5 Applications of MES in Industrial Automation
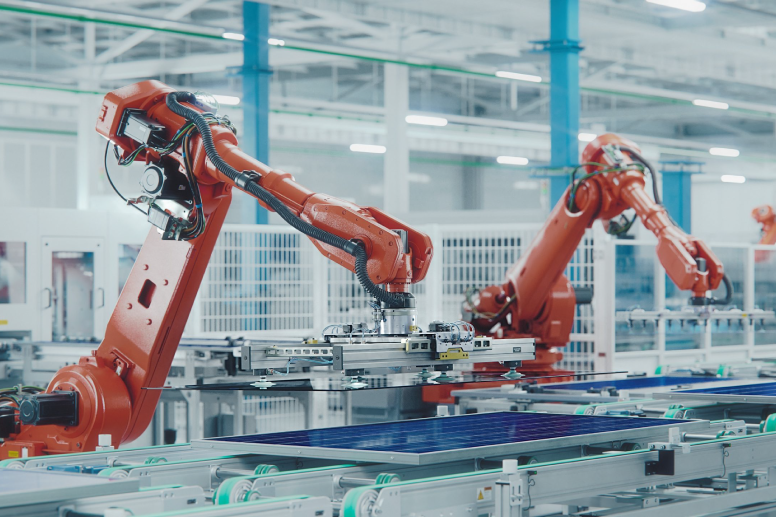
5 Applications of MES in Industrial Automation
Manufacturing Execution Systems (MES) have become a significant technology for bridging operational data with production goals. Many factories rely on real-time information to address production bottlenecks before they result in costly setbacks. Data synchronization across machinery, workers, and supply chains has proven vital for improving output consistency. Industry leaders consider MES an essential part of modern manufacturing strategies due to the immediate and measurable advantages it offers.
What is MES in Industrial Automation?
Manufacturing Execution Systems (MES) are specialized software platforms that track and manage production activities across industrial facilities. They gather real-time data from machines, workstations, and personnel to offer accurate process insights. This approach ensures that tasks run smoothly and that performance meets defined targets. An estimated 74% of manufacturers plan to implement MES or upgrade their existing solutions soon, reflecting the growing importance of this technology.
These systems play a pivotal role in industrial automation by coordinating data flows between the shop floor and higher-level business systems. This coordination supports improved scheduling, resource allocation, and process control. Manufacturers benefit from streamlined operations and real-time data insights, both of which contribute to higher output quality. MES in industrial automation applications provide a cohesive structure that ties together many facets of production, from raw materials to final products.
Importance of MES in Industrial Automation
Companies depend on real-time production insights to reduce waste and optimize efficiency. MES in industrial automation offers a direct line of sight into active workflows, allowing teams to anticipate bottlenecks before they escalate. This method keeps downtime to a minimum and enhances the overall reliability of manufacturing assets. It also helps unify data from multiple plants, leading to consistent process standards.
Another important function of MES is the ability to align production with business targets. It assists in calculating resource requirements, monitoring quality metrics, and tracking performance all in one place. This streamlined approach leads to time savings, cost reduction, and fewer errors. MES in industrial automation applications often lead to better returns on investment because they allow factories to maximize output within existing infrastructure.
5 Applications of MES in Industrial Automation
1. MES Application in Production Planning
Production schedules rely on accurate data to avoid misalignment and resource shortages. MES application in production planning helps gather relevant metrics from the shop floor to create realistic timetables. Planners gain visibility into lead times, batch sizes, and machine usage, which assists in prioritizing tasks effectively. This approach sets the stage for consistent throughput and minimizes schedule disruptions.
Better scheduling leads to faster time-to-market and higher customer satisfaction. The data analysis features of MES platforms also show exactly where to reduce inefficiencies or plan for expansions. This makes production more scalable as market demands fluctuate. Factories often see tangible returns with shorter cycles and fewer unexpected delays.
2. MES in Quality Control
Quality assurance teams benefit from an integrated system that flags deviations in real time. MES in quality control provides continuous monitoring of parameters like temperature, pressure, or component specifications. Alerts highlight variations outside the acceptable range, allowing prompt corrective actions. Workers no longer wait until the end of a batch to identify and fix issues.
Immediate error detection prevents additional defects and avoids rework costs. This improvement contributes to stronger regulatory compliance and boosts overall brand reputation. Better traceability also makes it easier to manage recalls when necessary, as each unit can be tracked through every production step. The measurable payoff is fewer quality failures and enhanced consumer trust.
3. MES for Inventory Management
Material shortages and surplus stock create unnecessary expenses. MES for inventory management offers accurate tracking of raw materials and finished goods. The software reconciles available stock with upcoming production requirements, reducing over-purchasing or last-minute scrambling. This clarity lowers warehousing costs and ensures materials are used effectively.
