streamlined processes, improved quality, and actionable insights. With the right investments in training and infrastructure, machine learning becomes a valuable tool for driving innovation and efficiency across every aspect of manufacturing.
Overcoming Challenges in AI and ML Adoption
While the advantages of AI and machine learning in manufacturing are clear, integrating these technologies is not without challenges. Manufacturers face hurdles related to data quality, skill gaps, and cost considerations. Understanding and addressing these barriers is essential for achieving successful outcomes.
One of the primary challenges lies in data management. Manufacturing operations generate vast amounts of data, but much is unstructured or siloed across different systems. Poor data quality or inconsistent formats can hinder the accuracy of AI and machine learning models. Developing a unified data strategy and ensuring data accuracy is critical to overcoming this obstacle.
Skill gaps among employees also present a significant barrier. Many organizations lack the internal expertise to deploy and manage machine learning solutions. Training programs and external partnerships can bridge this gap, ensuring the workforce is equipped to maximize the value of these technologies.
Cost is another concern, particularly for small and medium-sized manufacturers. AI and machine learning require investment in infrastructure, tools, and talent. Implementing pilot programs and subscription-based pricing models can help manage these costs, enabling businesses to evaluate ROI before scaling solutions. Finally, resistance to change can slow adoption. Employees and leadership may be hesitant to embrace unfamiliar technologies. Open communication, clear demonstration of benefits, and involving stakeholders early in the process can foster buy-in and ensure smoother implementation.
2025 Trends: AI and Machine Learning in Manufacturing
The adoption of machine learning in manufacturing continues to change, with new trends reshaping how production processes are managed. As we move into 2025, manufacturers prioritize advanced technologies that enhance efficiency, sustainability, and adaptability. Machine learning is central to these developments, enabling smarter, data-driven operations that reduce costs and improve product quality.
Emerging trends such as digital twins, edge AI, and autonomous manufacturing systems demonstrate the growing reliance on machine learning for real-time decision-making and operational agility. These innovations highlight how manufacturers are building more intelligent factories that meet the demands of a dynamic industry.
- Increased Use of Digital Twins: Manufacturers are leveraging digital twins—virtual replicas of physical systems—to simulate processes and optimize performance. Machine learning models enhance these simulations, providing real-time insights into production and maintenance needs.
- Hyper-Personalized Production: AI is enabling manufacturers to offer customized products on a large scale. Machine learning analyzes customer preferences and automates adjustments in production lines to create tailored products efficiently.
- Autonomous Manufacturing Systems: Fully autonomous factories are becoming more prevalent. AI-powered systems integrate machine learning to manage production lines with minimal human intervention, improving efficiency and reducing costs.
- Sustainability and Energy Efficiency: Machine learning drives sustainable practices by optimizing energy usage and minimizing waste. Predictive models identify areas for energy conservation, helping manufacturers meet environmental goals and reduce costs.
- Advanced Robotics Integration: Collaborative robots (cobots) with machine learning capabilities enhance human-machine interactions on production floors. These robots adapt to dynamic environments and assist workers in performing complex tasks.
- Edge AI for Real-Time Decisions: The adoption of edge AI, which processes data locally rather than relying on centralized systems, is increasing. This trend allows manufacturers to make faster, data-driven decisions at the production site directly.
- Expanded Focus on Cybersecurity: As manufacturing becomes more connected, cybersecurity is a growing priority. Machine learning algorithms are being used to detect and prevent cyber threats, ensuring data integrity and operational continuity.
These trends emphasize the importance of machine learning in manufacturing, showcasing its role in fostering innovation, efficiency, and resilience. Technologies offer solutions to pressing industry challenges, from enabling hyper-personalized production to ensuring robust cybersecurity.
As adoption accelerates, delivering even greater value to manufacturers. Companies that integrate machine learning into their strategies today will be positioned to lead the industry, setting new standards for operational excellence and sustainability in the years ahead.
Measurable Business Impact of Machine Learning in Manufacturing
Machine learning in manufacturing drives measurable business outcomes that directly impact profitability, productivity, and sustainability. These benefits stem from the ability to process large datasets, automate critical tasks, and improve decision-making at every stage of the production cycle.
Manufacturers leveraging machine learning have reported significant reductions in operational costs. Predictive maintenance, for example, minimizes unplanned downtime and extends the lifespan of equipment. By addressing maintenance needs proactively, companies can lower repair expenses and prevent revenue losses caused by halted production lines.
Product quality and customer satisfaction have also improved due to machine learning applications. Advanced algorithms ensure consistent monitoring and early detection of defects, reducing waste and returns. This translates to enhanced brand reputation and stronger relationships with clients.
Machine learning enhances supply chain efficiency by optimizing logistics, demand forecasting, and inventory management. Accurate predictions reduce excess stock and ensure timely deliveries, resulting in cost savings and improved cash flow. Energy consumption is another area where machine learning delivers results, identifying inefficiencies and enabling manufacturers to cut energy costs while meeting sustainability goals.
Manufacturers worldwide are integrating advanced technologies to enhance efficiency, precision, and scalability. At 42Q, we combine decades of manufacturing expertise with cutting-edge cloud-based solutions to drive smart connected manufacturing. Our flexible, cloud-native MES platform empowers manufacturers with real-time visibility, streamlined operations, and accelerated digital transformation. Learn how our solutions can optimize your factory and unlock its full potential.
Key Takeaways
- Machine learning in manufacturing improves efficiency, enhances product quality, and reduces operational costs through automation and predictive analytics.
- Predictive maintenance powered by machine learning reduces unplanned downtime, extends equipment lifespan, and minimizes repair costs.
- Real-time data insights enable manufacturers to optimize supply chains, forecast demand, and respond effectively to market changes.
- Emerging trends such as digital twins, edge AI, and autonomous systems highlight the growing reliance on machine learning for more intelligent manufacturing.
- Strategic implementation, workforce training, and data infrastructure are crucial for overcoming adoption challenges and unlocking the full potential of machine learning.
FAQs
Machine learning in manufacturing uses data-driven algorithms to optimize production processes, enhance quality control, and predict maintenance needs. This technology processes large datasets from production lines to identify patterns and improve decision-making, resulting in cost savings and operational efficiency.
The main difference is that AI focuses on creating systems that mimic human decision-making, while machine learning enables systems to learn and improve from data. Both are used in manufacturing to optimize processes, but machine learning emphasizes continuous performance improvement.
Automotive, aerospace, medical devices, and consumer electronics benefit significantly from machine learning. These sectors rely on precision, efficiency, and scalability, all enhanced through machine learning applications like predictive maintenance and quality assurance.
Key challenges include managing large volumes of unstructured data, addressing workforce skill gaps, and handling infrastructure and training upfront costs. Overcoming resistance to change within organizations is another common barrier to successful adoption.
Machine learning identifies inefficiencies in energy usage, reduces waste, and improves resource allocation. These capabilities help manufacturers meet environmental goals while lowering costs and supporting sustainability across the production cycle.