Digital records replace manual data entry and boost transparency across multiple sites. Operators can monitor consumption rates and plan restocking at optimal times. This method eliminates guesswork and leads to more predictable cost forecasts. The main benefit is a stable production flow that meets timelines without tying up capital in idle inventory.
4. MES in Maintenance Management
Production lines depend on consistent equipment performance, and downtime often leads to missed goals. MES in maintenance management provides a structured way to monitor machine health and schedule preventive tasks. Operators receive notifications when certain performance thresholds are exceeded or when usage hits defined limits. This precaution helps avoid major breakdowns by catching issues early.
Proactive maintenance extends the life of vital assets and promotes minimal interruptions to production. Managers can measure the effectiveness of maintenance activities with built-in analytics and adjust schedules as necessary. This means improved asset utilization and reduced overhead related to emergency repairs. Facilities often report better overall productivity and fewer unplanned shutdowns.
5. MES in Regulatory Compliance
Many sectors face specific standards for documentation, product traceability, and process safety. MES in regulatory compliance streamlines the capture and organization of necessary records. Production details are recorded automatically, reducing human error and ensuring consistent adherence to legal requirements. Audits become simpler because data remains centralized and easily accessible.
Automated logging of parameters lessens administrative burdens and cuts the time spent on manual inspections. Managers use the platform to verify that each lot meets industry guidelines and remains within approved ranges. This level of oversight is vital for consumer safety and brand credibility. The measurable outcome is reduced compliance-related costs and fewer legal complications.
Future Trends in Industrial Automation MES
The next wave of MES features is already shaping how factories measure performance and adapt to shifting demands. An industry analysis projects that the MES market could surpass $18 billion globally by 2030, highlighting the sustained momentum of these solutions. Emerging technology and advanced production strategies promise new efficiencies for many businesses. It is worthwhile to consider how upcoming developments may reshape your manufacturing roadmap.
- Greater integration with cloud services is expected to offer a faster time-to-value for new implementations. This approach reduces on-premise infrastructure and broadens accessibility.
- Augmented analytics in MES solutions will guide manufacturers to detect patterns and outliers quickly. This insight makes it easier to tweak operations on the fly.
- Collaborative robotics paired with MES have the potential to streamline workflows even further. Machine-generated data will feed into centralized dashboards for real-time visibility.
- Scalable IoT adoption could enhance data collection from sensors and devices across every step of production. The outcome is a stronger ability to forecast maintenance needs and manage workloads more precisely.
- Predictive modeling within MES may transform how factories refine production methods. Statistical projections of future performance will inform more targeted improvements.
Keeping pace with these trends can open new revenue streams and boost productivity. Adaptable MES platforms also help address uncertainties and market fluctuations more effectively. Each manufacturer must assess which features will yield the greatest impact based on business size and product complexity. The final goal is a stable, data-centric production model that supports continuous improvement.
Manufacturers worldwide are embracing cloud-based solutions to achieve efficiency, precision, and scalability. At 42Q, we combine decades of manufacturing expertise with cutting-edge technology to deliver connected manufacturing. Our flexible, cloud-native MES platform enhances visibility, streamlines operations, and accelerates digital transformation. Discover how our solutions can empower your factory to achieve its full potential.
Key Takeaways
- MES offers a unified way to manage production tasks, track resources, and monitor quality in real time.
- Integrated quality control within MES allows immediate detection of deviations, saving time and preventing rework.
- Inventory management becomes more cost-effective thanks to accurate material tracking and automated stock reconciliation.
- Maintenance notifications reduce downtime and prolong equipment lifespan by highlighting issues before failures occur.
- Regulatory compliance becomes simpler through automated record-keeping and standardized reporting workflows.
FAQs
A modern MES in industrial automation often includes real-time data capture, resource scheduling, and advanced analytics. It connects shop floor activities with management goals to maintain consistent production quality. Some solutions also integrate regulatory checks and automated reporting to keep businesses fully prepared for audits.
MES focuses on real-time production management, while other tools might handle specific tasks like equipment control. It provides a centralized view of processes, making it easier to spot bottlenecks or inefficiencies. Many manufacturers use MES alongside other systems to ensure continuous improvement across the entire facility.
MES tools offer preventive maintenance alerts based on equipment usage or performance metrics. This proactive strategy addresses potential malfunctions before they escalate. Reduced downtime leads to stable output and lower repair costs.
MES platforms automate record-keeping for processes, materials, and product history. Compliance checks become part of daily production routines, minimizing manual oversight. Many businesses see faster audits and fewer legal complications through these digital records.
MES can typically synchronize with enterprise resource planning systems through standardized APIs. This integration ensures that production data and business metrics reflect the same accurate information. Organizations often adopt such a setup to create a unified source of truth for operational decisions.